- Visit Us & Conduct Research
- Learning and Teaching
- Collection Highlights
- Language in Archival Descriptions
- Search our Collections
- Current Exhibits
- Previous Exhibits
- Special Collections
- Hours & Location
- Records Management
- School History

Polaroid versus Kodak: The Battle for Instant Photography
In 1947, Edwin Land unveiled a new process that would change the direction of amateur photography. It was a one-step, one-minute process that produced a fully finished photograph, something no one had ever seen before. This process was the beginning of a new genre of creating photographs called instant photography. The camera that was made for this in-camera process was the Land camera, named for the inventor of synthetic polarizer and the instant film process, and the founder of the Polaroid Corporation. Many different models of these first Polaroid cameras, as well as many later models, can be viewed at Special Collections in the Toronto Metropolitan University Library Archives, along with examples of different Polaroid photographs and instant film.
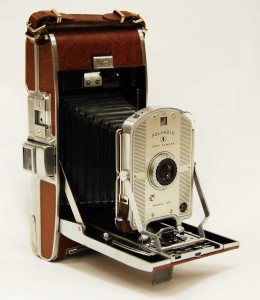
Polaroid dominated the market for this unique and easy photographic process that was a huge hit with amateur and professional consumers. However, also among the shelves of Special Collections, are examples of cameras, prints and film made by a number of different manufacturing companies who tried to get in on this popular genre of photography. None were nearly as successful, as no one could compete with the Polaroid name or their (what is often referred to as brilliant) marketing campaign. Stars such as Steve Allen , Jack Paar, Sir Lawrence Olivier, Mariette Hartley & James Garner , Blyth Danner, Candice Bergen , and The Muppets loaned their talents to promoting Polaroid products at a time when many stars were wary of doing commercials.
Then, in 1976, Polaroid was finally faced with their first real competitor for the instant photography market, an already established manufacturer of photographic equipment and materials: the Eastman Kodak Company. But Polaroid was prepared to deal with their competition, and by 1986, all of Kodak’s instant photography films and cameras had been pulled from the market, and Kodak ceased to manufacture any products that would directly compete with Polaroid’s instant photography niche.
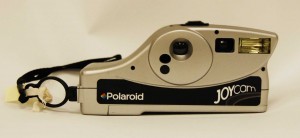
In fact, from 1963-1969, the Eastman Kodak Company had actually manufactured Polaroid’s instant film for them. At this time, Kodak was planning to introduce themselves to the market with a packfilm design, but later, after Polaroid released their SX-70 system in 1972, Kodak decided to go in a different direction and follow Polaroid with an integral type process instead. Although Kodak’s design differed from Polaroid’s in numerous ways, Polaroid filed suit against Kodak mere months after the release of the new products for the infringement of 12 Polaroid patents, accusing Kodak of illegally incorporating instant photography technology into their products. They claimed that during the 10 years the Eastman Kodak Company produced instant photography materials, they had cost the Polaroid Corporation $12 billion.
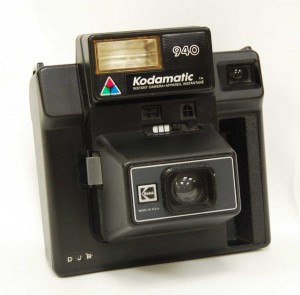
The final charges, announced in 1990, did not amount to $12 billion (what many considered a huge exaggeration), but at $909 million, they did come close to a billion. Found guilty on 7 of the 12 patent infringements after a trial in 1985, Kodak was forced out of instant photography the following year. The widely reported ruling was bad news for customers who had purchased a Kodak Instant camera.
The case did end favourably for Kodak though, especially after the high demands from Polaroid, who felt that Kodak had intentionally copied their technology. After a 14-year legal battle, in 1991 Kodak was finally ordered to pay Polaroid a total of $909 million, $925 million with interest, the largest settlement ever paid out until last year when Apple was awarded $1.049 billion in damages from Samsung infringements.
As part of the settlement, Kodak needed to provide compensation for customers who had bought any of their instant cameras between 1976 and 1986 and would no longer be able to purchase film to use in them. Owners of Kodak instant cameras were invited to call a toll free number and register themselves in order to receive a settlement packet. The packet was mailed out to those who registered, and provided customers with instructions of how to receive a rebate check or certificate, which often involved removing the name plate off of the front of the camera and mailing it in as proof of purchase.
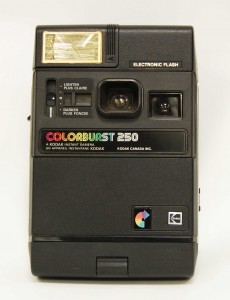
The Eastman Kodak Company did manage to recover after the Polaroid lawsuit, and with the sales of their popular movie films were able to regain their success. Unfortunately, the company was much slower with the uptake of the digital market, and in 2012 filed for bankruptcy due to lack of demand for the primary products made by their company, photographic films.
If you wish to pay tribute to some of Kodak’s instant photography cameras, you can make an appointment to come and see examples such as the Kodamatic 940, the Kodak Colorburst models 250 and 300, and the Kodak Trimprint 940 (with nameplates still intact!), as well as a wide range of instant cameras, film, and equipment made by Polaroid and other instant photography manufacturers that Special Collections keeps in their Heritage Camera Collection and the Kodak Canada Corporate Archives.
More information
Have a look at some of the original television advertisements for the Kodak instant Cameras.
For more detailed information on how the instant photography process works, have a look at this article by Tom Harris at How Stuff Works.
To make an appointment with Ryerson Library Special Collections, contact:
416-979-5000 ext 4996
Frezza, Bill. “Polaroid, Kodak, Apple: No One Escapes the Winds of Creative Destruction” Forbes, Sept 5, 2012. http://www.forbes.com/sites/billfrezza/2012/09/05/polaroid-kodak-apple-no-one-escapes-the-winds-of-creative-destruction.
Holusha, John. “Kodak Told it must Pay $909 Million.” New York Times (1923-Current File) , Oct 13, 1990. http://ezproxy.lib.ryerson.ca/login?url=http://search.proquest.com/docview/108482495?accountid=13631.
“Instant Camera Settlement.” Kodak Service and Support. http://www.kodak.com/global/en/service/faqs/faq0098.shtml.
“Kodak Settles Dispute With Polaroid the Fight Over Instant-photography Technology Took 15 Years and Cost Kodak $925 Million in Damages.” The Inquirer, July 16, 1991. http://articles.philly.com/1991-07-16/business/25783982_1_polaroid-patents-instant-cameras-instant-photography-business.
McCarty, Dawn and Beth Jinks. “Kodak Files for Bankruptcy as Digital Era Spells End for Film.” Bloomberg, January 19, 2012. http://www.bloomberg.com/news/2012-01-19/kodak-photography-pioneer-files-for-bankruptcy-protection-1-.html.
Wurman, Richard Saul. Polaroid Access: Fifty Years. [S.I.] : Access Press, 1989.
Share this:
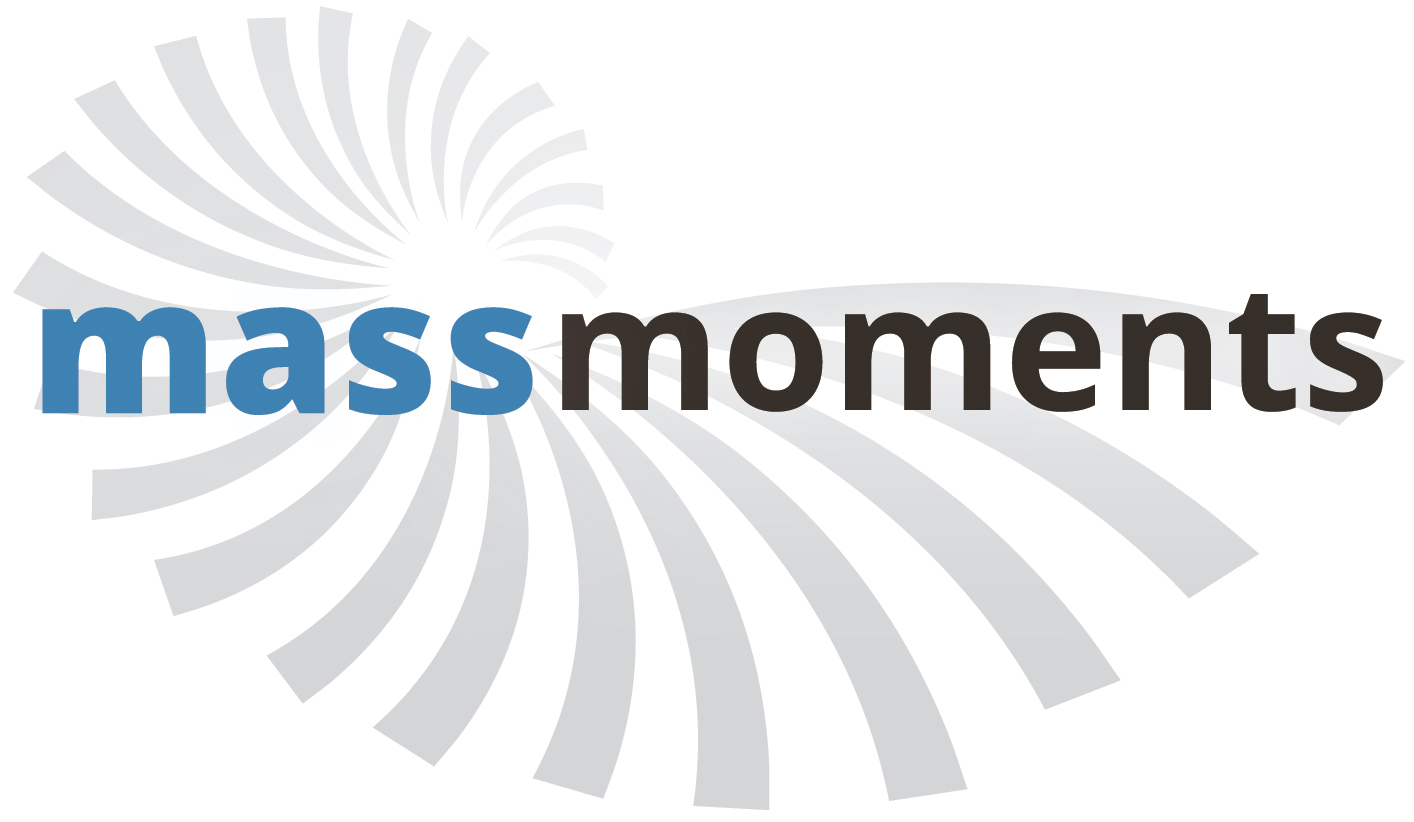
Polaroid Wins Patent Suit Against Kodak
Primary source.
JUDGE RULES FOR POLAROID IN PATENT SUIT
Polaroid Corp., and especially founder Edwin H. Land, celebrated a landmark legal victory yesterday.
A US District Court judge in Boston ruled that Eastman Kodak Co. infringed on seven Polaroid patents that are key to instant photography, Polaroid's core business. The decision closes at least one chapter in a nine-year legal battle between the two photography giants.
Judge Rya Zobel, who heard the case without a jury, still must determine whether to award damages or other remedies to Polaroid. She set no date for that decision.
One analyst predicted an award of $30 million to $40 million.
. . . Kodak entered the instant photography market in 1976, ending Polaroid's 28-year monopoly, which resulted from an impenetrable patent wall built by its lawyers and based on work by Land and his colleagues.
. . .Yesterday's decision was a personal victory for Land, who invented instant photography and spent his life building Polaroid into one of the hottest glamour companies of the 1960s and 1970s. Several of the patents involved in yesterday's decision were Land's.
Land acknowledged he was pleased and then some. "I'm thrilled," he said from his office at the Rowland Institute for Science in Cambridge, which he founded. "We worked so hard the first time around on the contents of the film and the camera and the patents on it. And we worked very hard trying to make clear to the court what the essence of every invention was."
Boston Globe , September 14, 1985.
Comment by Joe Ross | 09/13/2006
Comment by maryf | 09/14/2006
Comment by Joe Ross | 09/14/2006
You need to be logged in to add comments.
Moment Audio
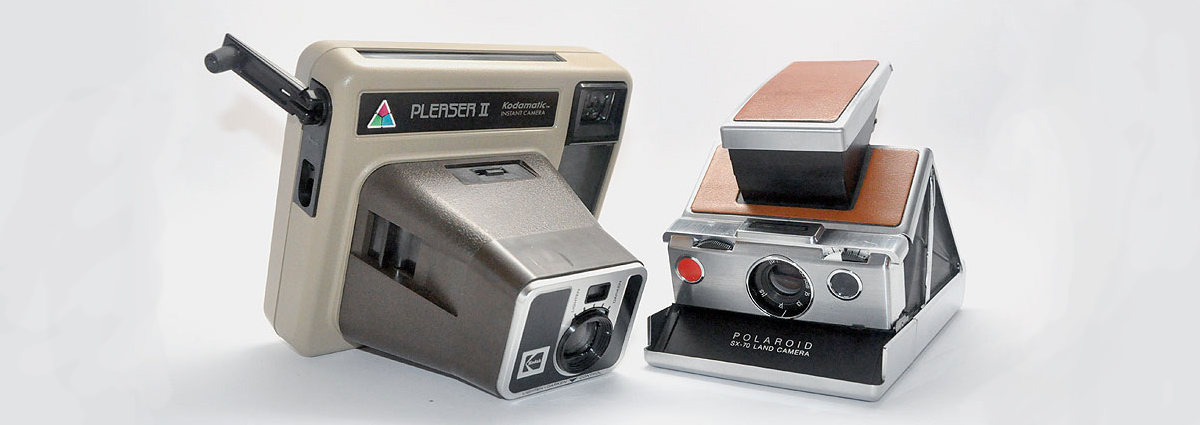
On this day in 1985, Polaroid won a huge victory in federal court. A judge ruled that Kodak had violated Polaroid's patents for instant photography. The decision ended a nine-year legal struggle between the two photography giants. The first instant camera went on sale at Jordan Marsh in downtown Boston in 1948; it was an immediate success. Edwin Land, the brilliant Harvard dropout who founded Polaroid in 1937, hired other young scientists to help develop the technology. They continued to improve the optics, chemistry, and design of the cameras. For nearly 50 years, Polaroid built and dominated a worldwide market for instant photography. But digital photography dealt the company a blow from which it could not recover. In 2001, it filed for bankruptcy.
Land received more than 500 patents, making him second only to Thomas Edison.
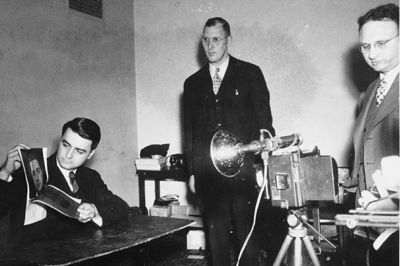
Edwin Land was born in 1909 in Bridgeport, Connecticut, the son of Jewish immigrants from the Ukraine. His parents were prosperous enough to send him to Harvard. Arriving in Cambridge in 1926, he proceeded to spend most of his time trying to create an artificial light polarizer. He knew that light traveled in waves, radiating out in all directions. When it passed through certain materials, light could be filtered — or polarized — in such a way that beams emanated in only one direction. The result was the elimination of the distracting glare of unfiltered light.
But natural materials that polarized light were rare and expensive. At the end of his freshman year, Land shocked his parents with the news that he had decided to take a leave of absence from Harvard, move to New York City, and devote himself to developing an artificial light polarizer. He worked from his basement apartment, with occasional nighttime forays into the Columbia University chemistry labs. After two years of furious experimentation, the young man applied for and received a patent on a synthetic light polarizer. It was the first of more than 500 patents he would receive, making him second only to Thomas Edison.
Polaroid's scientists soon developed a reputation for problem solving; they could move quickly from pure to applied science.
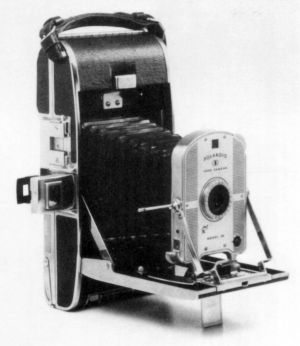
Land returned to Harvard in 1929 at the age of 20. He was determined to make his patent useful. With physics instructor George Wheelwright, he envisioned important applications for his invention: filters for auto headlights and cameras, sunglasses, glare-reducing windows. Anxious to begin commercial production, in 1932 Land left Harvard one semester shy of graduation. "The Bill Gates of his era," as the Boston Globe described him, was like Gates, a Harvard dropout who achieved success without the lauded degree. Land and Wheelwright established the Land-Wheelwright Laboratories in Cambridge.
The men secured contracts from Kodak for photo filters and from the American Optical Company for sunglasses. But in the depths of the Great Depression, Land was unable to interest Detroit in his pet project, glare-reducing polarized filters for auto headlights. Land and Wheelwright managed to keep the business afloat, and in 1937 they formally incorporated the company under the name Polaroid.
When the U.S. entered World War II, George Wheelwright joined the Navy. Edwin Land chose a different way to serve his country. He gathered the best young scientists from Harvard, M.I.T., and Smith College and made Polaroid into a place that melded scientific research and business. The biggest room in the headquarters building was the research library. Land encouraged creativity, collaboration, and a can-do attitude. Polaroid's scientists soon developed a reputation for problem solving; they could move quickly from pure to applied science. The U.S. military repeatedly turned to Polaroid to help surmount technological challenges it faced.
Within the hour, the camera, the film, and the physical chemistry became so clear to me that . . . I hurried over to the place where [a colleague] was staying, to describe to him in great detail a dry camera which would give a picture immediately after exposure."
For the military, Land and his team created glare-screening goggles, polarized gun sights, glare-proof airplane glass, and a 3-D machine for training machine gunners that was the forerunner of later arcade games. The company's workforce grew into the thousands. But the return of peace brought a decline in military contracts. Land watched as his payroll shrank to only a few hundred. The company would fail without a new product.
The inspiration came on a family vacation in California. Land took a picture of a burro for his three-year-old daughter, Jennifer. When the little girl impatiently asked, "Why can't I see it now?" she spurred her father's imagination. He went for a walk to think through the problem. Many years later he recalled, "As I walked around . . . I undertook the task of solving the puzzle [Jennifer] had set me. Within the hour, the camera, the film, and the physical chemistry became so clear to me that with a great sense of excitement I hurried over to the place where [a colleague] was staying, to describe to him in great detail a dry camera which would give a picture immediately after exposure."
It took Polaroid scientists nearly five years to make Land's vision into a reality. By the fall of 1948, the Land 95 camera, priced at $89.95, was ready for the public. On the day after Thanksgiving, a sales and demonstration crew arrived at Boston's Jordan Marsh Department Store . As astonished customers witnessed the first instant photos being made, cameras flew off the shelves. The demonstration ended early when the entire stock of cameras sold out.
As astonished customers witnessed the first instant photos being made, cameras flew off the shelves.
For the next half-century, Polaroid's instant cameras would be a cultural phenomenon and the company would set high standards as a model employer. The development of new and improved versions and a series of clever advertising campaigns ensured Polaroid's success. By 1972, it was a huge corporation, with operations all over the world. That year, Land introduced a product that he believed came close to perfection: the SX-70, a fully automatic, motorized, folding, single-lens reflex camera that produced high quality color prints in a matter of seconds.
But there were clouds on the horizon. Despite the popularity of Polaroid cameras, the stock price was falling and, equally ominous, Kodak had gained nearly 30% of the instant camera market. In 1976 Polaroid filed a patent infringement suit against its rival. Although Polaroid eventually won the lawsuit, weak management and the explosive growth of digital photography brought about what would once have been unthinkable. In 2001, one of the state's premier companies filed for Chapter 11 bankruptcy. It has since been sold twice to investors; the Polaroid brand is now owned by a Minnesota-based holding company.
"Dr. Land" — Harvard awarded him an honorary doctorate in 1957 — retired in 1983. He died in 1991.
The American Chemical Society has designated the former location of the Polaroid Corporation Laboratories, a National Chemical Landmark, which is commemorated by a plaque on the building at the corner of Main and Osborne Streets in Kendall Square.
The MIT Museum houses the Polaroid Historical Collection .
This Mass Moment occurred in the Greater Boston region of Massachusetts.
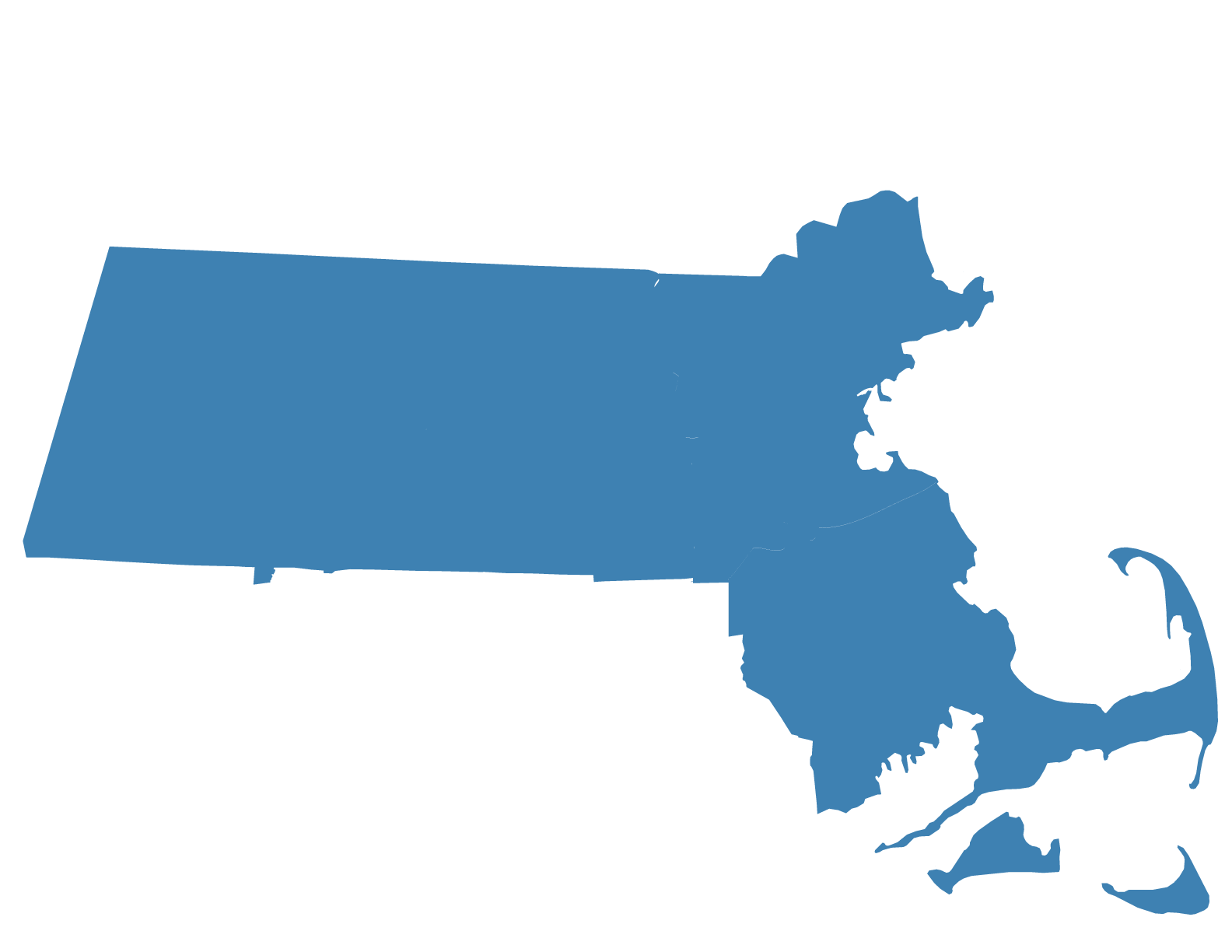
Boston Globe, October 17, 2006.
Land's Polaroid: A Company and the Man Who Invented It, by Peter C. Wensberg (Houghton Mifflin Company, 1987).
Insisting on the Impossible: The Life of Edwin Land , by Victor K. McElheny (Perseus Books, 1999).
" The Branding of Polaroid ," a corporate history written by former Polaroid consultant, Paul Giambarba.
"Biographic Memoirs: Edwin Herbert Land," by Victor K. McElheny online at the National Academies Press website
Related Moments
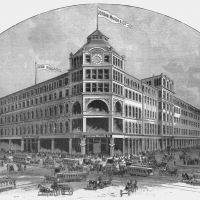
Jordan Marsh Announces New Store
On this day in 1947, Jordan, Marsh and Company announced that it was going to build "the greatest department store in the world" in downtown Boston. Almost a hundred years earlier, in 1851, Eben Jordan...
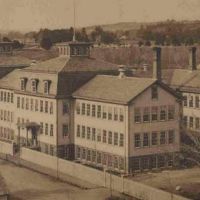
American Optical Celebrates 150th Anniversary
On this day in 1983, Southbridge celebrated the 150th anniversary of the nation's oldest optical company — the American Optical Company, or "the A.O." as it was known in the Worcester County town where it...
- Harvard Business School →
- Faculty & Research →
- January 1978 (Revised February 1983)
- HBS Case Collection
Polaroid-Kodak (B1)
- Format: Print
About The Author
Michael E. Porter
More from the author.
- August 2023
- Faculty Research
Vanderbilt: Transforming an Academic Health Care Delivery System, 2020
- 13 Jan 2023 - 14 Jan 2023
India’s Quest for Sustainable Growth in a New Global Reality:: The Need for a Region- and Sector-Driven Approach
- Vanderbilt: Transforming an Academic Health Care Delivery System, 2020 By: Michael E. Porter, Robert S. Kaplan, Mary L. Witkowski and David N. Bernstein
- India’s Quest for Sustainable Growth in a New Global Reality:: The Need for a Region- and Sector-Driven Approach By: Christian H.M. Ketels and Michael E. Porter
- Find a Lawyer
- Ask a Lawyer
- Research the Law
- Law Schools
- Laws & Regs
- Newsletters
- Justia Connect
- Pro Membership
- Basic Membership
- Justia Lawyer Directory
- Platinum Placements
- Gold Placements
- Justia Elevate
- Justia Amplify
- PPC Management
- Google Business Profile
- Social Media
- Justia Onward Blog
Polaroid Corp. v. Eastman Kodak Co., 641 F. Supp. 828 (D. Mass. 1986)
641 F. Supp. 828 (1986)
POLAROID CORPORATION v. EASTMAN KODAK COMPANY.
Civ. A. No. 76-1634-Z.
United States District Court, D. Massachusetts.
September 13, 1985.
Judgment October 11, 1986.
*829 William J. Cheeseman, Laurence S. Fordham, Foley, Hoag & Eliot, Boston, Mass., Herbert F. Schwartz, Fish & Neave, New York City, for plaintiff.
Robert S. Frank, John M. Hall, Choate, Hall & Stewart, Boston, Mass., Francis T. Carr, Kenneth E. Madesen, William J. Ungvarsky, Paul Lempel, Robert D. Fier, James Galbraith, Walther E. Hanley, Allen E. Rubenstein, Lynne Darcy, Kenyon & Kenyon, New York City, Kenyon & Kenyon, Boston, Mass., Gerald E. Battist, Eastman Kodak Co., Rochester, N.Y., for defendant.
ZOBEL, District Judge.
Polaroid Corporation, the assignee of numerous patents in the field of instant photography, brought this action against Eastman Kodak Company for infringement of twelve of its patents relating to the art/technology of both film and camera. Kodak denied infringement and alleged that all of the patents are invalid or unenforceable or both.
One of the film patents, U.S. Patent No. 3,761,269, this Court, on Kodak's motion for summary judgment, held invalid as obvious within the meaning of 35 U.S.C. § 103. The parties waived their claims of infringement and invalidity with respect to a second patent, U.S. Patent No. 3,757,657, alleged to have been infringed by certain features of Kodak's EK-4 camera. Trial proceeded with respect to the remaining ten patents [1] on the issues of liability and infringement, on one hand, and invalidity and/or unenforceability on the other. This memorandum shall constitute my findings of fact and conclusions of law as to those issues. [2]
In conventional photography, as opposed to instant photography, a picture begins as a sheet of plastic or paper coated with a thin layer of gel which has in it a suspension of microscopic crystals of silver halide. When that coating is exposed through the lens of the camera, the silver halide grains are modified to form an invisible image the latent image. Exactly how the latent image is formed is apparently still subject to debate, but it involves the transformation of the silver halide into concentrations of minute, reduced silver particles depending upon the intensity of light on various portions of the film.
To make the latent image visible, the film is placed into a developera reducing agent. The developer delivers electrons to the concentration of silver halide grains that form the latent image and further transforms them into metallic silver. Because the developer will continue to deliver electrons to the silver halide, ultimately reducing all to silver, the process must be stopped after a period of time when the latent image has become optimally visible. This is accomplished by briefly immersing the film in a dilutable acid bath. Because exposure of the film to light would wipe out the latent image, developing must be accomplished in a dark room.
Following development, the film is put into a solvent for silver halidehypo *830 which converts the remaining silver halide crystals into soluble silver salts and removes them by dissolving them. Since all of these chemicals would in time adversely affect the quality of the image, the film finally is thoroughly washed in water and dried, leaving a permanent negative image.
The negative image is formed where light converted the silver halide into metallic silver, which is seen as black. The more light reaches a particular area, the denser the concentration of silver and the darker the image in that area. The brightnesses on the negative are thus totally reversed. To produce a positive, the process just described is repeated. The negative is projected onto sensitive paper carrying a silver halide emulsion either through an enlarger or by pressing the negative directly against the positive. The positive is then processed in essentially the same manner as was the original film.
Edwin H. Land, the founder of Polaroid and the inventor of numerous patents, including several of those in suit, began work on what he came to call "one-step photography" in 1944. In 1947, he first introduced his version of the diffusion-transfer process by which the negative and positive were produced simultaneously. The film which will become the negative was exposed in the same manner as in conventional photography. The steps thereafter differed radically from those described above. The negative is brought into juxtaposition with a positive sheet within the camera and a viscous reagent contained in a sealed pod on one of the sheets is spread between them by means of two rollers. The positive and negative, which are symmetrical, are developed at the same time. After a defined period of time, the sandwich, positive and negative with reagent in-between, is pulled out of the camera and peeled apart. The camera also serves as the darkroom. Later, in the SX-70 system, the sandwich itself becomes the dark room.
One-step photography, as first marketed in December 1948, produced a sepia colored photograph. That was replaced by black and white peel-apart film in the early 1950s. At the same time that these sepia and black and white films and cameras were being developed and improved, Land and his associates addressed the problem of instant color photography.
Color photography requires three negative layers, each sensitive to a different primary colorblue, green or red. Complimentary dye layersyellow, magenta and cyan, the subtractive colors positioned between the sensitive layersabsorb the primary color to be recorded on each sensitive layer. Thus, the blue sensitive layer controls the yellow dye layer next to it, which absorbs blue light; magenta absorbs green; and cyan, red. The dye layers are therefore sometimes called minus blue, minus green, and minus red. In conventional color photography, each sensitive layer contains a "coupler" and the dye layer a "color developer" which, by a reduction-oxidation process, will join together and form a dye. After exposure, the color developer is oxidizedit gives up electrons to the sensitive layer where the latter has been catalyzed by light. The silver halide layer is reducedit gains electrons, enabling the color developer and silver halide to join. Each color uses a different coupler and the coupling process takes place within each layer. There is no transfer to different layers. Moreover, the reaction time of each coupler is different. Instant photography relies on a diffusion transfer process in which the reagents that form the negative image at the same time operate to form the positive. Coupler chemistry did not easily adapt to diffusion transfer.
At Dr. Land's direction, Howard G. Rogers, starting in 1947, began work on the problem of instant color film. The solution he evolved discarded couplers and relied instead on dye developers, a combination of preformed dye and developer, and led eventually to one of the patents in suit, U.S. Patent No. 3,245,789. By 1957, Polaroid had made a prototype of the first one-step color photograph, and in 1963 it introduced instant color to the market under the name Polacolor, a peel-apart product.
*831 Further work on both film and camera led to the introduction of the SX-70 system in 1972, described by Dr. Land as "absolute one-step photography." It is an elegant, highly sophisticated camera and film system. The photographic unit, which is ejected from the camera immediately after exposure, develops into a visible image in daylight and requires no peeling. The camera designed for the particular needs of this film unit contains a motor, gear train, and pick which, working together, operate to eject the film unit. The photographer needs to do nothing but focus the camera and expose the film to obtain a finished print.
Except for the '789 dye developer patent mentioned above and the 165/262 opacifying layer patents to Rogers, all of the patents in suit pertain to innovations incorporated into the SX-70 system.
From the early 1950s, Kodak had supplied Polaroid's needs for negative material. After Polaroid's development of the one-step color photograph, the parties, in December 1957, entered into an agreement pursuant to which Polaroid disclosed to Kodak certain of its color technology, including Rogers' concept of dye developers, and Kodak cooperated with Polaroid to develop and produce negative material adapted to this technology. Kodak then continued to supply Polaroid's requirements for negative material and the parties periodically met to discuss their research activities. About 1963, the research meetings terminated, although Polaroid continued to work on refinements and improvements in color and continued to inform Kodak of its progress from time to time. In April 1968, Polaroid advised Kodak of a radically new film, which would ultimately become the SX-70, and in October of that year, Dr. Land showed Henry C. Yutzy, Kodak's vice president of research, photographs made with the new method. The parties discussed a licensing and continuing supply arrangement, without coming to any resolution. In April 1969, Kodak notified Polaroid of its intention to terminate the 1957 agreement.
In early 1969, Kodak also launched its project PL-976an effort to put an instant product on the market by 1976. The object was to produce a high quality color print in the camera which preferably would not require peeling and to do so without the assistance of existing patents. PL-976, then optimistically redesignated PL-974 (moving back to 1974 the projected market date) investigated a variety of photographic chemistries. During 1970, groups at Kodak outside the research laboratory became more interested and the project was once again renamed and restructured. Project P-129 was begun to develop an instant color film similar to Polacolor and compatible with Polaroid cameras. P-130 was to produce an integrated systemKodak film for a Kodak camera. The former, P-129, was abandoned toward the end of 1972 after an expenditure of 94 million dollars. Although the stated reason was that Kodak had been unable to solve certain problems caused by the particular chemistry used, the cessation of work on P-129 followed shortly upon the introduction by Polaroid of its SX-70. Contemporaneous Kodak memoranda recognized that any product created by P-129 would be obsolete even if it appeared on schedule.
The P-130 effort continued with increasing intensity. Because Kodak sought to attain its objectivescamera and film simultaneously, not sequentially, the expenditures of manpower and money were enormous. Between 1,300 and 1,400 people were assigned to P-130 at the peak periodlate 1973 to mid-1975. Dr. Albert Sieg, Director of Photographic Strategic Planning, described the approach taken by Kodak. The different groups assigned to solve various discrete problems were to explore the existing technology and pursue parallel work on different applicable technologies. When no technology existed to solve a particular problem, invention was called for. That, in turn, required increased funding and increased resources. Despite these efforts, numerous problems defied solution.
*832 By the early part of 1972, Kodak had developed the "Lanyard" camera model, so called because the picture was to be ejected by use of a lanyard. It advanced the film by means of front picks. It did not contain a motor nor a gear train but did include devices to strip the pod from the photograph and to trim its edges. Although, as a consequence, the camera was relatively large, Kodak's marketing people were content with its size. Following Polaroid's SX-70 announcement in April 1972, and review by the P-130 committee of its implications, the committee found that the "P-130 program as earlier defined, was no longer desirable." The Lanyard camera was too large by comparison to that marketed by Polaroid.
Kodak also encountered numerous difficulties in its attempt to develop the film. Like Polaroid, it had to work out the imaging chemistry of integral film. By the fall of 1971 Kodak researchers had focussed on two dye release chemistries but did not achieve sufficient speed with either one of them until late 1972. By mid-April 1972, Kodak researchers had still not worked out a solution to the problem of dye stability and they had yet to solve problems associated with the mordant and the opacification layers. Although they hoped to achieve a "no-inventions" prototype by January 1973, a host of difficulties remained as late as mid-December 1972.
It is undisputed that Kodak purchased large quantities of SX-70 cameras and film in October 1972, after they became commercially available. It is also undisputed that the several groups and departments involved in P-130 were ordered to familiarize themselves with the Polaroid product and to test it. As a result, Kodak's marketing coordinators and managers commented in January 1973 that the P-130 program, as it then existed, was only "marginally acceptable." They recognized that Polaroid had set the standard Kodak would have to meet and that even a "me-too" program would require more than two and one-half years to produce a less than equal design.
Kodak did, in fact, introduce an integral system consisting of its EK-4 and EK-6 cameras and PR-10 film in April 1976. It is those products which, in several particulars, are alleged to infringe the patents in suit. Although, as Kodak correctly points out, this case involves nine [3] different patent disputes and instant photography is not the perpetual domain of Polaroid, the response of Kodak to the SX-70 system has some bearing on the judgment concerning the underlying patents. Also while it is by no means decisive on the question of infringement of any particular patent, so does the suggestion in September 1973 of Kodak's Development Committee that "[d]evelopment should not be constrained by what an individual feels is potential patent infringement."
Kodak denies each allegation of infringement and argues the invalidity of each claim asserted against it. I will deal with the specific allegations of infringement and validity in the discussion pertaining to each patent. Certain broad contentions recur, however, and are properly addressed here.
The parties are in substantial agreement on the standards for judging anticipation and obviousness under 35 U.S.C. §§ 102 and 103. They disagree in one area that bears on several of the patents in suitthe effect of Polaroid's internal work and whether it constitutes part of the prior art against which the validity of a particular patent is to be judged. Work done within Polaroid which was not published is not prior art and I have not considered it in judging the validity of any patent. Del Mar Engineering Laboratories v. United States, 524 F.2d 1178, 1182, 207 Ct.Cl. 815 (1975).
As to each patent, Polaroid relies on the presumption of validity. Kodak claims that this presumption is in nearly every instance undercut by Polaroid's failure to disclose pertinent prior art to the *833 Examiner. The parties have genuine disagreements as to what constitutes prior art, but I rule that Polaroid has fulfilled its obligation to the Patent Office where the patent in suit is in the class of patents that was cited. See, e.g., E.I. Du Pont de Nemours v. Berkley & Co., Inc., 620 F.2d 1247, 1267 (8th Cir. 1980); International Telephone & Telegraph v. Raychem Corp., 188 U.S.P.Q. 214, 219 (D.Mass.1975), aff'd, 538 F.2d 453 (1st Cir.), cert. denied, 429 U.S. 886, 97 S. Ct. 238, 50 L. Ed. 2d 167 (1976). In addition, prior art described in the specifications is expected to be considered by the Examiner. Gould v. General Photonics Corp., 534 F. Supp. 399 , 403 (N.D.Cal.1982). Patent Examiners are also presumed to be aware of patents which issued from applications they had earlier examined. Hahn & Clay v. A.O. Smith Corp., 320 F.2d 166, 172 n. 15 (5th Cir.), cert. denied, 375 U.S. 944, 84 S. Ct. 351, 11 L. Ed. 2d 274 (1963).
In support of its argument that the patents are valid, Polaroid points to the commercial success of the processor product disclosed. The SX-70 camera and film system has unquestionably been immensely successful, as has Kodak's product. The evidence presented is, however, inadequate to permit me to assign to any one patent credit for the commercial success of the whole. Accordingly, this factor has played no part in the decision.
Finally, I have for the sake of completeness proceeded to consider the issue of infringement even as to those claims found to be invalid.
Land U.S. Patent No. 3,362,821 concerns stabilization in one-step color photography. All photographic processes, as described earlier, implicate three stepsexposure (formation of the latent image), development (formation of a visible image), and stabilization (cessation of chemical reactions and preservation of the visible image). In conventional photography stabilization is accomplished by subjecting the film to different chemical solutions seriatim. One-step photography, by definition, required telescoping all of the steps, which is not to say that numerous steps did not occur sequentially within film and camera. Thus, chemicals were needed which would, when combined with the processing composition, permit development, then stop it at the optimal point and thereafter remain neutral. Solution of this problem was complicated by the fact that each type of film, sepia, black and white, and color, unexpectedly called for markedly different stabilization techniques.
Polaroid's first one-step film, introduced in 1948, produced sepia prints in a peelapart format. For stabilization, Dr. Land used metal salts and water soluble esters. In the presence of the processing composition, the metal salts reacted with the esters to reduce the pH. Because their reaction rate with the alkali of the processing composition was relatively slow, they permitted formation of the image before they broke up to produce alcohol and neutralizing acid. Finally, the reaction of the several components of this system reduced the pH to an ideal level, just above neutral. Too much acidity would cause production of sulfur which, in turn, would attack silver and ultimately destroy the photograph.
This stabilization mechanism was highly successful also because the photographer needed to do nothing but take the picture. Brown pictures were not ideal, however, and there was great pressure to produce black and white film.
Because both sepia and black and white film involved silver transfer, Dr. Land and his associates had thought that the same stabilization process would work with black and white film. They found that it did not. To obtain a black and white print, the aggregation of silver ions was changed. That produced a shield. As a consequence, the metal salt, lead acetate, could not uniformly penetrate the black and white surface and the migration of the esters was also retarded. The ultimate solution was the print coater. The photographer had to swab each positive with a solution of a polymer and acetic acid that both washed the film and gave it a protective coating. *834 This stabilizing system also required redesign of the black and white image and the support.
Color film called for still different techniques. The timing needs of color were different from those of both sepia and black and white. During the 1950s and into the early 1960s, when Polaroid and Kodak still cooperated, scientists from both camps discussed a number of proposals, including a suggestion of Kodak's Dr. Vittum to use an acid layer of commercially available sulfostearic acid. [4] None worked successfully and as the scheduled date for marketing the new color film, Polacolor, approached, Polaroid expected to offer the film with a print coater. Even that, however, presented difficulties. Because the problems inherent in stabilizing color film differ radically from those pertaining to black and white, the coaters used different materials and required different "skills" from the user. The color print had to be coated within five seconds after removal from the camera. It had to be swabbed 16-18 times and the coating was slow to dry.
The print coater was not only cumbersome and difficult to use, it also lacked elegance. During the summer of 1962, Dr. Land and his associates engaged in intensive investigation of alternative stabilizing techniques. To succeed, the stabilizing system had to meet three requirements. It had to allow the processing emulsion to retain its alkaline characteristics long enough to permit adequate image development and dye transfer. It then had to drop the pH abruptly and permanently to prevent further development and dye transfer, and third, it had to remove from the image-receiving layer the alkali metal ions introduced by the processing emulsion. The alkali metal ions, if not removed, would precipitate as salts in the image receiving layer and in time cause the image to become dull.
In September 1962, Land conceived and indeed suggested to Messrs. Yutzy and Damschroder of Kodak, the use of a nondiffusible polymeric acid and associated timing layer. Unlike the esters which first had to decompose to provide a neutralizing acid, the acid polymer would react instantly upon contact with the alkali. The acid polymer would then abruptly drop the pH in the film structure by removing alkali metal ions from the processing solution and attaching them to itself. The layer had to be thick enough to provide adequate polymeric acid to accomplish the task, and a mechanism had to be incorporated to delay the reaction until the completion of development. The idea had two additional advantages. The polymeric acid, by removing the alkali metal ions, prevents the precipitation of metal and attendant dullness of picture. It thus produces more brilliant images. Color diffusion transfer by its very nature requires the disposition of a larger volume of alkali than does sepia or black and white film. The polymeric acid layer disposes of that alkaline environment and thus enables maintenance of a good image indefinitely.
Polaroid immediately incorporated the concept of a nondiffusible polymeric acid layer into its Polacolor film which was, with that stabilization mechanism, introduced to the market in 1963. Dr. Land considered building the polymeric acid layer described above into two possible locations of the film unit: between the support and the adjacent image-receiving layer; or beyond the far part of the negative, that is, between the support associated with the negative and the innermost layer of dye developer. Two patents issued on this invention, one pertaining to the location of the acid layer near the positive, Land U.S. Patent No. 3,362,819; the other pertaining to an acid layer near the negative, Land U.S. Patent No. 3,362,821, the patent in suit. Polacolor employs the location described in the '819 patent. Polaroid alleges *835 that Kodak's PR-10 film, which admittedly contains an acid layer, places the layer in the photosensitive element thereby infringing the '821 patent.
The '821 patent discloses a layer of a nondiffusible acid-reacting reagent in the photosensitive element. It describes the preferred embodiment of the invention as a layer containing an acid-reacting polymer, and particularly, a polymer-containing free carboxyl group. The patent uses the shorthand expressiona polymeric acid layer. It includes a list of specific polymeric acids suitable to the purpose. The specifications teach that the polymeric acid layer is preferably 0.5 to 1.5 mils thick; that is, relatively thick as compared, for example, with the dye layers.
The acid layer contains acid groups attached to a polymer so as to be nondiffusible. It reduces the pH in the image-receiving element by attracting alkali ions and then trapping them by precipitating them into the acid layer. The patent accordingly describes the acid layer as "a mordant for alkali." [5] It further teaches that the action of the polymeric acid must be controlled so that it will not interfere either with the development of the negative or with the image transfer of unoxidized dye developers. In other words, the reduction of pH must be properly timed. The patent suggests three timing mechanisms. A separate spacer layer of inert polymer may be used to delay contact between the alkali ions and their trap, or an inert polymer may be mixed into the acid polymer to make the acid less accessible to the alkali ions. A third method calls for an acid layer with a relatively lower concentration of acid groups, again to prevent too rapid attraction and precipitation of alkali ions.
The patent states that the polymeric acid layer "is provided in the photosensitive element and is positioned adjacent the support, i.e., between the innermost layer of dye developer and the support." That positioning is depicted as well in Figure 1 of the patent. The specifications by reference to Figure 1 describe the photosensitive element as comprising "a support bearing, in turn, a layer containing as a nondiffusible acid-reacting reagent, a polymeric carboxylic acid ..." and the dye developer layers. The image-receiving element comprises a "support carrying an image-receiving layer."
Claim 1 is the only claim asserted against Kodak. In the context of color diffusion transfer processes, it claims the use of a layer of a nondiffusible polymeric acid containing sufficient acid groups to effect a reduction of at least two pH units in the surface of the image-receiving layer, compared with the initial pH of the processing composition, prior to the completion of the imbibition period. The acid layer is claimed to be contained in the photosensitive element and positioned between the support and the innermost negative layer.
Kodak denies infringement and contends that the patent is, in any event, invalid under 35 U.S.C. §§ 102, 103 and 112 and that it is unenforceable. It relies in its post-trial brief on two prior art references listed in the Section 282 Notice: U.S. Patent No. 2,584,030 and Kodak French Patent No. 1,293,709. [6]
The '709 patent is said to disclose the process described in claim 1 of '821 and thus to render that claim invalid under 35 U.S.C. §§ 102(a) and 102(b). French Patent No. 1,293,709 describes color diffusion transfer processes employing coupler chemistry in which the photosensitive element is exposed, an alkaline-processing solution is applied, and a diffusible colored image is transferred to an image-receiving layer. It acknowledges that in "processes involving the transfer of dye images to mordanted reception layers, small amounts *836 of alkali ..." may also be transferred and may be objectionable. One proposed solution is to wash the reception layer to remove such materials, and one method offered is "to squeegee the dye images into contact with a moist sheet containing ... an acrylic acid polymer ... to neutralize the alkali...." Alternatively, it suggests providing "a hydrophylic [sic] organic colloid layer containing the mentioned acids ... between the mordanted support and ..." reception layer, which layers are later stripped from the mordanted support.
I find that '709 does not anticipate claim 1 of '821. The acid layer in '709 is not located in the photosensitive element, but between the photosensitive layer and its support. Both Dr. Land and Kodak's expert, Dr. Trautweiler, agreed that the '709 layer does not reduce the pH of the surface of the mordanted support, the analog of the image-receiving layer of '821. More fundamentally, the acid layer of '709 is a scavenging layer designed to prevent alkali from reaching the mordanted support, not a stabilizing system designed to stop the development process and prevent subsequent chemical reactions. The experts agreed, moreover, that they knew of no commercial unit in which dyes diffuse through an acid layer, that is, one in which the acid layer is positioned as in '709. That patent does not describe the process of '821 and the process it does describe does not solve the problem addressed by '821.
Kodak asserts that '709, in any event, and U.S. Patent No. 2,584,030 disclose the technique of using an acid layer in the photosensitive element to reduce pH and that '821 therefore represents no more than the application of routine skill. Kodak's assertion is premised on a most narrow reading of the patent in suit, namely, that the purpose of the acid layer is to neutralize the processing composition and thereby to prevent stain caused by the oxidation of the developer. I do not, in view of the evidence adduced at trial, treat the invention so severely. The '821 patent describes a system of stabilization that not only lowers the pH but does so in a specified manner with a timing mechanism. Its purpose is not merely to prevent stain but also to increase the light-stability of the dyes in the image. The specifications and examples teach the use of particular acids and acid layers of particular thicknesses. They teach three different timing mechanisms, which are earlier detailed, and the means of achieving light stability through trapping positive cations in the acid layer so that they cannot go to the image layer and damage it.
For the reasons outlined earlier, I do not find in the '709 patent the teaching of the stabilization system of '821, even to one of the high level of skill characteristic of those engaged in this field. The single reference on page 52 of a 53-page document [7] to a "hydrophylic [sic] organic colloid layer containing ... acids" to remove "small amounts of alkali" from the mordanted reception layers does not teach the use of an acid layer with a timing mechanism. Nor does the peel-apart film of '709 teach the location of the acid layer "in the photosensitive element."
The second prior art reference relied on by Kodak is Land's '030 patent, issued ten years before '821. It teaches stabilization techniques useful for sepia images and describes two processes, one using heavy metal salts and the other, an acid. One of the acids specified is cellulose acetate hydrogen phthalate, which is also a preferred polymeric acid in '821. The '030 teaches the need to reduce the pH of the liquid composition to 7, 6 or lower, and while it is preferable that "the acidifying substance" be "included on or associated with the image-carrying layer ..." such is not essential and "it might, for example, be positioned between the photosensitive layer and the base carrying this photosensitive layer...." This patent, like '709, describes a peel-apart film structure. The acid layer *837 is available to the alkaline reagent directly so that neutralization occurs immediately. The amount of acid must be small enough not to interfere with silver development. During processing, the acid is slowly dissolved by the processing composition while simultaneously the pH of the processing composition is slowly lowered.
I credit the testimony of Dr. Land that this mechanism does not teach the system embodied in '821. To say, as did Dr. Trautweiler, that if one deletes the words "color" and "dye" from claim 1, one gets the process described by the '030 patent does not take sufficient account of the essential differences between the processes for sepia and color. Color diffusion transfer requires more time than the simpler silver transfer of sepia, and color requires the removal of the alkali metal ions from the environment of the image entirely. Neither these unique requirements of color, nor the mechanisms disclosed in '821 for meeting them are disclosed in '030.
The evidence is undisputed, moreover, that the art had been full of experiment for several years, but no one had perceived the particular conformation, position and qualities of the '821 polymeric acid layer for stabilizing color diffusion transfer film units until Dr. Land did in 1962. He was the first despite the fact that the parties in this case include on their staffs, without doubt, the world's preeminent experts in the field of instant photography.
Kodak further argues that the '821 patent is invalid because it does not teach how to make the claimed invention as required by 35 U.S.C. § 112. One of the requirements of claim 1 is that the polymeric acid layer contain sufficient acid groups to effect reduction in the pH of the surface of the image-receiving layer of at least 2 pH units compared with the initial pH of the processing composition. Kodak's expert, Dr. Trautweiler, calculated the drop in pH in several examples cited in '821. His computations show a substantially smaller reduction and Kodak argues therefrom that the patent does not teach how to make the claimed invention. The calculations are just thatthey are not based on experimental data. Moreover, Dr. Trautweiler did not view the system as a whole. Other components effect some reduction of pH before the acid layer begins its work. But the acid layer completes the process and does thereby cause reduction of the pH on the surface of the image-receiving layer by at least two pH units. In this fashion, the invention works precisely as claimed.
Finally, Kodak contends that the patent in suit is unenforceable because Polaroid's attorney and Dr. Land allegedly misrepresented the content of '030 to the examiner and failed to inform the Patent Office of the existence of the '709 patent. To prevail in this defense Kodak must show that Dr. Land and his attorney made misrepresentations with knowledge of their falsity or in an atmosphere of gross negligence as to their truth. It must further show that any information withheld was material. Materiality means facts known to the applicant which but for nondisclosure would have prevented the patent from issuing or would have restricted the claims. Digital Equipment Corp. v. Diamond, 653 F.2d 701, 715 (1st Cir.1981) (citing Union Carbide Corp. v. Filtrol Corp., 170 U.S. P.Q. 482 (C.D.Cal.1971), aff'd, 179 U.S.P.Q. 209 (9th Cir.1973)). The First Circuit does point out that the questions of culpability and materiality are interrelated such that an intentional scheme to defraud may require a lesser showing of materiality; a negligent misstatement, a greater one. Digital Equipment Corp. v. Diamond, 653 F.2d at 716.
The '030 patent was unquestionably cited to the examiner. Given my finding above on the relevance of its contents to the invention of the patent in suit, I find that Dr. Land and his attorney did not in any way misrepresent its significance. French Patent No. '709 was not cited at all, but I credit the testimony of the attorney, Mr. Mervis, that he was unaware of it until many years later. I find, therefore, that the '821 patent is valid against all of the defenses raised by Kodak.
*838 The issue of infringement hinges on the definition of the location of the acid layer in Kodak's PR-10 film. Specifically, the question is whether the acid layer is "in the photosensitive element." The parties do not disagree that the PR-10 acid and timing layers are positioned between a support and the photosensitive silver halide and associated dye layers. But Kodak points out first that in the manufacture of PR-10 the acid layer is coated on one support, the negative layers on another support, and that they are manufactured as separate elements and then assembled into one film unit. Because the negative and acid layers are coated on different supports, it argues, the acid layer is not positioned "in the photosensitive element." The difficulty with that argument is that claim 1 is admittedly a process, not a product claim, and in defining the process it describes the position of the acid layer in the photosensitive element precisely where it is located in PR-10, "between the support and the innermost layer containing ... dye imageforming substance." The photosensitive element is described in the specifications as including, in order, a support, a polymeric acid layer, a spacer or timing layer, and the layers containing the silver halide emulsions and dye developer. Regardless of the manner of manufacture, the sequence of layers in PR-10 is that described in the patent, and during processing, PR-10 is comprised of the same layers depicted in Figure 1 of the patent and has the same structure described in claim 1.
Conflicting definitions of "photosensitive element" in other Polaroid patents do not save PR-10 from the claim of infringement. The term clearly has various possible meanings, as is shown by Kodak's recital of other references. '821, however, provides its own clear definition. [8] A patentee is entitled to choose his own terms and to insist on them so long as he is consistent and does not contravene any single established or accepted meaning. Mooney v. Brunswick Corp., 663 F.2d 724 (7th Cir. 1981); Harrington Manufacturing Co. v. White, 475 F.2d 788, (5th Cir.), cert. denied, 414 U.S. 1040, 94 S. Ct. 542, 38 L. Ed. 2d 331 (1973).
For the reasons stated, Land U.S. Patent No. 3,362,821 is valid and infringed by Kodak's PR-10 film.
As noted earlier, Howard G. Rogers began in 1947 to explore the possibility of importing color into one-step photography. Conventional color photography relied on coupler chemistry to produce color. A color developer became oxidized, and as a result combined with a coupler compound to form a dye. Different couplers were needed to produce different colors and each had a different reaction rate, making this process unsuitable for diffusion transfer which required a synchronization of reactions that coupler chemistry simply did not permit. Rogers sought to solve that problem by his coupling dye process disclosed in U.S. Patent No. 3,087,817, a patent not directly involved in this litigation. It used preformed dyes with coupling groups attached. In that process, the oxidized color developer joined with the coupler and its attached dye and thereby controlled not the formation of dye but the transfer of the preformed dye to the positive layer. That is, when the processing composition is introduced, the color developer is oxidized where silver halide was exposed and, as described before, it then joins with the coupler. The junction of color developer and coupler forms an insoluble compound which remains in the negative layer and is ultimately discarded as the negative is peeled. Where silver halide was not exposed no oxidation-reduction and no coupling takes place; the coupler with dye attached remains *839 soluble in the processing solution and can transfer to the positive layer. The coupling dye process eliminated the problems attendant on different reaction times as the same coupling groups could be used for all dyes. But all color developer compounds used in the coupling process, paraphenylenediamines, themselves presented other difficulties. They were unstable when stored in the negative and had a tendency to desensitize the silver halide emulsion; they sometimes stained the picture; they could cause dermatitis; and they gave relatively slow reaction time and film speeds.
In the early 1950s, Mr. Rogers proposed an entirely new approach, the use of dye developers. A single molecule of such compounds contains both dye to form the image and developer to develop the latent image in exposed silver halide and to control diffusion. [9] The idea was to change the solubility and therefore mobility of the dye through oxidation by the developing silver. Mr. Rogers, in fact, hypothesized two possibilities, a "positive" dye developer which as a consequence of oxidation would produce a less soluble product, and a "negative" dye developer which would create a more mobile dye product. These concepts were ultimately embodied in two patents, respectively, U.S. Patent No. 2,983,606 and No. 3,245,789, the patent in suit. The positive dye developer process disclosed in the '606 patent is the one which Polaroid has used commercially in all of its color films since the introduction of Polacolor. Polaroid alleges that the negative dye developer process was incorporated into Kodak's PR-10 film.
The positive dye developer process works as follows. After exposure and the introduction of the processing compound, an auxiliary developer, which may be included in the processing compound or built into the negative layer, will in the exposed portions of silver halide, give its electrons to the silver halide. It, in turn, takes electrons from the dye developer, which thereby becomes oxidized. Oxidation precipitates the dye, thereby fixing it in the negative layer. Where silver halide was not exposed, the dye developer is not oxidized; the dye is not precipitated, and the dye therefore is able to transfer to the positive layer to form the colored image. In both the developed and undeveloped portions, the silver halide stays in the negative. Where the scene is light, the dye is held back in the negative by its precipitation there, while in the darker portions of the picture where silver halide remains undeveloped, and the dye developer unoxidized, the dye is free to move to the positive, the image-receiving layer.
As described in Rogers U.S. Patent No. 3,245,789, issued to Polaroid Corporation on April 12, 1966, on Application Serial No. 107,889, filed on May 5, 1961, in the negative dye developer process the dye is transferred to the positive layer in the exposedthe developedregion of silver halide. In general terms, the dye developer, which has relatively low mobility to begin with, is, as is true for the positive dye developer process, oxidized. In the negative dye developer process, however, the dye developer splits off a dye molecule as a result of oxidation. This molecule then has a lower molecular weight and greater solubility, so it becomes more mobile. It is then able to transfer to the positive layer. Where silver halide is not exposed, the dye developer is not oxidized and not split. Being relatively immobile, the unoxidized dye developer remains in the negative.
Specifically, the patent discloses a color diffusion transfer process for forming color photographs or transparencies using compounds referred to as "negative transferring developing agents." If colored, these compounds are described as being dye developers in the reduced state, "i.e., *840 they are compounds which are both dye and a silver halide developing agent." They are characterized as being "relatively nontransferable to the image-receiving layer" but they form a substantially more mobile, diffusible oxidation product. That is, the colored oxidation product is more diffusible than the unoxidized negative transferring developing agent.
The patent suggests that the photosensitive element of the film unit, the negative, contains in the silver halide emulsion a layer of the dye developer. [10] When, after exposure, the liquid processing composition is introduced, it permeates the emulsion to provide a solution of dye developer. Then, as the exposed silver halide is developed, the oxidation-reduction reactions previously described and the attendant transfers of dye molecules take place.
Polaroid charges infringement of claims 5 through 9. Claims 6 through 9 are dependent on claim 5.
Claim 5 describes the process outlined above. Claim 6 adds the requirement that the mobile oxidation product be a dye that absorbs light in the same region of the spectrum in which its associated silver halide emulsion is sensitive. Claim 7 provides for positioning the dye developer layer between the silver halide emulsion and the film unit support. Claim 8 claims the addition of an auxiliary developing agent, which is colorless. Claim 9 adds the requirement that development be effected in the presence of an antifoggant. [11]
Kodak challenges the validity of the patent and denies infringement. It asserts, first, that the process taught in the patent and claimed in claim 5 does not in fact work, as required by 35 U.S.C. §§ 101 and 112. Second, it contends that the process is anticipated by the prior art and that it is, in view of the prior art, obvious. Resolution of these contentions depends on the date of invention and the scope and content of the prior art applicable in light of that invention date. Finally, Kodak argues that PR-10 practices the prior art and not the teaching of the patent in suit. Therefore, either the patent in suit is invalid in view of the prior art or, if valid, it is not infringed.
Section 101 provides that "whoever invents ... any new and useful process ... may obtain a patent therefor." Section 112 requires that the specification contain "a written description of the invention, and of the manner and process of making and using it, in such full, clear, concise, and exact terms as to enable any person skilled in the art ... to make and use the same...."
Kodak asserts first that the '789 invention is useless because, as described, it will produce at best a poor image. This is so, it says, because the negative dye developer must be mobile even in the unoxidized state to serve as the developing agent for the silver halide. That is, unless the dye developer molecules are mobile, they cannot move into contact with the silver halide. Kodak asserts that if they are mobile, the developer molecules will transfer to the positive layer unoxidized and thus cause poor image discrimination. Second, Kodak argues that the patent, in fact, discloses only one negative dye developer compound, bis-sulfonyl hydrazide, and that this compound does not work even in a peel apart format which mechanically stops any further diffusion transfer. A fortiori, it does not work with integral film.
The argument does not accord with the appropriate legal standard and it misconceives the disclosure of the patent. A patent is invalid under § 101 if the "invention is `incapable of achieving any of the aims of the patent under any conditions.'" E.I. DuPont de Nemours & Co. v. Berkley & *841 Co., 620 F.2d 1247, 1258 n. 10 (8th Cir. 1980). The process described in this patent does occur precisely as planned. Experiments by both parties demonstrated that the negative dye developer molecule split when oxidized and thereby produced a mobile dye which transferred to form an image that corresponded to developed areas in the negative. Although the evidence showed that the images obtained were poor, because more dye developer transferred than is desirable, I credit the testimony of Mr. Rogers that the solution, to add a larger ballast, was an expedient well known in the art. Indeed, Dr. Lee J. Fleckenstein, a senior research associate in the Color Instant Laboratory Division of Kodak, testified at length about the experiments he conducted, beginning in 1958, with various compounds and ballasting groups. I am persuaded therefore that one of ordinary skill in this field "would be able to understand the patent disclosure and, from that disclosure, using the skill of the art, could build an operative system." Decca Ltd. v. United States, 544 F.2d 1070, 1077, 210 Ct.Cl. 546 (1976), cert. denied, 454 U.S. 819, 102 S. Ct. 99, 70 L. Ed. 2d 89 (1981). Accordingly, the patent is not invalid under either § 101 or 112.
The remaining issues of invalidity are bound up with the issue of infringement. They all require determination of the date of the invention of '789 and the manner in which the processes described in the cited patents and patent applications and those of PR-10 and '789 work.
The background of the inventions disclosed in the '606 positive dye developer and '789 negative dye developer patent is outlined above. Mr. Rogers conceived of the idea of both positive and negative dye developers at some time during the early 1950s. He thereafter conducted experiments with positive dye developers and succeeded in obtaining image transfer by 1955. He did little, if any, work with negative dye developers because they were relatively slow and required the use of reversal emulsions. Mr. Rogers had, however, observed the effects of negative dye developers and he recalled that the images were poor and transient.
In 1955, Polaroid very broadly disclosed both positive and negative dye developers in the form of an amendment, claim 28, to a pending patent application, Serial No. 415,073. The claim was rejected by the Examiner and Polaroid eventually cancelled it without prejudice. Polaroid did not by this action concede invalidity of that claim.
In 1957 Polaroid disclosed both positive and negative dye developer processes to Kodak pursuant to the mutual disclosure agreement made in December, 1957. That document states that "Polaroid has examined a large number of processes for obtaining transfer images in color," and that except for a few described in the literature, these processes are described in patents and patent applications appended to the document. The descriptions refer to particular chemicals and the manner in which they react; the use of reversal emulsions, antifoggants and auxiliary developers; and a variety of arrangements of the several layers of a film unit. The document also asserts that "[N]egative transfer images may be obtained by forming a mobile dye as a result of development of the latent image...." It specifically discloses the use of "a sulfonyl hydrazide of one or two molecules of a dye," the class of compounds used in Example 1 of the patent.
The application for the '789 patent was filed on May 5, 1961.
Polaroid claims an invention date at least as early as 1953, but, in any event, no later than December 1957. To sustain either date, it must prove both that by that date Mr. Rogers had conceived of the negative dye developer and that he had reduced it to practice. That is, Polaroid must show not only that Mr. Rogers formulated the process in his mind, but also that the process had been successfully performed. To show reduction to practice it must show that "the series of steps constituting the process ... [have been] carried out in such a manner as to demonstrate the practicability of the process." Bell Telephone Laboratories v. Hughes Aircraft Co., 422 F.Supp. *842 372, 380 (D.C.Del.1976) (quoting 1 Rivise and Caesar, Interference Law and Practice § 131 (1980)), aff'd, 564 F.2d 654 (3d Cir.1977), cert. denied, 435 U.S. 924, 98 S. Ct. 1489, 55 L. Ed. 2d 518 (1978).
Despite the disclosures in the 1955 patent application and the 1957 document to Kodak and despite the fact that the latter refers to the compounds ultimately specified in the patent, Polaroid adduced no evidence of any documented experiments that demonstrated the efficacy of negative dye developers until the experiments conducted in November 1960. Mr. Rogers' testimony concerning his observations during the 1950s was tentative and constitutes tenuous evidence of reduction to practice at best. Accordingly, I find that '789 is entitled to an invention date of November 1960.
To show both invalidity and noninfringement, Kodak relies on the splittable coupler process represented by its British Patent No. 840,731 granted on July 6, 1960 and three references based on inventions of K.E. Whitmore and P.M. Mader of Kodak. [12] The last three are also directed to the splittable coupler process; but they disclose in addition a "deamination" process.
In the splittable coupler process of the British patent a mobile color developing agent develops the exposed silver halide and becomes oxidized. It then moves to a dye release compound composed of a preformed dye to which is attached a conventional color coupler (para-phenylenediamine) and ballast group. The oxidized developer displaces the dye molecule which is thereby split off. The dye thus becomes mobile and is able to transfer to the image receiver. It is a process that, all parties agree, takes place in two steps and is relatively slow.
The deamination process of Whitmore-Mader also operates in two steps. It uses black and white, not color developer. However, the initial reaction is similar to that of the splittable coupler process. The developer reacts with exposed silver halide and becomes oxidized. It too moves to an immobile dye group but instead of simply displacing the dye molecule it first oxidizes the dye compound, thereby being itself reduced to its original state. The oxidized dye group, which is called a "quinoneimine," undergoes another reaction. As the Australian specification puts it, "subsequent treatment with, for example, strong alkali causes deamination to take place and the splitting off of ..." a diffusible dye for transfer to the reception layer. The residue is still ballasted and therefore immobile; it remains behind. Because the split dye segment contains an "amino" group, the process is called "deamination."
In the PR-10 process, according to Kodak, black and white developer is oxidized by exposed silver halide. The oxidized developer moves to the adjacent layer of a ballasted immobile dye release compound, sulfonamidonaphthal, oxidizes it and becomes itself again reduced. The oxidized dye release compound, a quinoneimide, undergoes hydrolysis, resulting in its being cleaved into a mobile, diffusible dye and an immobile ballasted group. Because the split dye contains an amide group, Kodak calls the process "deamidation." Kodak asserts that this is the process described in the prior art and that it is a process different in kind from that described in '789; but if it were deemed to infringe '789, then '789 is both anticipated by and obvious in view of that prior art.
Kodak's first argument, that its PR-10 process is different from and does not infringe the process disclosed in '789, has several elements. It asserts that in the '789 process, the dye containing compound, the dye developer, is mobile and moves to the silver halide, whereas the corresponding compound of PR-10 does not. It further argues that in '789 the dye compound develops silver halide; in PR-10 it does not. In '789 oxidation of the dye compound causes a diffusible dye molecule to be split off; in PR-10 oxidation forms a *843 new immobile compound with dye still attached. The dye splits off only upon the next reaction, hydrolysis. In '789 the oxidation reaction is irreversible; in PR-10 the developer compound is oxidized by the silver halide but then returns to a reduced state after oxidizing the dye compound.
Kodak's analysis of the '789 process is premised on a strained and narrow reading of the patent and it hinges on the terminology used in describing these two processes. If the terms are changed, the analysis fails. First, claim 5 of the patent does not require the dye containing compound and the developing agent to be one and the same. Therefore, it does not require that the dye-containing compound be mobile so as to contact the silver halide. See infra note 9.
Claim 5 does not call for development by the negative dye developer; rather it states that silver halide is developed " in the presence of a negative dye developer." (emphasis added). I credit the testimony of Mr. Rogers that the auxiliary developer is the agent that contacts and develops silver halide. It moves back and forth between the layers of dye developer and silver halide, oxidizing the former and reducing the latter. The fact that claim 8 of the '789 patent specifically calls for the use of an auxiliary developer does not mean that claim 5 is not broad enough to include its use. See Application of Smythe, 480 F.2d 1376, 1381-82 (C.C.P.A.1973); United States v. Adams, 383 U.S. 39 , 48-49, 86 S. Ct. 708, 712-13, 15 L. Ed. 2d 572 (1966). Thus the patent does not require either explicitly or implicitly, that the dye developer be mobile before oxidation. [13] Functionally, therefore, the negative dye developer of '789 corresponds to the dye release compound of PR-10, not to the developer or electron transfer agent of the latter.
Second, Kodak's argued distinction between the oxidation processes is as well more apparent than real. The oxidation and cleaving reactions of PR-10 and '789 occur in a similar manner and with one treatment. The parties agree that oxidation of the negative dye developer of '789 results in splitting off a diffusible dye molecule. The reaction takes place in the alkaline processing composition and it is without question a one-step reaction. '789 does not describe a separate alkali step, but the alkali attack is an important part of the reaction.
The oxidation and splitting reactions in PR-10 also take place in the alkaline solution and I find that they occur essentially simultaneously. That is, when oxidized, the dye compound cleaves into dye and immobile by-product virtually instantaneously. I credit the testimony of Mr. Rogers that the reaction mechanisms '789 and PR-10 are the same. Although Kodak describes the PR-10 process in terms of successive oxidation and hydrolysis reactions, those, in fact, occur at the same time; in Mr. Rogers' words, the reactions happen "in one fell swoop."
Finally, there is no difference between the two processes in the manner in which the developer (the electron transfer agentthe black and white developer of Kodak and the auxiliary developing agent of Polaroid) functions. In both, the developer is alternately oxidized by the exposed silver halide and reduced by the dye containing compound.
Kodak unquestionably spent considerable time and effort to achieve a dye release process and I do not doubt the testimony of Dr. Fleckenstein concerning his experiments in 1969 with sulfonamidophenols and his observation of their reactions. The sulfonamidophenols are in reality, however, another species of negative dye developer. PR-10 in fact employs sulfonamidonaphthols but the parties agree that they are simply a stronger developer. They do not *844 differ in reaction from the phenols. I find that those compounds follow the same reaction path as do the compounds of the '789 patent.
Kodak additionally argues, however, that if PR-10 and '789 are construed to involve the same process, then the process disclosed in '789 was anticipated by the prior art and therefore the patent is invalid. I find that both processes are fundamentally different from those described in the prior art. The Whitmore-Mader proposal requires after oxidation of the dye compound "subsequent treatment with ... strong alkali" which causes deamination and splitting off of the dye. In contrast, '789 and PR-10 are one-step processes. The Whitmore-Mader process is, moreover, of questionable utility. The dye group specified is a para-phenylenediamine compound and therefore suffers all the disadvantages attendant on the use of that chemical. Mr. Rogers testified that the process has no commercial value for the additional reason that the compounds specified could give rise to extraneous competing reactions that would result in less mobile dyes and a reduced yield of diffusible dye. [14] Kodak did not, in fact, pursue the deamination proposal in the succeeding continuation-in-part application which resulted in the grant of a patent. Whitmore-Mader does not anticipate '789 nor are the teachings of '789 obvious in view of Whitmore-Mader.
The PR-10 process infringes every element of the claims of the '789 patent that Polaroid has asserted. It is a diffusion transfer process in which exposed silver halide is developed "in the presence of" a sulfonamidonaphthol dye releaser which is a colored silver halide developing agent. In PR-10, the dye releaser or developing agent is oxidized as a function of development and forms an oxidation product, the dye, which is more mobile in the alkaline solution than was the dye releaser, and which transfers by diffusion to the imagereceiving layer. It thus infringes claim 5.
PR-10 also fits the added elements of claims 6 through 9. It employs the relationship between dye color and silver halide sensitivity specified in claim 6. The dye releaser of PR-10 is positioned in the photosensitive element in a layer between the silver halide and the support, as required by claim 7. The electron transfer agent of PR-10 is the colorless "additional silver halide developing agent" of claim 8 and development is effected in the presence of an antifoggant as required by claim 9.
Because '789 does not practice the teaching of Whitmore-Mader, it is neither anticipated by nor obvious in view of those prior art proposals. Because PR-10 does practice the teaching of '789 it infringes the asserted claims of that patent.
The development of a photograph must occur in a darkroom because exposure of the latent image to light will destroy it. The conventional darkroom has no place in instant photography, however, so Polaroid evolved several means of shielding the negative from light during development. The camera itself served as darkroom in some models; the film unit did in others. The latter solution typically consisted of light-tight external layers, one of which was coated with the image-receiving layer, while the other was designed to be peeled away after development to enable viewing of the picture. Absolute instant photography as envisioned by Dr. Land required a darkroom mechanism by which the film unit would remain intact before, during and after exposure and would not *845 be physically altered after processing. It also required a mechanism whereby development could take place outside the camera and in daylight. The solution was an internal opacifying system, one manifestation of which was used in the SX-70 system.
The basic SX-70 film structure is disclosed in U.S. Patent No. 3,415,644 issued to Dr. Land. It consists of a transparent support on which are coated the neutralizing and image-receiving layers and an opaque support on which are coated the negative layers. The two supports are joined at their edges and the processing composition, which contains an opacifying agent, is spread between them. The darkroom is thus formed by the opaque support and the opacifying agent. Two fundamental problems inhere, however, in that arrangement. First, because the film is exposed through the same side through which the image is ultimately viewed, a means for reversing the negative image must be incorporated. Second, the opacifying agents specified in the patent, titanium dioxide, a white substance, and carbon black, turned out in practice to be unsatisfactory singly and in combination. Titanium dioxide did not provide adequate opacification; carbon black, even in combination with titanium dioxide, provided an unsatisfactory grey background for viewing the picture. The first problem was solved in the SX-70 system by incorporating a mirror into the camera, the second, by departing from the teaching of the patent and synthesizing an opacifying agent which temporarily bars light and is then "decolorized."
While reviewing his own work on the SX-70, Howard Rogers, on New Year's Day, 1968, thought of an alternative to its film structure. His idea was to coat both the positive and negative elements on the same transparent support but to place between the image-receiving and photosensitive layers separate white pigment and carbon black layers. The white layer was the background for viewing and the white and black layers in combination, one of the walls of the dark room. To form the other wall of the darkroom, Mr. Rogers included carbon black in the processing composition. The processing composition was spread not between the positive and negative layers but between a second transparent support and the photosensitive layers.
This structure permits exposure through the separate transparent sheet and viewing through the support coated with the laminate. The arrangement results in a right-reading image and thus eliminates the need for any reversal mechanism. The positioning of the pod and processing composition permits the use of carbon black as the opacifying agent and eliminates the need for an expensive decolorizing compound. Mr. Rogers points out that his process is a much simpler opacification system than that employed in SX-70. He suggests two additional advantages. First, spreading the processing goo on the outer side of the negative layers means that the dyes do not have to travel through it; the structure therefore better tolerates bubbles in the processing composition. Second, using a preformed white layer permits viewing against the white background of the image as it forms. Mr. Rogers's structure represents a neat solution to the competing requirements of a darkroom for processing and at least one transparent support for exposure. It was not used in the SX-70 because by the end of 1967 the work on the SX-70 was substantially completed and a considerable investment had been made in production machinery.
Mr. Rogers's discovery is disclosed in U.S. Patent Nos. 3,594,165 and 3,689,262, both of which issued on September 5, 1972 and which the parties have treated as substantially identical. '262 is a continuation-in-part of '165. The specifications call for coating on one transparent support both the image-receiving and photosensitive layers. The sandwich is completed with a "transparent sheet element superposed coextensive the contact surface of the laminate" and affixed along the edges to form an integral structure. The patents further disclose that the laminate contains between the image-receiving and photosensitive layers "a processing composition permeable opaque layer." That opaque layer is preferably *846 two discrete layers, one containing titanium dioxide for viewing the image against a white background and one containing an opacifying agent such as carbon black for absorbing light.
The pod is located so that the processing composition is spread "on the surface of the laminate distal the transparent support," that is, between the laminate and the separate transparent sheet. The processing composition contains, in addition to the chemicals necessary to accomplish development and stabilization, an opacifying agent which, again, may be carbon black. The patents specify that exposure is made through the separate sheet that, in conjunction with the laminate containing the separate opaque layers, forms a light-tight envelope in which the development process can occur. After exposure, the processing composition spreads and penetrates through the negative layers to initiate the dye diffusion process. The dye transfer image may then be viewed as it is being formed through the transparent support and against the white layer.
The patents suggest the inclusion of a polymeric acid layer "positioned intermediate the transparent support layer and next adjacent essential layer." Alternatively, the "polymeric neutralizing layer" may be "carried by the [separate] transparent sheet ... next adjacent to the photosensitive laminate." In such a structure the acid layer may be insulated from "deleterious interaction with the remainder of the photographic system during storage, exposure and initial processing" by a timing layer.
Polaroid has asserted claims 3, 5 and 6 of each patent against Kodak. Each of these claims incorporates by reference claim 1 of the respective patents. Claim 1 describes a composite diffusion transfer color process film unit comprised of three parts. The first, subpart (a) in the '165 patent, calls for a laminate that contains a transparent support on which are coated, in order, a dye image-receiving layer, a processing composition permeable opaque layer, a silver halide layer, and dye image-forming layers. The second, part (b), describes a second transparent support of a size equal to the first and opposite the laminate. The third, part (c), calls for a pod containing processing composition and an opacifying agent positioned so that its contents are spread between the laminate and the second transparent support.
Claim 3 adds that the opacifying agent in the processing composition is present in sufficient quantity and the opaque layer of subpart (a) "is effective to prevent exposure" of the silver halide layers in the presence of radiation actinic to development. Claim 5 provides that the opaque layer "is actinic radiation reflective." Claim 6 specifies that it is comprised of titanium dioxide in a polymeric binder.
Kodak claims that every element of the 165/262 film structure is old. In particular, it alleges that U.S. Patent No. 3,415,645, an earlier Polaroid patent, describes most of the features of the patent in suit. Those features of 165/262 not described in '645the concepts of incorporating an opacifying agent in the processing composition and of using separate black to white strataare, it asserts, both taught in the prior art. Kodak also argues that the 165/262 patents are invalid under 35 U.S.C. § 112 for failing to disclose the best mode known to Mr. Rogers for preparing the layers of the film unit. Finally, Kodak denies that its PR-10 film infringes these Polaroid patents.
The earlier '645 patent, which was before the Patent Examiner during the prosecution of the patents in suit, describes a film unit that has one opaque layer which serves both as light barrier and white background for viewing, and an opaque flap which is superimposed on the negative layers after exposure. The pod is located so that the processing composition is spread between the positive and negative layers.
Kodak points to identical drawings depicting the arrangement of layers of the '645 and 165/262 patents, respectively, and argues therefrom that before processing the film units are identical in arrangement and functioning. For example, both *847 are exposed and viewed from opposite sides and both permit viewing of the image as it develops. Neither requires peeling to view the picture and both are described in their respective patents as "integral." According to Kodak, then, the only difference between them is the manner in which the "delayed" opaque layer is constructed after exposure. The '645 patent uses an opaque flap; the 165/262 patents use carbon black in the processing composition. Since the latter mechanism is well known in the prior art, Kodak argues that this modification of '645 does not result in patentable invention.
The difficulty with Kodak's argument is that the evidence does not support the premise of identity between the '645 and 165/262 patents, even before processing. Dr. Trautweiler, Kodak's expert, testified and I so find that despite the similarities of the drawings, '645 does not disclose the photosensitive laminate of 165/262. As Mr. Rogers explained, although the corresponding layers are similarly arranged, they do not adhere to each other in the same way. In addition, the '645 patent specifies a single opaque layer to act as both light barrier and white background for the final picture. I find that the specifications of 165/262 and claims 3, 5 and 6 of those patents, read together, clearly provide for separate, preformed black and white layers.
The use of separate black and white strata constitutes a significant difference. Combining black and white into one layer creates optical problems because too much white provides inadequate opacification and causes the light to be attenuated to the negative, resulting in fogging. Adding sufficient black to prevent damage to the negative is likely to cause the picture to lose white highlights and look muddy. In contrast, the 165/262 patents teach that separating the black and white layers provides opacification without compromising the clarity of the picture. Placing the black layer behind the white minimizes fogging. None of the prior art cited, including, of course, the '645 patent, refers to adjacent preformed black and white layers, one of which has an absorptive and the other a reflective background.
Kodak concedes that 165/262 are different from '645 during and after processing. The difference between 165/262 and '645 before processing is greater, however, than the mere substitution of carbon black for the opaque flap. Unquestionably, the addition of carbon black to the processing composition was known even as a means of opacification. But the issue is whether in view of the cited prior art, the similarities between the subject matter of 165/262 and the prior art are such that the subject matter of 165/262 as a whole would have been obvious. Thomas & Betts Corp. v. Litton Systems, Inc., 720 F.2d 1572, 1579 (Fed.Cir.1983); Kimberly-Clark Corp. v. Johnson & Johnson, 745 F.2d 1437 (Fed. Cir.1984). I find that they were not.
The use of opacifying agents in the processing composition is taught in three patents relied on by Kodak: U.S. Patent Nos. 3,053,659 and 2,607,685 to Land; and U.S. Patent No. 3,309,201 to Friedman. All relate to peel-apart film units. None disclose the other relevant and significant features of the 165/262 film unit.
The '685 patent is cited as an early example of the concept of distributing an opacifying agent from a rupturable pod to create a light shield for out-of-camera processing of the film unit. The patent does not, as Kodak concedes, teach the inclusion of the opacifying agent in the processing composition. Indeed the film unit of that patent has three pods, one each for developer, white pigment and black dye. I credit the testimony of Mr. Rogers that this multiple pod arrangement is wholly unsuitable to integral films.
Further, the film units of the '659 patent are primarily for x-ray images. The patent clearly teaches the technique of providing a delayed opaque layer by superimposing an opaque cover sheet over the exposed surface or including lamp black, also known as carbon black, in the processing goo. But the film units depicted in the patent are not arranged and do not function in the manner *848 of the 165/262 film units. With none can the forming of the image be viewed. More specifically, the films of Figures 1-5 in the '659 patent do not have the photosensitive laminate of 165/262 nor the opaque layers permeable to the processing composition. Figure 10 represents a transparency that may be viewed only after both the top and bottom opaque layers have been stripped off. Contrary to Kodak's contention, the '659 patent does not teach the functional equivalent of an opaque flap and opaque goo. It uses an opaque envelope for processing the transparencies, not opaque flaps. Moreover, if opaque goo were substituted, the unit would be nonfunctional. A transparency by definition cannot be shielded by a permanent opaque layer.
The Friedman '201 patent, where the use of an opacifying agent in the processing composition is also taught, relates to film units for making 35 mm transparencies. Its disclosure of opaque processing composition between the positive and negative layers does not suggest the 165/262 film unit.
Finally, it is undisputed that Kodak in October 1969 [15] applied for a United States patent on a film unit identical to that of the 165/262 patent. The application, which was approved by Kodak management, was based on an "Invention Conception" by Harold E. Cole, a patent attorney at Kodak. Mr. Cole had extensive knowledge of the prior art and had spent considerable time studying Polaroid patents to find a "non-infringing way" to make an instant film. He distinguished this film structure over the prior art including, in particular, the Land '645 patent and pointed to precisely the same advantages over the prior art on which Mr. Rogers now relies. Kodak learned in early 1970 of Mr. Rogers's applications which had been filed in 1968. Kodak management consulted outside patent counsel and engaged in considerable effort to obtain a United States patent, filing altogether three applications on the same film structure. The '165 patent issued in July 1971; Kodak finally, and on the advice of outside patent counsel, abandoned its United States patent application in December 1971.
Although Kodak's position at the time of its own application concerning the patentability of the 165/262 film structure is not decisive on that issue, it is some evidence that claims 3, 5 and 6 of the Rogers patents are valid against the prior art.
Finally, Kodak contends that the 165/262 patents are invalid under 35 U.S.C. § 112 because they do not disclose the best mode known to Mr. Rogers of preparing the photosensitive layers. The statute requires that the patent set forth the "best mode contemplated by the inventor of carrying out his invention." The arrangement of the layers is important in controlling the diffusion of the dye developers. Because the dye developers are mobile in the processing composition, the laminate must be constructed in such a manner that the mobile dye developer remains in the area of its associated exposed silver halide. The developer associated with unexposed silver halide, however, must be able to diffuse to the image receiver. Lack of control over the dye developer results in a defective color image. One solution lies in the addition of interlayers which slow the progress of the dye developers or barrier layers which temporarily halt it. It is the alleged failure to specify the use of barrier layers and the precise composition of the barrier layers appropriate to the laminate disclosed that Kodak argues runs afoul of section 112.
I credit Mr. Rogers' testimony that he thought interlayers sufficient and that he considered gelatin to be the preferred interlayer material for this film unit. That is indeed what the patents recite. I further find that gelatin will produce satisfactory, albeit not perfect, color separation because the use of auxiliary developer, also specified *849 in the patent, will precipitate the nonreacted dye developer in its original layer.
In an ongoing effort to improve interlayers, Polaroid experimented with a number of latex materials, including one known as Rhoplex AC-61. Polaroid used it in the commercially available form and also with the addition of thickeners. Mr. Rogers did not consider it the best interlayer material. Rather, in experimenting with it and other materials he found that what worked in the laboratory turned out not to be usable with the production machines. Accordingly, I find that Polaroid has not violated section 112 nor has it deliberately omitted known information concerning the effect of thickeners which would render the patent unenforceable.
Kodak does not deny that the PR-10 film unit contains each element of the asserted claims. It denies infringement, however, on the ground that each of the PR-10 features is found in the prior art. Kodak cannot avoid infringement by suggesting that individual components of PR-10 are disclosed in various prior art references. Morrill v. Automatic Industries, Inc., 93 F. Supp. 697, 708 (W.D.Mo.1950). It is the unique layer and support arrangement described in the asserted claims which are included in the PR-10 and this arrangement is not described in the prior art. I find that the PR-10 film infringes claims 3, 5 and 6 of the 165/262 patents.
Mordants are chemicals that fix dyes in a substance by combining with the dye to form an insoluble compound. The dyes used in instant photographic processes are, by definition, soluble and therefore tend to wander both toward and away from the image-receiver. Accordingly, a mordant must be included in the image-receiving layer to form and retain an image. U.S. Patent No. 3,770,439 relates to a class of polymeric mordants which include in their structure specified repeating units [16] that are described in the patent and denoted as "Formula A."
In the fields of photography and textile printing, mordants have been used for a long time to bind dyes; and numerous mordanting compounds have been produced commercially and disclosed in the literature and in patents.
Researchers at both Polaroid and Kodak sought to adapt some of these known compounds to integral film. They found however that diffusion transfer in an integral film unit imposed additional and far more rigorous requirements on the mordant than did the "matrix printing" process. In the latter, no diffusion through several layers takes place. Color prints are made from three preformed printing matrices that are dipped in different color dyes and one after another pressed directly against a receiving sheet that contains a mordant. The receiving sheet is immediately exposed to air to dry.
By contrast in any instant process the photosensitive and image-receiving layers are contained within the same sandwich, and all three dyes travel at the same time in an alkaline environment through several layers before reaching the image-receiver. Although peel-apart film is separated and the image-receiving layer exposed to air, such is not the case with integral film. In an integral film unit even after the dyes reach the image-receiver they are subjected to ongoing chemical reactions. In addition, the final image remains in a wet environment as the film unit slowly dries over a period of weeks following exposure and development. Thus to be useful for an integral film unit, a mordant had to work with three dyes at once; it had to be strong enough to attract the dyes to the image-receiver and to prevent their being pulled out *850 by competing chemical reactions; and it had to hold the image stable in a wet environment.
Polaroid encountered numerous difficulties in meeting these mordanting requirements during the development of the SX-70 film, and in the summer of 1970 Dr. Land assigned Lloyd D. Taylor, the Laboratory Manager of Polymer Research, to find a mordant that would hold the dyes in an integral film unit. Dr. Taylor directed his staff to evaluate several compounds, including polymers of certain vinyl benzyl quaternary ammonium salts. He had worked with such compounds in the early 60's. Although he had found some of them promising, he put them aside as they were not then commercially available. Under Dr. Taylor's direction, his staff tested a number of polymers and obtained far better results with compounds that contained the vinyl benzyl quaternary ammonium mixture than with those that did not.
U.S. Patent No. 3,770,439, filed on January 3, 1972, and issued on November 6, 1973, describes Dr. Taylor's discovery of the excellent mordanting qualities of polymers that include repeating units of vinyl benzyl quaternary ammonium salts of a particular construction. The repeating unit is denoted "Formula A" and its general chemical structure is shown as follows:
The name of the compound signifies its constituent parts. "Vinyl" is the two carbon, three hydrogen part of the structure at the top left:
The lines to the left and right of the carbon atoms represent bonds that link this repeating unit to others. The "benzyl" is comprised of the benzene ring [17] with one carbon and two hydrogen atoms attached:
Bonded to the benzyl group is the "quaternary nitrogen" atom represented by the symbol N+. "X-" represents an anion that is covalently bonded to the positively-charged nitrogen to form a salt. The quaternary nitrogen bonds directly with three chemical groups in addition to the benzyl group. The patent refers to those three as "R groups" and in the representation of Formula A uses the shorthand symbol (R1)3.
The specifications and the claims in issue state that "each R can be the same or different substituent chosen from the group consisting of hydrogen, hydroxyl, alkyl radicals having from one to six carbon atoms, alkoxy radicals having from one to six carbon atoms, or alkanol radicals having one to six carbon atoms...." Only the alkyls are implicated in this lawsuit.
Alkyl groups are a series of compounds of hydrocarbons. [18] They are named in accordance with the number of carbons they contain. The first six members of the series are the "lower" alkyls and they include methyl carbon (1), ethyl (2), propyl (3), butyl (4), pentyl (5), and hexyl (6). An "alkanol" and "alkoxy" are "substituted" alkyls where one of the hydrogen atoms is substituted by a nonalkyl such as oxygen.
Mordants bind dyes through various forces. One is the attraction the typically positively-charged (cationic) mordant has *851 for the negatively-charged (anionic) dye. Another, known as Van de Waal's forces, involves the preference that different hydrocarbons have for each other as compared to the water in which the dyes are dissolved. The hydrocarbon parts of the dye are attracted to the hydrocarbon parts of the mordant, resulting in "hydro-phobic bonding" of the two. The problem for the designer of a mordant is to achieve the optimum balance of these forces for the particular dye, including, of course, matching the water sensitivity characteristics of the mordant to that of the dye.
Variability in mordant water sensitivity relates directly to mordanting qualities. Because the dye is in water, the mordant must be hydrophilic enough to react with the dye, but hydrophobic enough to form a mordant complex that is insoluble. The mordant must also correlate with the water sensitivity of the dye. It should not pull out the dye instantly and thus clog the surface of the image receiver, but it should permit uniform penetration of the image layer by the dye.
Quaternary ammonium salts are very water sensitive. Dr. Taylor discerned that their water sensitivity could be changed by varying the number of carbon atoms in the R groups, but he also realized that longerchain alkyl groups would create complications. With an increase to, for example, 8 carbons, micelle formations, aggregates of small molecules that are not polymers, may occur in the image layer and cause haze or similar optical problems. Accordingly, in July 1970 Dr. Taylor directed his staff to evaluate polymers containing lower alkyl group vinyl benzyl quaternary ammonium repeating units, [19] which ultimately led to the patent in suit.
The parties completely disagree about the scope of the disclosure of the '439 patent. Polaroid asserts that it concerns both homopolymers and copolymers of Formula A. Kodak would limit the claims to homopolymers. Polaroid insists that the patent is directed specifically to integral film. Kodak reads it to describe polymeric mordants conforming to Formula A generally. I find that the patent describes homopolymers and copolymers of Formula A as mordants for integral film.
First, Polaroid's research and experiments were directed to a variety of copolymers of Formula A. In 1970 Dr. Stanley Bedell grafted a Formula A polymer to a polyvinyl alcohol homopolymer. Dr. Taylor tested it on August 31, 1970 and found that it worked well. In 1971 Dr. Jurgen Grasshoff made a straight chain copolymer that included a Formula A polymer. Also in 1971 Polaroid evaluated on a commercial scale a mixture that included a polymer of Formula A and another mordant, poly-4-vinyl pyridine homopolymer. All of these experiments proved the mordanting ability of Formula A. The last-mentioned test showed Formula A to provide faster dye transfer and higher dye density, particularly with cyan, than did the mordant containing only the poly-4-vinyl pyridine.
Second, the language of the patent clearly indicates both homopolymers and copolymers. The specifications refer to "a polymeric material including a polymer of ... [Formula A]...." They describe the invention as comprising "a polymer of Formula A copolymerized with other polymeric materials...." [20] The patent as a whole thus informs the claims which refer to a "polymeric layer comprising a polymer conforming to Formula A...."
Similarly, the descriptions of the film units in the patent persuade me that the mordant disclosed is for integral film. All *852 of the examples use structures of integral film.
Polaroid accuses Kodak of infringing claims 1, 7, and 8. Claim 8 is incorporated by reference into claim 7.
Claim 1 describes an image-receiving element that includes a Formula A mordant with specified R groups as quoted and described above. Claim 7 describes a diffusion transfer product, including "a photosensitive system comprising at least one selectively sensitized silver halide layer integrated with a dye image providing material, processing composition ... and an image-receiving element ..." that conforms to claim 1. Claim 8 adds that the photosensitive system comprises a blue, a green, and a red-sensitive silver halide layer integrated, respectively, with a yellow, a magenta, and a cyan dye image-providing material.
Kodak contends that claim 1 is anticipated, pursuant to 35 U.S.C. § 102(a) and (b); that all claims asserted are invalid as obvious, pursuant to 35 U.S.C. § 103; that the patent is unenforceable for Polaroid's breach of its duty of disclosure; and that, in any event, the PR-10 mordant does not infringe.
Kodak's obviousness argument relies on a number of foreign and United States patents as well as on an article. They include two patents of Dr. Hyman Cohen, a Kodak scientist, French Patent No. 2,003,003, and Belgian Patent No. 734,082; Russian Author's Certificate No. 165,378; British Patent No. 1,022,207, U.S. Patent No. 3,773,509, plus a 1957 article by Messrs. Jones and Goetz, entitled "p. Vinylbenzyltrialkyl Ammonium Salts in Vinyl Polymerization."
The parties agree that the level of skill in this art is very high. A person of ordinary skill would have a Ph.D. degree in organic chemistry and several years in photography systems with a fair exposure to instant photography and polymers.
I find initially that the U.S. '509 patent is not prior art. It was filed on March 9, 1971, and thus subsequent to the invention date of, at the latest, August 1970 to which the '439 patent is entitled.
All of the remaining references do in some manner describe mordants with repeating units that conform to Formula A; the French patent discloses a generic structural formula into which Formula A fits. However, all are directed specifically to matrix printing. None describes the use of the mordant disclosed in an instant, let alone, integral film unit.
French Patent No. '003 discloses a formula with numerous variables. Even Kodak's expert, Dr. Donald Arthur Smith, agreed that the formula permits the construction of a very large number of compounds. None of these are vinyl benzyl quaternary ammonium compounds. Nothing in the patent suggests the particular utility of the lower alkyls. And the patent does not teach that any of the mordants disclosed are useful in integral film units. Indeed, in later applications by Dr. Cohen and others for patents covering a specific class of vinyl benzyl quaternary ammonium mordants for instant photography, Dr. Cohen and his co-inventors distinguished those compounds which included some Formula A polymers from the '003 disclosures. They further claimed them to be patentable over U.S. Patent No. 3,709,690, the counterpart of French '003.
The Belgian '032 patent clearly does include data on the mordanting performance of three Formula A polymers, but again in the context of matrix printing. [21] Moreover, the patent teaches not the utility of Formula A, but the addition of "reactive anchoring" groups to prevent matrix stain, the diffusion of the mordant into the matrix. Reactive anchoring groups react chemically with another polymer included in the gelatin to become immobilized. Such a reaction is both unnecessary and highly undesirable in an integral film unit. It would add yet another reaction that is difficult to control and one that would tend to fuse all the polymers in the image-receiving *853 layer. Reactive anchoring groups are outside the scope of the '439 patent and the references in the Belgian patent to formula A polymers in connection with the disclosure of reactive anchoring groups do not teach the particular use of Formula A disclosed in the '439 patent. Kodak so viewed the Belgian patent on an earlier occasion. In an application relating to a group of vinyl benzyl quaternary ammonium mordants for instant film, that led to U.S. Patent No. 3,625,694, Dr. Cohen again claimed these compounds to be patentably distinct over the Belgian disclosures.
In a similar vein, the British '207 patent teaches the use of a particular "hydrazinium" anchoring group as copolymer with a Formula A compound. It, too, is directed to matrix printing. It, too, is undesirable in instant photography, and neither Polaroid nor Kodak has ever used for commercial instant film a mordant that included such an anchoring group.
The disclosure of a Formula A mordant in Russian Author's Certificate 165,378 is, like the disclosure in the other references, directed to a matrix printing process for movies. This process, both experts agreed, is even more cumbersome than the ordinary matrix printing process and teaches nothing about mordants for instant film.
Kodak argues with respect to the Russian Author's Certificate that it not only teaches the disclosure of '439 but, in fact, anticipates claim 1 of the patent. But claim 1 defines the image layer of an integral film unit; it is not the image layer of any photographic diffusion process. It is not, therefore, anticipated by the Russian Author's Certificate.
The Jones and Goetz article discloses that a Formula A polymer can be used as a mordant in invisible ink which becomes visible when the paper is treated with indigo dye. The authors also found one Formula A compound to mordant an acidic dye in the context of textile printing. Like the other references cited, it is inapposite.
Kodak's argument throughout depends on glossing over the distinctions between matrix and instant dye transfers, and on its assertion that the utility of a mordant for one process necessarily suggests its utility for another. The fact that one skilled in the art would consider as possible candidates in an extensive search the mordants disclosed in these references does not meet the standard of obviousness under 35 U.S.C. § 103. In re Yates, 663 F.2d 1054, 1057 (C.C.P.A.1981), Application of Goodwin, 576 F.2d 375, 377 (C.C.P.A.1978), aff'd without opinion, 599 F.2d 1060 (C.C.P.A. 1979); Trio Process Corp. v. L. Goldstein's Sons, Inc., 461 F.2d 66, 72 n. 18a (3d Cir.), cert. denied, 409 U.S. 997, 93 S. Ct. 319, 34 L.Ed.2d. 262 (1972).
I am persuaded by the evidence that the differences between matrix printing and instant photography are such that the knowledge of one is not directly transferable to the other. Both Polaroid and Kodak tried to adapt for instant photography mordants used in matrix printing. Both failed. Because diffusion transfer, particularly in an integral film, imposes substantial additional requirements on mordants, none of which are considered or addressed in the cited references, I find that those references do not render the '439 patent invalid under 35 U.S.C. § 103.
Kodak asserts that the patent is unenforceable because Polaroid allegedly withheld from the Patent Office material information concerning the usefulness of Formula A polymers as mordants. Specifically it claims that Polaroid knew that these mordants have poor light stability and that they do not function well with yellow dye. I credit the testimony of Dr. Taylor that the light stability tests on which the argument is based and which were conducted in 1965 with Polacolor film produced results that were erratic and, at best, inconclusive. As for the contentions concerning yellow dye, they are based on one manifestation of Formula A. Others, with different sized R groups, provide good mordanting with yellow dye as well. Polaroid did not, therefore, withhold information such as to render the patent unenforceable.
The issue of infringement depends first on the scope of the '439 patent. The mordant *854 of PR-10 is a copolymer, and Kodak asserts that the patent is limited to homopolymers of Formula A. Since I have earlier addressed this argument, see infra p. 851-852, and found the '439 patent to include copolymers of Formula A as well, this defense fails.
The second argument centers on the composition of the PR-10 mordant. The parties agree that it has three different repeating unitsstyrene, divinylbenzene and vinylbenzyldimethylbenzyl ammonium chloride. Polaroid contends that the first two repeating units are not mordants at all. According to Polaroid, the styrene balances the hydrophilic/hydrophobic properties of the polymer and the divinylbenzene serves to cross-link all three of the repeating units. The third unit, Polaroid says, is the mordant of the polymer and it infringes '439. Kodak insists that the compound cannot be so compartmented, that its mordanting properties are due to the combined effect of all the parts of the polymer. I am persuaded from the evidence that the quaternary nitrogen component of the PR-10 mordant is the one that performs the function of capturing and immobilizing the dye. I am equally persuaded, however, that the other two repeating units are essential to achieve the good mordanting quality of the whole.
Finally, Kodak contends that the vinylbenzyldimethylbenzyl ammonium chloride is a structure not disclosed or claimed in the '439 patent. Again, the parties agree that the allegedly infringing polymer is a vinyl benzyl quaternary ammonium structure with 3 R groups. Two of the R groups are admittedly methyls and therefore lower alkyls that fit squarely within the asserted claims. The third is a benzyl group; it includes a 6 carbon benzene ring plus an additional carbon. It admittedly is not a lower alkyl and it does not fit the language of the patent. Polaroid asserts, however, that the benzyl is a substituted alkyl which is equivalent to a six-carbon hexyl. Alternatively, it argues that under the doctrine of equivalents, the PR-10 mordant infringes the patent in suit because the dimethylbenzyl quaternary ammonium repeating unit achieves results equivalent to those achieved with Formula A hexyl.
The evidence at trial disclosed considerable disagreement about the terminology used to describe the benzyl R group. Dr. Taylor testified, and Kodak's experts agreed, that strictly speaking it is a substituted alkyl consisting of a one carbon methyl substituent and a six carbon benzene ring. The evidence also showed that the presence of the benzene ring transforms this R group into an aryl. I find that both terms are correct. A substituted alkyl is an alkyl in which one hydrogen has been replaced by a nonalkyl, a definition that encompasses the R group in issue. An aryl compound is one which has the benzene ring structure, a definition that also includes this R group. The '439 patent claims only "alkyl radicals having from one to six carbon atoms" and certain specified substituted alkyls not including benzyl. Accordingly, I conclude that the choice of nomenclature does not dictate the result. The benzyl R group is simply not claimed.
The question remains whether the PR-10 mordant infringes under the doctrine of equivalents.
The parties agree that under the doctrine of equivalents infringement may occur if the defendant's product or process performs the same function in the same way to obtain substantially the same result as the product or process disclosed in the patent. Graver Tank and Mfg. Co. v. Linde Air Products Co., 339 U.S. 605 , 70 S. Ct. 854, 94 L. Ed. 1097 (1950); Rich Products Corp. v. Mitchell Foods, Inc., 357 F.2d 176, 182 (2d Cir.), cert. denied, 385 U.S. 821, 87 S. Ct. 46, 17 L. Ed. 2d 58 (1966). The burden of establishing equivalence is on the plaintiff.
A comparison of the PR-10 mordant, or even of its quaternary nitrogen component, with Formula A discloses that both unquestionably perform the same mordanting function. I find also that both quaternary nitrogen repeating units perform that function in substantially the same way, although I credit the testimony of Dr. Smith *855 that the PR-10 compound is a stronger mordant than any manifestation of Formula A. If the comparison is between the PR-10 mordant as a whole and Formula A, they clearly do not function in the same way because the divinyl benzene component of PR-10 permits cross-linking of the polymer and results in a latex compound.
Regardless of how they are viewed, the quaternary nitrogen repeating units of PR-10 and the '439 patent do not, in any event, achieve the same result. As discussed earlier, the reason for limiting the number of carbon atoms in Formula A to six was Dr. Taylor's perception that a larger number would cause optical problems. The PR-10 mordant confirms that understanding. It is a cloudy dispersion and does cause optical interference. Thus, while it achieves good mordanting results, the PR-10 compound does so with precisely the disadvantage predicted for compounds with more than six carbons. Kodak solves the optical problem by incorporating matching refractive indices into the gelatin in which the mordant is mixeda solution wholly outside the scope of '439. Even comparing the mordanting results of dimethyl-hexyl and dimethyl-benzyl R group polymers, I am not persuaded that they are equivalant. The tests performed by Polaroid to show equivalence do not succeed. The results were different even though the hexyl used was not a straight chain R group but a ring structure.
The PR-10 mordant does not, therefore, infringe any of the claims of the '439 patent asserted. It does not read on the claims nor has Polaroid shown equivalence.
In summary, I find that the '439 patent is valid, but that the accused mordant does not infringe any claims asserted.
Photographic prints, whether produced by conventional means or by an instant process, whether on a single support or consisting of a laminate, have a tendency to curl and to distort. [22] Although the parties disagree about the precise manner in which curl or distortion is induced in integral film units, they agree that it is the presence of moisture at some point in the life of the film unit that may bring about a temporary or permanent deformation of the print. The patent in suit, U.S. Patent No. 3,578,540 to Dr. Land, describes an integral film unit "especially designed to resist distortion due to physical changes, particularly the quantity and distribution of moisture in laminae comprising the [film unit]...." The evidence shows and the patent points out that the effects of moisture on the dimensional integrity of the supports are exacerbated in an integral film unit because the quantity and distribution of moisture within the film units continue to change for a relatively long period of time.
It was well known in the art that curl and distortion are caused by uneven stresses on the supports. It was also known that these stresses are caused by the absorption of moisture by the supports and subsequent drying. The supports tend to respond unequally to the moisture itself and to the presence of alkali therein. The photographic layers also absorb moisture and swell as a result. Upon drying, the layers shrink and thus also exert forces, uneven forces, on the supports.
Dr. Land hypothesized that in an integral film unit the direct and indirect impact of moisture operates initially on the inside surfaces of the supports, and if the impact or stress on the supports is balanced the problem of curl is solved. That is, identical supports arranged in such a manner as to respond equally to what is contained between them is the answer. He thought such a balanced response could be attained by using supports that have both good mechanical stability and extremely low permeability to water and water vapor. Nonabsorption of water by the supports eliminates that distortion caused by the *856 presence of moisture. Thus, the patent discloses that "a generally flat, undistorted and dimensionally stable, yet flexible" film unit can be achieved by using supports which are "symmetrically disposed with respect to the surrounding atmosphere and dimensional changes" and which are made of "materials that exhibit low water absorption and low water transmission rates."
The specifications describe a film unit that uses symmetrical supports. Symmetry in this context is described as substantially equal reaction of the two supports to the presence of moisture. The essential characteristic of the supports, according to the patent, is that they be "relatively impermeable to and non-swellable by moisture." "Suitable materials include alkaline solution impermeable materials such as vinyl chloride polymers; polyesters such as polymeric films derived from ethylene glycol terephthalic acid, for example, polyethylene terephthalate, polycarbonates, phenylene oxide polymers, acrylics, polyethylene and polypropylene." The patent cautions that the list is exemplary and not exhaustive, and that in fact other materials with superior water absorption qualities are known. Although these materials may not have suitable optical qualities for the transparent support, they are ideally suited for use as the opaque support layers. The example in the patent uses polyester, i.e., polyethylene terephthalate. Polyester is also the material used in SX-70 and PR-10 film units. [23]
Polaroid asserts infringement of claims 5, 6 and 8. Claims 5 and 6 incorporate by reference claims 1 and 4, and claim 8 incorporates claim 7.
Claim 1 describes a laminated photographic product comprised of two dimensionally-stable support layers, at least one of which is transparent, but both of which have substantially the same physical responses to the presence of moisture in the image-containing layer sandwiched between them. The image-containing layer includes a silver halide emulsion layer; an intermediate lamina comprising a polymeric film-forming material and an opacifying agent; and an image-receiving layer containing a dye-diffusion transfer image. Claims 4 and 5 add the requirement that all support layers be formed of the same polymeric material and have substantially the same physical characteristics, and that they be relatively impermeable to water vapor. Claim 6 specifies that they be made of polyester. Claims 7 and 8 are similar and reiterate the support layers' relative impermeability and similar physical response to moisture.
Kodak challenges the validity of the patent on the ground that it is anticipated by Kodak's BIMAT film. It further asserts that the only new aspect of the film unit described is the selection of the support materials. According to Kodak, the choice of polyester is obvious, as is the use of symmetrical supports. Kodak also denies infringement.
The initial dispute between the parties concerns the nature of the disclosure. Whereas Kodak views the patent as teaching nothing more than the choice of polyester as the material of choice, Polaroid defines the invention by reference to specific qualities of the supportsthey must be symmetrical and substantially impermeable to moisture.
Polyester was developed by Dupont and it became available for use as film in 1955. DuPont proclaimed it as superior to cellulose acetate in optical clarity, durability, dimensional stability and low moisture sensitivity. These claims were unquestionably true and the photographic industry began using a polyester film base in the late 1950s in various applications. It is undisputed that for some time before the invention of the '540 film unit both parties employed polyester and prescribed it in a number of patents, including patents pertaining *857 to instant photography. [24] It is also clear, however, that for reasons hereafter set forth, neither party considered using two polyester supports with integral film units until Dr. Land did so.
As noted earlier, it was well known long before Dr. Land conceived the idea of symmetrical supports that one cause of curl and distortion was the uneven drying of print or film unit components and the consequent uneven forces on the support. The evidence shows that the conventional response was to provide a balance against these forces. An example of such balancing used in conventional film was coating the side opposite the photographic layers with "pelloid," a material which expanded and contracted in a manner similar to the photographic layers. It thereby opposed the forces generated by the drying of the photographic layers. [25]
This means of balancing is not useful, however, in integral film unitsstructures kept together in a closed system before, during, and after development, which remain in contact with and respond to not only water but also the alkali in the processing composition. Dr. Land's insight lay in the recognition that the problem has to do not solely with the reaction of the supports to that environment but also to each other. The film unit will remain flat if the supports are symmetrical in the sense that both have low water transmission and absorption rates. It had theretofore been thought that to maintain image stability one of the supports had to be water permeable so that the film unit could dry fairly rapidly. Contrary to that prevailing wisdom, Dr. Land believed that with the presence of the polymeric acid layer in the film unit a wet environment would not harm the image ( see Part II, the '821 patent, supra ). Accordingly, the combined use of the polymeric acid layer and symmetrical supports would result in a film unit that was both stable and flat. That Dr. Land's hypothesis is correct has been proven by countless film units produced with both features. Thus, I find that the '540 patent discloses substantially more than the choice of a known material. The question remains whether the concept of symmetry as articulated in this patent was taught in the prior art.
The parties agree that a person of ordinary skill in the art to which the '540 patent pertains would have had at least an undergraduate degree in chemistry or chemical engineering and several years experience in the fields of plastics and film. Each party disparages the qualifications of the opposing expert. I find both not only qualified, but highly qualified.
The references cited against the patent in suit fall into several categories. First, are the patents pertaining to peel-apart film units. Kodak's '915 patent and Polaroid's '775 patent describe a color instant film with a layer structure similar to that of '540. The former includes polyester in a comprehensive list of possible support materials. The latter suggests polyester as the material for both support layers. However, because both disclose only peel-apart film units, neither addresses the particular problems of curl in the closed system of an integral unit. Neither teaches the concept of symmetry.
The second category includes U.S. Patent No. 2,563,342 and U.S. Patent No. 2,983,606, both of which do describe integral embodiments. The '342 patent is directed to black and white film. One of the objects of the patent is to obtain greater resistance to curling, and it attempts to do so by the use of two support layers made of the same material, cellulose acetate. Polyester was not, at the time of this patent, available. In any event, despite the depiction in '342 of a film unit with identical supports, the patent does not teach the feasibility *858 of using symmetrical water-impermeable supports which by definition will maintain a wet environment for a period of time. Indeed, both Polaroid and Kodak found the use of cellulose acetate for both supports to be impracticable.
The '606 patent discloses a film unit with a structure like that of '540. Although directed primarily to peel-apart film, it does contain a description of an integral format that has two supports. It mentions cellulose acetate for the negative support, baryta paper for the positive support, and polyester not at all. The patent admittedly teaches nothing about choosing materials for those supports. It certainly does not teach the use of water-impermeable symmetrical supports, and I do not find the concept of symmetry to have been obvious even to a person of the high skill necessary in this field.
Finally, Kodak points to its own BIMAT process as evidence that the invention of the '540 patent is old and that symmetry in support is obvious. BIMAT was used for aerial and satellite reconnaissance photographs. It consists of a large roll of 4 mil Estar, the Kodak tradename for polyester film base, on which was coated a gelatin layer containing a processing agent. The user soaked the gelatin in a prescribed solution and brought this sheet into contact with a sheet containing the exposed negative. The latter was also carried on a large roll and was exposed frame-by-frame. When the two sheets are brought together the exposed negative is developed and a diffusion transfer image formed on the Estar sheet. After development, the negative is stripped away. Because the image layer on the Estar sheet was wet and sticky, it could be, and often was, covered with a second transparent polyester support to permit handling of the film. The BIMAT process thus provides transparencies, not reflection prints. These transparencies were stored on a spool or reel and could be viewed on a light table. Particular frames could then be cut out and processed again to make photographic prints.
Mr. John Otto, now a marketing product coordinator with Kodak, and formerly a photographic technician, brought to court samples of BIMAT processed aerial film that, he testified, had been made in 1966. They were flat and they were made of two sheets of polyester. However, the similarity with the disclosure of '540 ends there.
Kodak never regarded BIMAT as a permanently closed system. The laminate is made of two long strips of film, not discrete film units; and Kodak experienced difficulties making the cover sheet adhere to the BIMAT film. The informational brochure for this product states that an image will last about a week to ten days and it recommends that if long storage is desired, the film should be washed and dried. [26] It differs from an integral film unit in that the BIMAT sandwich is filled only with hardened gelatin, the transferred silver halide and a residue of processing material, compared with the multiplicity of layers and the retained moisture in an integral film unit. Given these fundamental differences in process, function and resultant productand despite the facts that it uses two polyester supports and that some flat samples existI find that BIMAT does not anticipate the '540 patent, nor teach its invention.
The inventiveness of the patent is further underscored by Kodak's unsuccessful efforts to achieve a flat and stable film unit. Kodak's efforts, begun in 1969, focused initially on systems that had at least one water permeable support, because it then adhered to the prevailing wisdom that rapid drying was essential to image stability. For the most part it used Estar for the image layer support and tested with it more than 600 different support materials. After the introduction of SX-70 Kodak began to use two polyester supports.
The PR-10 film unit differs from the literal language of the claims in two respects. *859 It uses pelloid layers on the outside of both supports. In addition, the two supports are of different thickness4 mil for one, 6 mil for the otherand are therefore of different stiffness as well. Kodak also claims departures in the PR-10 from the description of the laminae and the diffusion path of the '540 patent.
I am not persuaded by the evidence that the addition of the pelloid layers corrects any tendency to curl. On the contrary, the evidence suggests that a PR-10 film unit without pelloid is no more prone to curl than one with the pelloid layers intact.
That the supports of PR-10 are of different thickness and stiffness is undisputed. Kodak argues from this fact that the supports therefore do not have the same physical response to moisture as required by the claims. I credit the testimony of Dr. Land, however, that the important characteristic is the low permeability to water of the inside surface of the support. That is what determines the physical response of the support layer as a whole to moisture. That being so, the difference in thickness does not avoid infringement of all claims asserted.
Finally, Kodak argues that because the transfer image of PR-10 is not formed by diffusion of the dye image-providing materials through the layer formed by the processing composition, it is not formed by diffusion "through [the] intermediate lamina," and PR-10 does not infringe the asserted claims. The argument is premised on a reading of claims 1 and 7 that would limit the intermediate lamina to a layer formed by the processing fluid. I credit Dr. Land's testimony that the intermediate lamina of these claims are not so limited.
In summary, claims 5, 6 and 8 of U.S. Patent No. 3,578,540 are valid and infringed.
Every camera must incorporate a mechanism for advancing film into position to be exposed and after exposure away from the shutter opening and usually onto a roll for storage. Instant photography employs not rolled film but separate thin, flexible film units which are stacked in a cassette, typically in exposure position and which must be moved one at a time. Moreover, in an instant system, the film unit must, after exposure, move into the spread rollers to break the pod and distribute the processing composition contained in it over the entire photographic portion of the film unit. Thus, in a camera for instant photography, the film-advancing system must not only move the stacked film unit, it must do so one at a time and it must drive the spread rollers at an even and proper speed for a period long enough to both spread the processing composition and fully eject the film unit out of the camera.
During the development of the SX-70 Polaroid engineers and an outside consultant designed many different film-advancing systems. The principal variables were the location and shape of the motor and the configuration and mechanics of the pick, the device to move the film unit. All of the early designs placed the motor in or near the rollers, that is, in front of the cassette and camera, and they used friction devices or continuously reciprocating front picks. In the fall of 1969, after a number of pre-production models of cameras had been built, it became apparent that substantial problems remained with the pick in its various manifestations. Even in the then latest model, the PT III, the pick was unreliable in that it sometimes failed to transport even one film unit while at other times it transported more than one. The problem was sufficiently serious that Robert Duncan, the project manager of the SX-70 program, feared that Polaroid would not be able to meet the projected introduction date for the SX-70 camera and film. Dr. Land and others then engaged in an intensive effort to find a solution. As a result, Dr. Land and Messrs. Blinow and Leduc, a Polaroid engineer and his assistant, developed a transport system which gave rise to two patents, for the rear pick and for the *860 rear motor and gear train. The pick, which had been incorporated into earlier commercial cameras and the several experimental models before the fall of 1969, included, as mentioned earlier, both friction devices such as rubber fingers or wheels that pinched on the surface of the film unit, and front picks that entered holes in the film unit and pulled it into the spread rollers. Because the film units were thin and flexible, it had earlier been thought that they had to be pulled rather than pushed out of the cassette.
The friction devices were in practice unreliable. They did not always move the film unit at uniform speed; the pressure of the device could mechanically alter the silver halide grains and it could push the film unit out of alignment with the exit slot; the rubber tended to harden with age or become contaminated and was then unable to engage the film unit constantly and steadily. The front pick also presented several additional difficulties. The perforations required in the film unit for the operation of the front pick jeopardized the moisture integrity of the pods, they added to the cost of production, and they marred the appearance of the finished picture. In addition, a hole had to be built into the cassette containing the film unit to permit access of the pick to the film unit. Because that hole was near the exit slot it jeopardized the light tightness of the system.
These combined disadvantages defined the problem that required solutionto move film reliably and one at a time, without disturbing the alignment of the remaining film units relative to the exit slot, without requiring holes in the film unit and without fogging the unexposed film units. Dr. Land proposed that a single pick enter a slot in the cassette at the end opposite the spread rollers, engage the film unit at the rear, and from there push it into the spread rollers. This solution eliminated the need for holes in the film unit, it avoided any possibility of fogging, and it proved to be extremely reliable.
Dr. Land's rear pick was incorporated into the next two experimental models, the U-2 and U-3 built in early 1970. In these models the motor was located in the front of the cassette near the spread rollers and the new pick was variously connected to the motor or crank by a bar or a strap. Consideration had also been given to connecting it by a chain, a cable or a belt. It was then that Dr. Land assigned Messrs. Blinow and Leduc the responsibility of designing a drive system for the next model, the U-4. They proposed locating the motor in the rear of the camera and connecting it to the spread rollers by means of an elongated gear train. They also worked out a mechanism for stopping the movement of the pick while the film unit travelled through the spread rollers, until the time came for the pick to return to its position at the rear of the camera. The first camera to incorporate both improvements was the U-42 which was completed in August 1970. It became the commercial SX-70.
The rear pick has proven to be very successful and completely reliable. Dr. Land testified, without contradiction, that this pick design has moved billions of pictures and he has never heard of or seen a failure. It is disclosed in U.S. Patent No. 3,753,392, issued to Dr. Land on August 21, 1973, on an application filed on August 12, 1971, which was a continuation-in-part of an application filed August 19, 1970. The drive system with rear motor, elongated gear train and pick disenabling mechanism is the basis of U.S. Patent No. 3,709,122. The application for this patent was filed on May 10, 1971. The patent issued January 9, 1973. Polaroid alleges infringement of both, and I will consider them in reverse order.
According to the specifications, the invention relates to "a film-advancing means for use with e.g. self-developing cameras of the single lens reflex type, and more particularly, to a marriage between the film-advancing means ... and other subsystems of the camera to provide a structure which is slim, compact and readily *861 lends itself to transport within a user's pocket." More precisely, the specifications describe an arrangement that includes a motor at the rear of the camera, near one end of the film cassette, a film transport means in the form of a pair of rolls at the opposite end and a gear train, i.e., a plurality of gears coupling the motor and rolls which extend along one side of the film cassette.
Mounted on one gear of the gear train is a pin which engages and moves the pick mechanism and therefore the film unit. Because the gear carrying the pin moves through more than one revolution for each exposure, to prevent the pick from continuously moving back and forth a latch is provided on the pick apparatus that cooperates with a cam on the gear train to stop the pick "near the end of its travel toward the rolls, for a predetermined period of time, e.g., a period of time at least as long as that necessary to move the film unit out of engagement with the rolls." In operation, the gear train reduces the high speed of the motor to three different, slower speeds as needed to drive, respectively, the pick, the rolls and the cam.
Translated and somewhat simplified, the motor and connected gear train are activated by pushing the shutter release button on the camera. Insofar as is relevant to this patent, as the gears revolve, the pin engages the pick apparatus and drives it forward so that one film unit is delivered to the rolls. [27] Although the gears continue moving to drive the rolls, the latch and cam are arranged so that the pick is held in place from the time the film unit enters the rolls until it exits. At that point in time the cam releases the latch and the pick returns to its rear position, ready to start the next cycle, and the motor stops.
Polaroid asserts infringement by Kodak's EK-6 camera of claims 1, 2, 3, 6 and 8 of the '122 patent.
Claim 1 describes the arrangement and operation of the drive system components: "motor means" mounted adjacent one end of the structure supporting the cassette (the rear motor); "transport means" mounted at the opposite end of the cassette structure for engaging and moving a film unit (the spread rollers); and "motiontransmitting means" coupled to the motor means and extending along one side of the cassette structure (the gear train). The claim also calls for "means extending from said motor means (the pin) for engaging and driving film-advancing means" (the pick) from a "first position" to a "second position" "to advance an exposed film unit ..." into the spread rollers.
Claims 2, 6 and 8 depend on claim 1, and claim 3 depends on claim 2. They add the simultaneous operation of the pick and rollers (claim 2), the disenabling of the pick "for a predetermined period of time" (claim 3), a gear train consisting of a plurality of gears (claim 6), and a flange to drive the pick from the gear train (claim 8).
As is true with respect to all of the other patents in suit, Kodak contends that the claims in this one are invalid. The invalidity defense is based on 35 U.S.C. § 102(e), (f) and (g) and § 103. Kodak also denies infringement.
The parties have divided the prior art alleged to be pertinent into four categories, a group of rear motor camera patents, two groups of front motor camera patents, a number of Polaroid camera models, and a number of commercial cameras.
The rear motor camera patents, U.S. Patent No. 3,714,879 to Land, Blinow and Eloranta; U.S. Patent No. 3,641,889 to Eloranta; U.S. Patent No. 3,688,667 to Paglia; and U.S. Patent No. 3,685,416 to Coughlin, are asserted to be references under both sections 102(e) and 103. All have application filing dates between September 2, 1970 and April 16, 1971, which are earlier than the filing date of the '122 patent. All of these patents disclose a motor located at the rear of the camera and spread rollers *862 at the front. All disclose a "motion transmitting means" connecting the motor and rollers, which, at least, in the case of the '879 patent, is a gear train substantially identical to that of '122. All lack disclosure of the pick drive and disenabling mechanism of claim 1, however, even according to the testimony of Edward Kaprelian, Kodak's expert. None, therefore, meets the strict requirements of anticipation.
Polaroid also questions whether the rear motor patents may even be considered prior art. Since they bear earlier filing dates than does the '122 patent, Polaroid has the burden of proving that the invention of the '122 patent was both conceived and reduced to practice before September 2, 1970, the date the '889 application was filed. Hazeltine Research v. Brenner, 382 U.S. 252 , 255-56, 86 S. Ct. 335, 337-38, 15 L. Ed. 2d 304 (1965); Radio Corp. of America v. International Standard Electric Corp., 232 F.2d 726 (3d Cir.1956). Reduction to practice occurs when the invention is incorporated into a working device. Boyce v. Anderson, 451 F.2d 818, 820 (9th Cir.1971); Automatic Weighing Machine Co. v. Pneumatic Scale Corp. 166 F. 288, 303 (1st Cir.1909). I find that Messrs. Blinow and Leduc thought of locating the motor in the rear in late March 1970; and during April, May and June they worked out and tested the disenabling mechanism and the details of the gear train. Moreover, the evidence is undisputed that at least one of the working camera models, the first U-4 model, produced in August 1970, incorporated the rear motor drive system with pick disenabling mechanism. Accordingly, the rear motor patents are not prior art and do not invalidate any of the claims of the '122 patent under 35 U.S.C. § 102(e).
Kodak next relies on a number of front motor cameras, all of which are acknowledged prior art: U.S. Patent No. 3,683,770 to Land; U.S. Patent No. 3,447,437 to Tiffany; U.S. Patent No. 3,511,152 to Erlichman; U.S. Patent No. 3,545,357 to Erlichman; and U.S. Patent No. 3,563,145 to Bendoni. It asserts that all teach a pick disenabling mechanism and that the location of the motor in front is not essential to obtain a slim and compact configuration nor is it critical to the operation of the drive system. Neither the testimony of Mr. Kaprelian nor Exhibit DF-765, a chart comparing the elements of the claims of the '122 patent with the disclosures of the asserted prior art references, persuades me that the front motor camera patents anticipate the '122 invention. All claims of '122 are expressly limited to defined locations for the motor, spread rollers and "motion transmitting means." At this most basic level, therefore, none of the front motor camera patents meet the location requirements of the asserted claims of '122. Moreover, the requirement of a disenabling mechanism is admittedly met only in part by Bendoni '145 and Erlichman '357; and I find it is met not at all by Erlichman '152.
Finally, Kodak contends that in light of the references cited above, as well as a number of commercial cameras in use before the '122 invention and certain camera models built at Polaroid in 1969 and 1970, the '122 patent is invalid as obvious. The parties agree that the defense of obviousness is less strict than that of anticipation. Shanklin Corp. v. Springfield Photo Mount Co., 521 F.2d 609, 617 (1st Cir.1975), cert. denied, 424 U.S. 914, 96 S. Ct. 1112, 47 L. Ed. 2d 318 (1976). They do not agree about the scope and content of the prior art.
The art to which the '122 patent pertains is the art of camera design in general, not merely the art of designing instant cameras. The level of skill in that field is high; to be deemed skilled a person would have to have an engineering degree and at least four years of experience in camera design.
The separate elements of the claims of '122 are unquestionably taught by the prior art. The concept of a gear train, an arrangement that consists of a driving gear, a driven gear, and at least one intermediate gear, was well known in 1969-70, as was the fact that the gears could be combined in "an endless variety of ways in order to meet particular requirements of *863 shaft position, directions of rotation and gear ratio." H. Merritt, Gears, (3d ed. 1954). Moreover, gear trains were used in cameras, as demonstrated by the Bell & Howell Autoload 342 and the Yashica Sequelle cameras; and they were incorporated into several of the prior art patents. Both U.S. Patent No. 3,683,770 to Land and Bellows and U.S. Patent No. 3,447,437 to Tiffany show extended gear trains that connect the motor and rollers. The latter patent also teaches the use of speed-reducing gears.
The idea of a mechanism to move each film unit with but one back and forth motion by the film-advancing device was also old. Two front motor camera patents, U.S. Patent Nos. 3,702,580 and 3,678,830, both to Erlichman, teach the use of single stroke film picks. The Erlichman '152 patent describes means of disenabling the pick by the movement of the film against a ramp. Again in the Bendoni '145 patent, the movement of the unit film activates a disengaging mechanism that locks the pick in resting position until the next cycle. Even the idea of disenabling the pick by disengaging it from the continuously moving gears was known. The Erlichman '357 patent describes such a variant whereby the film unit, upon reaching a lever, unhooks the pick gear from the gear train until the processed film is removed from the camera.
The rear motor camera patents, although not prior art, are nevertheless relevant on the issue of obviousness. The proximity of the application filing dates of these patents to that of the patent in suit permits the inference, which I draw, that the work underlying those patents was done at about the same time as was the work on the '122 patent. These patents thereby indicate the level of skill in the art at the time and they suggest that there is nothing unobvious about locating the motor in the rear and using a gear train to connect motor and rollers. [28]
Polaroid's principal witness, Dr. Milton S. Dietz, testified that the advance of the '122 lay in the structure described and its particular arrangement. The patent itself states that it relates to a "marriage" between the pick and other subsystems that results in a camera that is slim and compact. The essence of the arrangement is the location of the motor in the rear. Once the motor is placed in the rear, the location of the remaining subsystems is dictated by the functional demands of the camera. Polaroid argues that so locating the motor was novel because it contradicted a number of known engineering principles and preconceptions, e.g., a motor should be near the primary load to be driven; and a transport system should be as short as possible to minimize the number of moving parts because a long gear train will bring about a loss of efficiency. However radical a departure from earlier instant cameras the rear motor may have represented, it was nevertheless taught by the Bell & Howell Autoload 342 and the Canon Dial 35 cameras, which teaching had proven the engineering principles to be less than inviolate. Even considering the arrangement as a whole, I find that it was, in view of the prior art, obvious.
The arrangement of the components of the drive system do not necessarily describe the different timing functions implicit in the claims of '122. But the timing too is taught by the prior art. As noted earlier, the gear train of Tiffany '437 describes the use of speed-reducing gears. I also credit the testimony of Mr. Kaprelian that the use of compound gears to achieve speed reduction and torque magnification was well known in 1969.
No one item of cited prior art discloses each and every element of the '122 patent, but I find that when taken altogether, the commercial cameras and the front motor camera patents would lead one skilled in the art to the invention of '122. Claims 1, *864 2, 6 and 8 of the '122 patent are therefore invalid under 35 U.S.C. § 103.
I consider the issue of infringement for the reasons stated earlier and find that, if the patent is valid, all claims asserted against Kodak are infringed. Kodak argues that it does not infringe any claims because the motor and a number of the gears of the EK-6 camera are above the film plane and that therefore they are not in the particular positions specified in the patent. But the claims do not specify the position of motor and gear train in terms of planarity vis-a-vis the film cassette. Nor do the claims call for a "slim and compact" camera as Kodak asserts. [29] The EK-6 camera is equipped with a motor located at one end of the camera, spread rollers at the opposite end, and a gear train connecting the two which runs alongside the cassette. Extending from one of the gears in the gear train is a cam that drives the pick. In operation, the system works as described in claim 1. The pick moves from one specific position to anotherfrom a first position to a second and ultimately back to the first. The gear train of EK-6 provides simultaneous operation of pick and spread rollers and thus infringes claim 2.
The system includes a mechanism, a single revolution clutch, that disenables the pick for a predetermined period of time necessary for the film unit to move through the spread rollers. That mechanism infringes claim 3.
Claim 6 is infringed by the gear train which extends from motor to spread rollers. The flange on the EK-6 pick mechanism which is driven by the cam on the gear train infringes claim 8.
In summary, I find that the '122 patent is not invalid under 35 U.S.C. § 102, but that its invention was obvious in view of the prior art and that the asserted claims are therefore invalid under § 103. If the patent were valid, all of those claims would be infringed by Kodak's EK-6 camera.
After outlining the problems of the then-known transport systemsthe friction devices and front picksthe specifications describe a film-advancing apparatus for use with a cassette that is the subject of yet another patent, U.S. Patent No. 3,415,644. The cassette has an exposure aperture in the forward wall, a slot in the front end through which the film unit exits into the spread rollers and "at least one elongated slot which extends rearwardly along one lateral side of the forward wall and at least part way down the cassette's trailing end wall." The film-advancing apparatus is mounted within the camera and includes "a film-engaging member which is adapted to extend into the slot in the cassette's forward and trailing end walls and engage the foremost film unit at or near its trailing end or at its trailing edge ..." in order to move it out of the cassette and into the bite of the rollers. The specifications discuss the invention in terms of a transport and processing system. Because this rear pick necessarily functions as part of such a system, it must be considered in the context of the entire system even though other aspects of the system are variously disclosed in several other patents, including '122 and '644.
Polaroid accuses the Kodak EK-6 camera of infringing claims 1, 2, 3, 4 and 12.
Kodak asserts invalidity under 35 U.S.C. § 103; it alleges that the patent is unenforceable; and it denies infringement.
Claim 1 calls for a combination of cassette and camera. The cassette contains a plurality of thin flexible film units and has an exposure aperture, an exit slot, and a rear pick opening "near an opposite end of said cassette." The camera has a "first film-advancing means adapted to extend into said opening for engaging [the] foremost film unit at [the] second edge thereof ..." (the rear pick, which is shaped like a *865 hook), [30] a "second film-advancing means" (the spread rollers), a motor, and a means for coupling the motor to the pick and rollers for advancing the film unit out of the cassette into the rollers and ultimately out of the camera. Claims 2 and 3 depend on claim 1 and add, respectively, simultaneous motion of the pick and rollers and reciprocating movement of the pick. Claim 4 depends on claim 2 and adds to it reciprocating movement of the pick. Claim 12 describes the method of exposing and processing a succession of film units by using the cassette, film units, and camera of claim 1.
The relevant art to which the '392 patent pertains is camera design. The prior art cited again falls into several discrete categories: a number of patents disclosing front picking mechanisms; [31] a number disclosing rear picking mechanisms; [32] and a number of commercial cameras.
Two of the front pick patents, Erlichman 3,511,152 and Bellows 3,505,943, were cited by the Examiner in rejecting the application as initially filed. That application claimed that the pick engaged the film unit "at or near its trailing end." The Examiner thought it obvious, in view of the Bellows '943 rear pick patent, to move either the friction wheels of Tiffany '437 or the front pick of '152 to the rear. In view of the '437 motor driven film advance system, the Examiner also thought it obvious to motorize the rear pick of Bellows '943. Polaroid thereafter amended the claims of the patent in suit to a rear pick that engaged the film unit not "at or near the trailing end," but only at the trailing "edge." In view of that history, I must read the patent narrowly and the claims as so limited. Graham v. John Deere Co., 383 U.S. 1 , 32-34, 86 S. Ct. 684, 701-02, 15 L. Ed. 2d 545 (1966); Burland v. Trippe Mfg. Co., 543 F.2d 588, 591-2 (7th Cir.1976); Itek Corporation v. Information International, Inc., 476 F. Supp. 1043 , 1047 (D.Mass.1979).
The limitation as to the point and manner of the '392 pick's engagement of the film unit renders the teaching of the front pick patents inapposite. Front picks operate either on the surface of the film unit or by entering holes in the film unit. All operate on the principle that the film unit has to be pulled out of the cassette. That a pick can push the film unit and that it can do so while fully maintaining the latter's physical integrity is not taught, nor even suggested by any of the front pick patents, either singly or in combination. Indeed, Mr. Kaprelian agreed that engineers of ordinary skill would first look to the use of holes in the film for engaging and moving it.
The prior art also includes a number of patents with picking mechanisms in the rear position. Although Kodak in its brief characterizes every such mechanism as a "reciprocating rear pick," the cited patents in fact disclose a great variety of devices, most of which are not picks as that term is used in the '392 patent. Bellows '943 was one of the patents cited by the Examiner in rejecting the original application. It discloses a manually operated friction finger that pushes against the film unit near its trailing end. Like the wheels of Tiffany '437, the finger of Bellows acts on the surface of the film unit with all the disadvantages of that arrangement. Insofar as the Bellows finger enters the cassette through the exposure aperture, its potential for causing harm to the photosensitive area of the film is even greater than that of front pick devices. The Bellows rubber piece does not teach the '392 hook-like pick *866 that pushes the film unit from the rear edge.
The '452 and '370 patents to Land and Wareham, respectively, disclose scanning cameras that are similar in operation. They were in fact never built because the design was too complex to be practical. The film transport system of these cameras is moreover totally different in function and design from that disclosed in the patent in suit. The film is moved out of the pack through rollers into exposure position by means of a lever which is mounted in the pack and is not part of the camera. After exposure, the direction of the rollers is reversed, the pod is then broken, and the processing composition is spread on the return trip. The lever is manually operated, and it does not push the film into the rollers for spreading purposes. These patents do not use nor do they teach the rear pick.
Brieloff '400 and Fish '606 describe cameras of the type once used by street vendors. Both cameras take photographs on postal cards. The Brieloff camera contains a magazine loaded with a number of photosensitive postcards. After exposure, a card is advanced through two pairs of friction wheels, one on each side, into a developing tank. The system's resemblance to '392 stops at this point, however. The film-advancing system is manually operated by a crank. The card travels toward the tank along with a front plate which is an integral part of the camera. The card is held against the plate by friction. The plate, in addition, has a shoulder across the entire trailing or top edge which also holds and moves the card as the plate moves. The Brieloff camera would not work with an instant film unit: it could not advance the film into spread rollers, nor could the processing system of the Brieloff camera perform the composition-spreading function. Brieloff does not include a separate cassette with an opening for the pick, and the shoulder across the moving plate does not suggest a separate pick that enters the magazine and moves only a film unit.
Kodak points out that Polaroid did concede the pertinence to the '392 pick of the Brieloff '400 camera when it in 1975 formally disclaimed claims 5-10, which arguably "were not patentable over Brieloff" because they did not include spreading. But the disclaimer of one claim does not admit the invalidity of other claims. 35 U.S.C. § 253, Champion Spark Plug Co. v. Gyromat Corp., 603 F.2d 361, 364 (2d Cir.1979), cert denied, 445 U.S. 916, 100 S. Ct. 1276, 63 L. Ed. 2d 600 (1980); United Chromium v. International Silver Co., 60 F.2d 913, 914-5 (2d Cir.1932), cert. denied, 288 U.S. 600, 53 S. Ct. 319, 77 L. Ed. 976 (1933). Moreover, the differences between the Brieloff '400 and the remaining claims of the '392 patent are, as noted, significant.
The Fish '606 camera is somewhat more suggestive of the '392 invention than is Brieloff. It, too, uses a stack of photosensitive postcards. However, instead of a moving plate with shoulder, the Fish camera employs two manually operated lugs or tongues that press against the top edge of the exposed card and move it out of the card holder into the developing tank. Although they, like the Brieloff '400 shoulder and the '392 rear pick, operate against the edge of the film card, I find that the '606 Fish patent does not teach the invention of '392. A postcard is not a thin, flexible film unit, and the disclosure of a mechanism to push a card does not teach the possibility of pushing a flexible unit. I credit the testimony of Dr. Land that the arrangement of the tongues would operate to scratch the photosensitive surface of the next postcard to be exposeda significant problem, given that the tongues move along the entire length of the underlying card. The parallel tongues also do not teach the feasibility of a single pick. Like the Brieloff camera, the Fish camera contains no spread rollers, and it cannot perform their functions. The postcard holder of Fish is also, like that of Brieloff, wholly unsuited to receiving the rear pick of '392.
Finally, Kodak cites three I.B.M. patents in what it calls the "analogous" art of card feeding. These patents relate to large, stationary data handling machines. The card *867 feeders use a pair of rapidly reciprocating knives to drive a succession of I.B.M. cards from the bottom of a stack of cards fed by gravity. The technology of moving these cards is not the same as that of moving a film unit. The evidence showed that the I.B.M. devices depend on the inertia of the stack and the high speed of the knives to advance one card at a time. That being so, they are not adaptable to operation at the far slower rate required to move film, and they, therefore, do not teach a camera designer how to advance film. They are not relevant prior art.
Kodak next cites a number of commercial cameras. Each of them, Kodak asserts, has a rear pick which moves film in the camera by pushing it at a trailing edge. They in fact do no such thing. All but one of these cameras, the Speed-O-Matic, use conventional roll film with sprocket holes. The film is advanced by a claw or claws that enter the holes along the edge or edges of the film and pull it into the next position. None uses stacked film units stored in cassettes. None moves one frame at a time. [33] None performs spreading and processing functions, and in none is the claw part of an intricate and integrated unit of camera, cassette and film.
The Speed-O-Matic uses a cardboard holder into which are placed back-to-back two pieces of film with their photosensitive side pointed outward. The holder is put into the camera so that a hole in the holder fits over a claw built into the camera. The claw moves the film into and out of the envelope. After the first exposure the envelope is removed from the camera and turned around to start the process anew. This arrangement, like that of the other cameras, does not perform the functions required of the '392 rear pick. It does not teach the invention of the '392 patent.
As noted earlier, the essence of the '392 invention is the rear pickits placement and manner of engaging and advancing the film unit. The invention must, however, be viewed in the context of the entire film transport arrangement and the demands of an instant camera. So viewed, the invention is not obvious. The differences between the prior art and the invention are important: none of the prior art patents or cameras had to solve the practical problems of a camera that not only stores and exposes film, but also processes it. Even Kodak's expert, Mr. Kaprelian, called the SX-70, which incorporates the '392 invention, "most innovative."
Kodak next argues that the patent is unenforceable because Polaroid failed to cite to the Examiner the most pertinent prior art, namely, the scanning camera patents, Land '452 and Wareham '370, and the street vendor camera patent, Brieloff '400. First, all of these patents were in the class of art searched by the Examiner and are, therefore, deemed to have been considered and discarded. E.I. DuPont de Nemours v. Berkley & Co., Inc., 620 F.2d 1247, 1267 (8th Cir.1980); International Telephone & Telegraph v. Raychem Corp., 188 U.S.P.Q. 214, 219 (D.Mass.1975), aff'd, 538 F.2d 453 (1st Cir.), cert. denied, 429 U.S. 886, 97 S. Ct. 238, 50 L.Ed.2d. 167 (1976). Second, having considered the prior art, I find that these three patents are not, in fact, more pertinent than those expressly brought to the Examiner's attention.
Kodak denies infringement only of claims 3, 4 and 12. It seeks to avoid infringement of claims 3 and 4 by suggesting that the path of the EK-6 pick does not fit the requirement of "reciprocating movement." As to claim 12, it asserts that in the operating sequence of the EK-6 no "predetermined period of time" elapses "from termination of exposure" to the engagement of the film unit by the pick as called for by that claim.
The argument with respect to claims 3 and 4 depends on an interpretation of "reciprocating movement" to mean "back and forth in a straight path." Because the path of the EK-6 pick is more or less "D" *868 shaped, it is said not to reciprocate. Kodak does not cite any authority for the proposition that reciprocating movement means only back and forth movement, and I do not read the words of the patent to confine the pick to a straight path. Accordingly, I find those claims infringed.
With the EK-6 the photographer must not only depress but also release the shutter button to start the motor and the consequent film advance. Because the photographer might theoretically keep the button depressed indefinitely, Kodak asserts that the element in claim 12 of "a predetermined period of time since termination of exposure" is missing and that the claim is therefore not infringed. Polaroid argues that the predetermined period of time means a time long enough to prevent blurring of the image by advancement before exposure is complete and that Kodak cameras undoubtedly have a similar safeguard built in. The difficulty with Polaroid's argument is that claim 12 does not further define the period of time and no evidence was offered as to any such safe time in the EK-6. Accordingly, I find claim 12 not infringed.
For the reasons stated, I find that the asserted claims of the '392 patent are valid and that the EK-6 camera infringes claims 1, 2, 3 and 4. Claim 12 is not infringed.
During the development work of the SX-70 system one of the problems that emerged and required solution was the phenomenon known as light-piping. The archetypical integral film unit has at least one transparent support through which the film is exposed. In such a film unit the photosensitive layers are shielded from light during development, on one side by an opaque support or by preformed opaque layers, and on the other by the inclusion in the processing composition of an opacifying substance. This substance is spread across the photosensitive surface of the film unit as the film travels through the spread rollers. When the film unit emerges from the camera, light rays hitting the transparent support are able to travel, or "pipe," through the length of that support and past the spread rollers to the portions of the film not yet treated with processing composition and therefore not yet shielded from light by the opacifying substance contained therein. Such light rays cause fogging, i.e., further exposure, where they strike the untreated portion of the film unit.
One well-known solution to the problem of light-piping was the to incorporate into the support an opacifying pigment in a quantity sufficient to offer some resistance to the light rays traveling through it. Another solution considered by Polaroid researchers, including Mr. Wareham, one of the inventors of the patent in suit, was to shield the film unit from ambient light until all or nearly all of it had passed the spread rollers. As possible shielding mechanisms, they discussed a dark curtain, a black retractable shade, and some sort of shroud or "imbibing lip." In the fall of 1971, Messrs. Wareham and Paglia, another Polaroid engineer, proposed a structural addition to what became the SX-70 camera, namely, a triangular light-shielded chamber through which the film unit had to travel before exiting the camera. One side of the triangle was formed by the wall of the camera that included the spread rollers. The second side, perpendicular to the first, was formed by a hinged extension of the back housing of the camera. The third side, the hypotenuse of the triangle, extended from the outer end of the back housing extension to the housing for the lens-shutter assembly which is attached to the first side. The addition was so constructed that it did not add to the size of the camera; when the camera was collapsed, the light shield folded into it. It was of such a size, however, that the film when exiting the spread rollers hit the hypotenuse and then was deflected by it toward an exit door between the end of the back housing extension and the lower end of the hypotenuse.
The triangular, folding structure was a more elegant solution than the shroud or dark sheets earlier discussed, but it required *869 bending the film unit to provide a sufficiently long path within the light-protected environment to reduce light piping to tolerable levels. This bending was contrary to Polaroid's long-held belief that proper spreading of the processing composition could be achieved only if the film were maintained in one plane. Surprisingly, bending not only failed adversely to affect spreading, it improved it in one important respect.
Ideally, the pod of an integral film unit contains exactly enough processing liquidno more and no lessfully to cover the photosensitive area at the correct thickness. Too little liquid means that the image will not be fully developed; too much is expensive, and it presents the problem of storing the excess. The ideal, however, is difficult to achieve in practice. The fluid does not maintain a straight front as it is pushed by the spread rollers; it takes the shape of a tongue. The center of the advancing fluid tends to move ahead of the edges in a shape similar to that assumed by even an initially square piece of dough when it is rolled. This phenomenon was also well known. Since it required additional processing composition to ensure complete coverage, considerable effort had been expended at both Polaroid and Kodak to achieve a flattening of the meniscus. [34] Researchers at both corporations worked with the design of the cassette and the camera, as well as the film. Unexpectedly, bending the film unit to accommodate to the light-shield structure turned out to assist materially in the spread control process.
U.S. Patent No. 3,810,211, which issued on May 7, 1974, on an application filed on April 24, 1972, discloses both the light-piping and spread control solutions to be gained from the claimed light-shield structure.
The specifications describe and illustrate a compact collapsible camera specifically including an "opaque light-shielding platelike member." They further detail the path of the film unit within this structure; it moves straight out of the spread rollers until it reaches the light shield whence it is deflected downward, and parallel to the light shield, to the exit at the bottom of the camera. The dimensions of the structure are such that when the leading edge of the film unit emerges into ambient light, a second portion, already spread with developer fluid, is between the exit and the front of the spread rollers but protected from light by the shield. A third portion, which has not yet been processed, is still behind the spread rollers. When the entire film unit has passed the rollers, the trap end is caught by the specially designed exit slot to prevent the photograph from falling to the ground.
The patent teaches that deflection of the film increases its path within the light-protected structure and thereby alleviates the problem of light piping. It also teaches that, given the relative stiffness of the film unit, deflection in front of the spread rollers causes the portion behind the spread rollers to be pushed up against the roof of the cassette. The result of that upward push is a thinning of the layer of developer fluid and an improvement in the contour of the fluid meniscus. The patent refers to, and indeed illustrates, other spread control devices and notes that the light-shield deflector enhances their utility in squaring the mass of fluid. This effect may best be understood by regarding the portion of the film remaining to be spread as a container. Pushing it up against the roof of the cassette or against any spread control projections shortens the container and thereby prevents the fluid from assuming an elongated shape.
Polaroid accuses Kodak's EK-4 and EK-6 cameras of infringing claims 8, 9 and 10 of the '211 patent. Claim 8 calls for a camera with a means for receiving, exposing, and processing a film unit described in the specifications as an integral film unit. It further calls for a "means for deflecting" the exposed film unit from the path it *870 would normally follow out of the spread rollers (the light-shield deflector), and it specifies that as the film is progressively advanced there is a portion outside the camera which has been spread, a second portion, also spread, between the rollers and the exit, and a third portion, as yet untreated, behind the rollers. Claims 9 and 10 depend on claim 8. Claim 9 describes the light-shield housing as forming part of the camera back and defines the exit path of the film unit as substantially parallel to the housing member. Claim 10 calls for the camera exit to grip the film unit as it passes through.
Kodak denies infringement and asserts the invalidity of the claims on grounds of anticipation and obviousness. It also argues that the claims adequately describe the invention and do not therefore satisfy the requirements of section 112.
Kodak's anticipation and obviousness arguments are based on a reading of the claims of '211 without any reference whatever to the specifications. Kodak is, of course, correct in its statement that an invention is limited to that which is claimed and that the specifications cannot be used to expand the patent monopoly, United States v. Adams, 383 U.S. 39 , 49, 86 S. Ct. 708, 713, 15 L. Ed. 2d 572 (1966) but "it is fundamental that claims are to be construed in the light of the specifications and both are to be read with a view to ascertaining the invention"; Burns v. Meyer, 10 Otto 671, 672, 100 U.S. 671 , 672, 25 L. Ed. 733 (1880); Ziegler v. Phillips Petroleum Co., 483 F.2d 858, 868 (5th Cir.1973), cert. denied, 414 U.S. 1079, 94 S. Ct. 597, 38 L. Ed. 2d 485 (1973). The claims asserted here describe a structure of defined dimensions and characteristics, as well as the change worked by that structure on the normal path traveled by the film unit out of the rollers and camera. The specifications explain the effect of the changed path of travel. Without consideration of an invention's object and beneficial result, the novelty of most inventions would often be elusive. Accordingly, I consider the prior art not simply as it describes particular camera structures but also as those structures affect the film unit.
Kodak cites five prior art patents and Polaroid's experimental U-5 camera as disclosing all of the elements of the asserted claims or their equivalents.
U.S. Patent No. 3,405,619 to Land describes a self-developing scanning camera. It is in fact constructed in such a manner that the film unit exits the camera through a curved passage necessitated by the particular placement of the motor. Although in this camera the film unit may in the course of its travel be literally partly outside the camera, partly in the passage, and partly behind the spread rollers, the '619 patent does not anticipate the asserted claims of '211. [35] First, the curved passage is not intended to be a light-shielding mechanism, nor does the patent disclose that it functions as such. Second, although the film is bent through the curved passage, the patent teaches nothing about bending and how bending improves spreading. Finally, the '619 camera is designed for use with peel-apart film which, by definition, does not present the same light-piping problems as does integral film. This patent was, moreover, in the class of art searched by the examiner during the prosecution of the '211 patent. E.I. DuPont de Nemours v. Berkley & Co., Inc., 620 F.2d 1247, 1267 (8th Cir.1980); International Telephone & Telegraph v. Raychem Corp., 188 U.S.P.Q. 214, 219, aff'd, 538 F.2d 453 (1st Cir.), cert. denied, 429 U.S. 886, 97 S. Ct. 238, 50 L. Ed. 2d 167 (1976).
Kodak argues that claims 8-10 are also anticipated by U.S. Patent No. 3,350,991 to Murphy. This patent is directed to the design of the film exit for a camera that uses peel-apart film. Kodak concedes that nothing in '991 teaches deflection of the film unit. On the contrary, the camera of '991 is designed to permit withdrawal of *871 the film in a straight line. Although like the '619 patent, this patent literally reads on some of the elements of the asserted claims, also like the '619 patent, it does not disclose the invention of '211. With respect to the '991 patent, Kodak also argues that the accused cameras are like that disclosed in '991 because in both the film exit is in line with the path normally followed by the film, and if the asserted claims can be said to read on the Kodak cameras they are invalid under '991. The difficulty with the argument is that the film exit of the accused cameras is not, in fact, in line with the film's normal path.
Three additional patents [36] are said to anticipate the claims asserted. All were before the Patent Office during the prosecution of '211. These patents disclose cameras adapted for use with integral film units. In each the spread rollers are located a short distance from the exit slot and in each the exit slot includes flexible lips that serve as a light seal and are arranged to exert a gripping force on the film unit. However, in none of these cameras is there a "means for deflecting [the] exposed film unit from the path it would normally follow...." These patents do not disclose all of the elements of claims 8-10. They say nothing about light piping or bending. On the contrary, they reflect the view of Polaroid until the discovery of the '211 patent that a film unit should not be bent. These patents do not anticipate the claims of '211.
In the course of the development of the SX-70 system, Polaroid built a number of camera models, including the U-5. The U-5 was at one point modified with an opaque deflector plate. Kodak asserts that this model shows every element of the claims asserted or their equivalent. The U-5, however, is not prior art, both because it was an internal experimental model, Del Mar Engineering Laboratories v. United States, 524 F.2d 1178, 1182, 207 Ct.Cl. 815 (1975), and because the structure upon which Kodak relies was built after the filing date of the patent in suit.
In support of its assertion of invalidity under section 103, Kodak relies on the same prior art patents discussed above plus two additional patents, Whall U.S. Patent No. 3,650,188 and Whall German Patent No. 2,009,384, and the prior knowledge of light-shielding within Polaroid.
The parties do not disagree that the relevant art is that of camera design and that a person of ordinary skill in the art is one holding at least a Bachelor's degree in mechanical engineering with a number of years experience in the field.
Unquestionably the prior art taught that one solution to the problem of light-piping is to provide a light free environment until the entire film unit is coated. Polaroid does not dispute that several of its camera designers knew that and had, in fact, experimented with a variety of light-shielding mechanisms, as described earlier herein. Moreover, the structures of all the prior art patents cited by Kodak and discussed above [37] do teach the feasibility of positioning an exit slot at some distance from the spread rollers. Although none specifically addresses the problem of light-piping, and, indeed, none suggests the use of that intermediate space for light shielding purposes, I find that an experienced camera designer would be able to adapt those cameras to provide the requisite protection from ambient light. However, none of these patents teaches the addition of a light shield particularly designed to bend the film unit. [38] Nothing in the experimental work at Polaroid suggested the feasibility, much less the utility, of bending the film.
Several of the patents, '991, '770, '437 and '357, do disclose exit slots defined by flexible lips or a spring arrangement. The *872 similarities between those devices and that described in claim 10 of the '211 patent are such that the gripping of claim 10 would clearly be obvious to a skilled camera designer. The addition of such gripping in claim 10 to the camera of claim 8 is accordingly invalid.
The additional patents cited to support the argument that the '211 is obvious, U.S. Patent No. 3,650,188 to Whall and its German counterpart, 2,009,384, disclose designs for a detachable imbibition chamber, a light-tight container which holds the instant film while it develops. As shown in the patents, the imbibition chamber may be a triangular structure into which the film is fed directly from the spread rollers. This is another patent that clearly teaches the use of a light-free environment; but since the film is fully developed before it exits the camera, the patent says nothing specifically to the problem of light piping. Moreover, in view of the size and conformation of the structure, the film is not bent at any time in its progress into or out of the chamber. Nor does the patent teach anything about spread control. The German patent discloses an alternative chamber with a transparent wall but only for storage purposes. As such, it does not render obvious '211.
Finally, Kodak argues that a thinning of the developer layer thickness is the only effect of deflection on spreading disclosed by '211. That consequence of bending was, according to Kodak, well known in view of Land U.S. Patent No. 2,495,111, Hamilton U.S. Patent No. 3,165,040, and Wills U.S. Patent No. 3,249,036. The first of these, the '111 patent, describes several mechanisms besides spread rollers for breaking pods. At least two involve a tortuous passage, something akin to a slalom course. As the film unit is pulled through the passage or the rods that form the slalom course, the pod is broken and the developer fluid spread. Although the patent describes a means of spreading by bending the film unit back and forth through obstacles, it says nothing about the effect of such bending on the shape of the meniscus or on the thickness of the developer layer. The '040 and '036 patents have to do with the design of film exit doors for peel-apart film and are used in Polaroid's Model 100 camera. Both teach that the film should be pulled out straight to avoid an adverse effect on spreading, and the exits are designed to ensure straight pulling. I am not persuaded that '211 is obvious in light of these additional references and conclude that the requisite invention is present in this patent.
Kodak attacks the validity of '211 on two additional grounds. The '211 specifications discuss the effect of bending the film unit on both the thickness of the developer layer and the shape of the meniscus. They also discuss the utility of bending in conjunction with other spread control devices. The evidence supports Kodak's contention that Polaroid knew that bending tended to thin the developer layer. The evidence does not, however, support Kodak's conclusion therefrom that Polaroid knew that thinning the developer layer improved spread shape. Nor does it support Kodak's assertion that spread shape is improved not by bending but by the inclusion in the film cassette of "shapers." As described earlier, the result of deflecting the film is to change the shape of the film as container and thus to prevent formation of the tongue. The prescription of bending to achieve a squared fluid mass went against all known principles. That bending will also affect development layer thickness and that it may be used in conjunction with other methods does not undercut the invention.
One of the drawings of the patent indicates an angle between the camera back housing extension and the light shield of 38°/30'. The claims do not define the angle. Kodak argues that that lack of specificity in the claims renders them invalid under section 12 because the angle is critical. The evidence showed, however, that the beneficial effects of bending may be achieved at angles other than that shown in the drawing. In fact, Kodak's 15° angle so proves. Accordingly, the claims do not fail to disclose an element that is critical within *873 the meaning of the patent law. See e.g. Scandiamant Aktiebolag v. Commissioner of Patents, 509 F.2d 463, 469-71 (D.C. Cir.1974).
The parties agree that for the purpose of determining infringement, the structures of the EK-4 and EK-6 cameras are identical. Kodak denies infringement on the grounds (1) that the accused cameras do not come within the literal terms of the asserted claims; [39] (2) that the angle of deflection in the accused cameras is different from that specified in '211; and (3) that the accused cameras achieve spread control by means other than deflection of the film unit.
Kodak does not contest that the EK-4 and EK-6 cameras meet all elements of claim 8 except the requirements that the exit means be disposed out of the normal path of the film unit and that there be a means of deflecting the film unit out of its normal path and toward the exit slot. It denies meeting these requirements by defining the accused cameras without reference to one of their parts, an exit spring. Without the spring, the exit is in line with the spread rollers and the film unit would not be deflected. But the spring acts as a means of deflecting the film, both narrowing the exit means and taking it out of the normal path of the film. Since the spring is part of the camera, claim 8 is infringed. [40]
Claim 9 specifically calls for the exit to be in the back of the camera and parallel to the normal film path. The arrangement of the light shield housing of EK-4 and EK-6 is in this respect totally different from the claim. Because the exit means in those cameras is not in the back, I find that claim 9 is not infringed.
If claim 10 were valid, it would be infringed by the gripping action of the exit spring.
Infringement is not avoided by reference to the angle of deflection. The claims do not require a particular angle and, as noted earlier, the precise angle is not critical to achieving the benefits of the patent.
Nor can Kodak avoid infringement by suggesting that it is not the camera structure that brings about spread control. It cannot both argue for a narrow construction of the claims and deny infringement based on an expansive reading thereof.
In summary, I find claims 8 and 9 valid and enforceable. The addition of the gripping mechanism of claim 10 is invalid for obviousness. Claim 8 is infringed by the EK-4 and EK-6 cameras, and if it were valid, claim 10 would be infringed as well. The accused cameras do not infringe claim 9.
During the development of the SX-70 camera Polaroid experimented with several film-loading designs and ultimately settled on a front-loading mechanism. The housing that contains the spread rollers pivots from its closed position to permit insertion of the film pack. Richard Paglia, a Polaroid engineer, was then assigned the task of devising a spread system for a front-loading motorized folding camera. At that time Polaroid had been experiencing leakage of developer fluid from the pod which necessitated periodic cleaning of the spread system. Because cleaning is simpler if the spread rollers are detached, Mr. Paglia designed the mechanism connecting the spread roller housing to the camera housing so that the former could not only *874 be pivoted open to permit film loading, but also separated entirely from the camera housing. This detachable spread roller housing arrangement is the subject of U.S. Patent No. 3,810,220.
As described in the drawings and specifications, the spread roller housing is attached to the rest of the camera by means of two relatively flexible arms which extend from within the housing. Each has a depression or, preferably, an aperture that fits over inwardly-facing projections on the camera housing. The apertures and projections form a hinge and are designed to permit the spread roller housing to rotate out of or into the closed position. By pressing the arms toward each other, it is also possible to disengage the apertures from the projections and thus to detach the spread roller housing from the camera. The patent points out that the ability to remove the housing facilitates maintenance and/or replacement of its components. Because precise alignment between the spread rollers, the film cassette, and the path of the individual film unit out of the camera is essential for proper spreading, it had been thought best to secure the spread roller housing permanently. "Permanent" in this context meant secured with screws or rivets. Although the housing so secured was still detachableit could be detached with toolsit was not "readily detachable." The patent asserts that the '220 invention achieves both maintenance of precise alignment and separability of the housing. The particular arrangement is said to be advantageous in that placement of the arms and projections inside the camera prevents accidental detachment and results in a neat and clean appearance of the camera when closed. At the same time, the separability feature is not apparent to an uninformed user, giving the manufacturer the option of telling customers to remove the housing for cleaning or, if customer servicing is unnecessary, withholding such information.
Polaroid asserts infringement by Kodak's EK-4 and EK-6 cameras of claims 1, 2, 3, 4, 5 and 8.
Claims 1, 3 and 5, the independent claims, each describe a self-developing camera. Each calls for an opening in the camera (the "first housing section") into which the film cassette is inserted, and a "second housing section" containing a spread system ("processing means") that extends "forwardly" and across the opening. Each calls for a means for coupling the second housing section to the first in a manner that permits pivoting the second into open and closed positions, and each requires that the coupling mechanism include "manually actuable means for readily disconnecting said second housing section from and connecting it to said first housing section." Claim 1 also requires that the second housing be detachable only in the open, the film-loading position, and claim 2 defines the processing means in that second housing as a pair of rollers. Claim 3 requires that the gear train (the "drive means") extend into the spread roller housing and that it be rendered inoperative when that housing is disconnected from the first housing. Claim 4 calls for the obverse, that the drive means be operative when the two housing sections are in the closed position. Claim 5 adds the description of the system of inwardly facing arms and projections that couple the two housings, and claim 8 requires that the arms include "at least one aperture."
Kodak's defense is premised primarily on invalidity of the patent under 35 U.S.C. § 103. It also denies infringement.
The parties agree that the relevant art is the art of camera design and that a person skilled in that art is someone with an Associate or Bachelor's degree in mechanical engineering and approximately four years experience. The prior art cited by Kodak includes both patents and a number of commercial cameras, as well as Polaroid experimental models.
Before considering Kodak's prior art references, it is useful to understand Polaroid's assertions concerning the scope of the invention. Milton S. Dietz, a Senior Vice President at Polaroid, and its expert witness on this patent, agreed that in August *875 1970: (a) a self-developing camera with a body (first housing) and a spread roller housing (second housing) hinged together was not new; (b) that the use of motors and gears to drive spread rollers and the use of a gear at the end of a spread roller was old; and (c) that it would have been obvious to one skilled in the art to use an easily detachable housing on a roll film camera and on a self-developing camera using peel-apart film. Nevertheless, Polaroid argues that the patent in issue discloses a genuine improvement over the prior art because (a) the use of a detachable spread roller housing in an integral camera is not obvious given the concern about precise alignment; (b) nothing in the prior art teaches the desirability of separability; and (c) the type of hinge used (flexible arms and projections) would have been thought to be inadequate in an integral camera, making the use of such an uncomplicated arrangement not obvious.
Kodak offered at least seven commercial cameras, including three produced by Polaroid, [41] having disconnectable backs or film-loading doors. All but one have a hinge arrangement comprised of projections on one housing and holes that fit them in the other. Several include flexible arms or levers that permit disengagement of the holes and projections and consequent separation of the camera from its door or back. Polaroid argues that none uses the precise hinge arrangement disclosed in the '220 patent and none was designed for use in an integral camera. Polaroid is correct that the hinges of the prior art references differ in various details from each other and from that described in the patent in suit. I find, however, that the earlier cameras do teach the efficacy of the '220 type of hinge and their use in cameras, i.e., an arrangement comprised of matched holes and projections, one of which is placed on a pair of flexible arms. I further find that the use of such a hinge to permit removal of the film-loading door was well known and its use to disconnect the spread roller housing would be obvious to a person skilled in the art.
The question remains whether the use of such a hinge in an integral camera would be obvious and, related thereto, whether the use of a detachable spread roller housing in an integral camera amounts to invention. Because an integral film unit, by definition, remains whole before, during, and after processing, and nothing is peeled away, the amount of processing composition in the pod must be precisely measured to be just sufficient to cover the exposed area of the film unit. Because there is only just the right amount of processing composition, the manner of spreading is crucial, and precision in spreading depends in large part on the physical arrangement of the spread system. Hence, Polaroid argues that any tampering with that arrangement by, for example, removing the spread rollers would be contraindicated, and the use of the very simple, uncomplicated '220 hinge would not be obvious. The evidence showed, however, that all of the hinge componentsthe projections and arms with aperturesare permanently affixed to the respective housings. They cannot be moved from their original positions without force and consequent damage to the camera. I am not persuaded, therefore, that a detachable spread roller housing represents a greater threat to the integrity of the spread system and the alignment of its several parts than does one that merely pivots open and closed. Whether the housing is opened to admit film, or whether it is entirely removed, the spread rollers are pulled out of alignment with the normal film path. Given the fixed positions of the arms, apertures, and projections that constitute the hinge, no significant difference exists between merely pivoting, on one hand, and, on the other hand, pivoting, detaching and reattaching the housing. The additional demands of an integral camera may render unobvious the employment of some otherwise old mechanisms. ( See discussion re '392 patent.) But they do not *876 elevate to the level of invention the arrangement of the '220 patent.
Having determined that the use of detachable film doors and backs was well known in the art, as were hinges constructed of matched apertures and projections, for the reasons stated, I further find that the use of such hinges and detachable doors is obvious even in integral cameras. [42] Accordingly, the patent is invalid under 35 U.S.C. § 103.
If the '220 patent were held to be valid, I find that all claims asserted would be infringed by the EK-4 and EK-6 cameras. Kodak's essential argument against infringement is that the housing of the accused cameras is not "readily" detached. In support of the argument, it points to the difficulties the Court encountered during trial when it attempted the detaching maneuver. But, in the first place, the maneuver succeeded. The housing was detached. In the second place, the word "readily" must be read in context. The patent distinguishes between a housing that is attached with screws, requiring tools for disconnection, and a housing that can be removed without tools. That Kodak's cameras may not be as easily divided as Polaroid's does not save them from infringement. I find that both accused cameras embody each element of the asserted claims and, therefore, would infringe claims 1, 2, 3, 4, 5 and 8 of the '220 patent were it held to be valid.
In summary, following are my conclusions concerning the validity and infringement of each of the patents in suit.
1. U.S. Patent No. 3,362,821, the polymeric acid patent, is valid and claim 1 is infringed.
2. U.S. Patent No. 3,245,789, the negative dye developer patent, is valid and claims 5 through 9 are infringed.
3. U.S. Patent Nos. 3,594,165 and 3,689,262, the opacifying layer patents, are valid and claims 3, 5 and 6 are infringed.
4. U.S. Patent No. 3,770,439, the mordant patent, is valid but claims 1, 7 and 8 are not infringed.
5. U.S. Patent No. 3,578,540, the symmetrical supports patent, is valid and claims 5, 6 and 8 are infringed.
6. U.S. Patent No. 3,709,122, the rear motor and gear train patent, is invalid, but if it were held to be valid, claims 1, 2, 3, 6 and 8 would be infringed.
7. U.S. Patent No. 3,753,392, the rear pick patent, is valid and claims 1, 2, 3 and 4 are infringed. Claim 12 is not infringed.
8. Claims 8 and 9 of the light shield deflector patent, U.S. Patent No. 3,810,211, are valid. Claim 10 is invalid. Claim 8 is infringed; and if it were held to be valid, claim 10 would be infringed as well. Claim 9 is not infringed.
9. U.S. Patent No. 3,810,220, the detachable spread roller housing patent, is invalid. If it were held to be valid, claims 1, 2, 3, 4, 5 and 8 would be infringed.
This Court tried the issues with respect to the validity, infringement and enforceability of ten United States patents owned by plaintiff Polaroid Corporation ("Polaroid") and the Court considered the parties' post-trial briefs and proposed findings of fact. A Memorandum of Decision was rendered by the Court on September 13, 1985, setting forth findings of fact and conclusions of law pursuant to Rule 52, Fed.R. Civ.P., with respect to these ten patents. In addition, on June 10, 1981, the Court granted summary judgment with respect to the validity of another United States patent owned by Polaroid, which was asserted in the complaint herein.
Pursuant to Rule 54(b), Fed.R.Civ.P., the Court determines that there is no just reason for delaying the entry of judgment on the issues decided with respect to these *877 eleven patents and directs the entry of judgment as set forth below. It is hereby
ORDERED AND ADJUDGED, that
1. This Court has jurisdiction over the subject matter of this action and over the parties.
2. Plaintiff Polaroid is the owner by assignment of each of the patents set forth in paragraphs 4-14 of this judgment ("the patents in suit") and of all rights of recovery for infringement thereof.
3. Defendant Eastman Kodak Company ("Kodak") has manufactured and sold in the United States during the term of the patents in suit, without authority from Polaroid, Kodak PR-10 film and Kodak EK-4 and EK-6 cameras.
4. With respect to Land U.S. Patent No. 3,362,821, entitled "Diffusion Transfer Processes Utilizing Photosensitive Elements Containing Polymeric Acid Spacer Layers," issued January 9, 1968:
a. Kodak has failed to carry its burden of proving claim 1 invalid.
b. Kodak has infringed claim 1 by making, using and selling PR-10 film.
c. Kodak has failed to carry its burden of proving unenforceability.
5. With respect to Rogers U.S. Patent No. 3,245,789, entitled "Photographic Products and Processes," issued April 12, 1966:
a. Kodak has failed to carry its burden of proving claims 5, 6, 7, 8 and 9 invalid.
b. Kodak has infringed claims 5, 6, 7, 8 and 9 by making, using and selling PR-10 film.
6. With respect to Rogers U.S. Patent No. 3,594,165, entitled "Novel Photographic Products and Processes," issued July 20, 1971:
a. Kodak has failed to carry its burden of proving claims 3, 5 and 6 invalid.
b. Kodak has infringed claims 3, 5 and 6 by making, using and selling PR-10 film.
7. With respect to Rogers U.S. Patent No. 3,689,262, entitled "Photographic Products and Processes for Color Diffusion Transfer," issued September 6, 1972:
8. With respect to Taylor U.S. Patent No. 3,770,439, entitled "Polymeric Mordant in Color Diffusion Transfer Image-Receiving Layer," issued November 6, 1973:
a. Kodak has failed to carry its burden of proving claims 1, 7 and 8 invalid.
b. Kodak has not infringed claims 1, 7 and 8.
9. With respect to Land U.S. Patent No. 3,578,540, entitled "Color Photographic Product Formed by Diffusion Transfer," issued May 11, 1971:
a. Kodak has failed to carry its burden of proving claims 5, 6 and 8 invalid.
b. Kodak has infringed claims 5, 6 and 8 by making, using and selling PR-10 film.
10. With respect to Blinow and Leduc U.S. Patent No. 3,709,122, entitled "Film-Advancing Apparatus," issued January 9, 1973:
a. Claims 1, 2, 3, 6 and 8 are invalid.
b. If the claims were valid, Kodak would have infringed claims 1, 2, 3, 6 and 8 by making, using and selling EK-6 cameras.
11. With respect to Land U.S. Patent No. 3,753,392, entitled "Film-Advancing Apparatus," issued August 21, 1973:
a. Kodak has failed to carry its burden of proving claims 1, 2, 3, 4 and 12 invalid.
b. Kodak has infringed claims 1, 2, 3 and 4 by making, using and selling EK-6 cameras and PR-10 film.
c. Kodak has not infringed claim 12.
d. Kodak has failed to carry its burden of proving unenforceability.
*878 12. With respect to Wareham and Paglia U.S. Patent No. 3,810,211, entitled "Self-Developing Camera System," issued May 7, 1974:
a. Kodak has failed to carry its burden of proving claims 8 and 9 invalid.
b. Claim 10 is invalid.
c. Kodak has infringed claim 8 by making, using and selling EK-4 and EK-6 cameras.
d. Kodak has not infringed claim 9.
e. If the claim were valid, Kodak would have infringed claim 10 by making, using and selling EK-4 and EK-6 cameras.
f. Kodak has failed to carry its burden of proving unenforceability.
13. With respect to Paglia U.S. Patent No. 3,810,220, entitled "Detachable Spread Roller Housing Section," issued May 7, 1974:
a. Claims 1, 2, 3, 4, 5 and 8 are invalid.
b. If the claims were valid, Kodak would have infringed claims 1, 2, 3, 4, 5 and 8 by making, using and selling EK-4 and EK-6 cameras.
14. With respect to Campbell U.S. Patent No. 3,761,269, entitled "Self-Developing Photographic Film Unit with Liquid Trap and an Alkali Neutralizing Spacer Element," issued September 25, 1973, claims 1 through 9 are invalid.
15. Effective January 9, 1986, Kodak, its officers, agents, servants, employees, and attorneys, and those persons in active concert or participation with them who receive actual notice of this judgment by personal service or otherwise, are enjoined and restrained from infringing any one or more of the following:
a. Claims 5, 6 and 8 of Land U.S. Patent No. 3,578,540;
b. Claims 3, 5 and 6 of Rogers U.S. Patent No. 3,594,165;
c. Claims 3, 5 and 6 of Rogers U.S. Patent No. 3,689,262;
d. Claims 1, 2, 3 and 4 of Land U.S. Patent No. 3,753,392;
e. Claim 8 of Wareham and Paglia U.S. Patent No. 3,810,211;
including, without limitation, by manufacture, use or sale of PR-10 film and EK-4 and EK-6 cameras.
16. The cause shall be set for determination of the following issues in a subsequent trial to be held by the Court:
a. Whether Kodak's infringement of any one or more of the patents in suit has been willful and deliberate.
b. The amount of damages adequate to compensate Polaroid for Kodak's infringement together with interest and whether such damages should be increased up to three times the amount found, all in accordance with 35 U.S.C. § 284.
c. Whether costs shall be taxed against either party.
d. Whether Polaroid is entitled to its reasonable attorney's fees because this is an "exceptional case" within the meaning of 35 U.S.C. § 285, and if so, the quantum of those fees.
[1] U.S. Patent Nos. 3,362,821; 2,245,789; 3,594,165; 3,689,262; 3,578,540; 3,709,122; 3,753,392; 3,810,211; 3,810,220; and 3,770,439.
[2] Both parties have claimed attorneys' fees pursuant to 35 U.S.C. § 285; Polaroid, charging willful and deliberate infringement, also seeks increased damages under § 284. These issues were reserved to a post-liability phase of the trial and I accordingly do not address them in this memorandum.
[3] Although ten patents are in issue, two, Patents No. 3,594,165 and No. 3,689,262, are substantially identical, reducing the number of disputes to nine.
[4] The researchers at Polaroid did not pursue Dr. Vittum's suggestion because sulfostearic acid does not satisfy prerequisites for stabilization of a color diffusion transfer system. It is not a high polymer, it does not have a delay mechanism, and it is a strong acid that might affect the mordants.
[5] See part V for definitions of terms used herein.
[6] The Section 282 Notice listed a number of prior art references and Kodak offered evidence as to all. U.S. Patent No. 2,584,030; French Patent No. 1,293,709, and corresponding abandoned U.S. Application Serial No. 29,075; U.S. Patent No. 2,923,623; Australian Patent No. 231,185, and its equivalent British Patent No. 804,971.
[7] The reference here is to abandoned U.S. Application Serial No. 29,075 which the parties agree corresponds to the French '709 patent.
[8] I use a word," Humpty Dumpty said, ... "it means just what I choose it to mean neither more nor less."
"The question is," said Alice, "whether you can make words mean so many different things."
"The question is," said Humpty Dumpty, "which is to be masterthat's all."
L. Carroll, Alice's Adventures in Wonderland & Through the Looking-Glass, New York: Signet, Signet Classics by The New American Library, Inc., 1960, p. 186.
[9] One of the issues concerning both validity and infringement of the patent in suit is the precise function of the developer. Mr. Rogers testified that the term refers to compounds that have the ability either to develop the silver halide directly or to act as messenger of electronsto have the "redox potential" necessary to be a developing agent. I accept that testimony and that definition.
[10] Although I have referred to the photosensitive element and dye developer layer in the singular, a film unit used in instant photography consists of a multiplicity of very thin layers, each of which performs a separate and unique function. For color photography, a separate negative and separate dye developer layer exists for each of the three subtractive colors.
[11] Fogging is the occurrence of cloudiness or partial opacity caused by chemical action or light. Antifoggants are chemicals designed to counteract this effect.
[12] Australian Specification No. 241,147, published February 12, 1959 and "accepted" October 2, 1962; abandoned U.S. Application No. 734,141, filed May 9, 1958; and Canadian Patent No. 602,607, issued August 2, 1960.
[13] Kodak reads the '789 patent by reference to the language used in the '606 patent describing the positive dye developer process. But contrary to Kodak's assertion, in neither process is it required that the dye developer in fact develop the silver halide. When auxiliary developer is used, it serves as messenger of electrons and the dye developer need not contact the silver halide. Mobility in both patents refers to the ability of the dye developer to cause transfer of image-forming compounds.
[14] Charles H. Schallhorn, a research associate at Kodak's Color Instant Laboratory conducted experiments with the Whitmore-Mader compounds in preparation for trial. He testified that oxidation and deamination occurred and that these reactions did result in the release of dye. The experiments are not, however, persuasive of the utility of the Whitmore-Mader process. In them, Mr. Schallhorn used materials not specified in the patent applications or patents and which in some instances were not even available in 1972. For example, he used a linking group and dye, sulfonate ester and a urethane linking group, because they are more stable than those used by Whitmore-Mader.
[15] The first application for what became the '165 patent was filed in May 1968. The patent issued on a later application, filed in April 1969, which was a continuation-in-part of that filed in 1968.
[16] A polymer is a very large molecule that consists of small units, linked together as in a chain. The small units, the links of the chain, are called repeating units. A polymer that consists of a series of identical repeating units is called a homopolymer; one that consists of two or more different repeating units is a copolymer. A repeating unit before polymerization is a monomer or monomeric unit.
[17] A benzene ring is a structural arrangement of six carbon atoms linked by alternate single and double bonds in a planar symmetrical hexagon.
[18] A hydrocarbon is a compound that contains at least one carbon and four hydrogen atoms, but atoms of no other type.
[19] The experiments in fact concentrated on copolymers with methyl and ethyl groups and did not include the higher groups of the lower alkyls.
[20] Kodak presented considerable evidence concerning the conventional method of indicating a copolymer, but it was inconsistent. The parties agree that the brackets surrounding the formula denote it as a repeating unit. Kodak's witnesses gave, and its own patent notation reflected, varying means of signifying that the repeating unit relates to a homopolymer or copolymer. Accordingly, I accept Dr. Taylor's interpretation of his own language.
[21] One, Compound VIII, was used as a control and performed poorly.
[22] The term "curl" refers to a uniform departure from planarity; "distortion" is a non-uniform change.
[23] The remainder of the patent details the various layers of the laminate which are not claimed to be new.
[24] These patents are cited in Kodak's section 282 notice and include U.S. Patent No. 3,059,659; Canadian Patent No. 682,226; U.S. Patent No. 3,438.775; U.S. Patent No. 3,330,655; U.S. Patent No. 3,253,915.
[25] Of course, a conventional photograph is one sheet that has been dried rapidly, and finding a means of balancing the stresses is not inordinately difficult.
[26] The samples brought by Mr. Otto prove Kodak's cautionary instructions. They are faded and stained.
[27] The precise manner in which the pick engages the film unit is described in the following discussion concerning that patent.
[28] Kodak would include in the prior art also the secret internal camera models, particularly the PT-III and U-3. While they, like the rear motor camera patents, may be evidence of the level of skill in the art, they are not prior art. Del Mar Engineering Lab. v. United States, 524 F.2d 1178, 1182, 207 Ct.Cl. 815 (1975).
[29] Insofar as the specifications describe the invention as providing a slim and compact camera, they are correct. Even if the location of the motor in the rear may have extended the length of the camera, it is slim and compact by virtue of the arrangement of the component parts. But that feature is not claimed.
[30] The specifications describe it as "a resilient arm ... [that] includes a downwardly turned film-engaging member which is adapted to engage the trailing edge of the film unit.... [This] member is configured such that its free end does not extend to a position wherein it could engage the trailing edge of more than one film unit."
[31] U.S. Patent No. 3,511,152 to Erlichman; U.S. Patent No. 3,545,357 to Erlichman, U.S. Patent No. 3,447,437 to Tiffany.
[32] U.S. Patent No. 3,505,943 to Bellows, U.S. Patent No. 1,070,400 to Brieloff, U.S. Patent No. 1,626,606 to Fish, U.S. Patent No. 3,460,452 to Land, and U.S. Patent No. 3,537,370 to Wareham, and a number of I.B.M. patents.
[33] As Dr. Land pointed out, advancing one frame of a roll of film necessarily advances all other frames on the roll.
[34] Polaroid had established its Spread-Testing Laboratory at least as early as 1969; Kodak, its Spreading and Trapping Committee no later than in 1970.
[35] It is even questionable whether the passage is equivalent to the light-shield chamber of claim 8 of the '211 patent. Mr. Kaprelian, Kodak's expert, characterized it as the "exit means" of claim 10. It cannot be both, chamber and exit means, and anticipate '211.
[36] U.S. Patent No. 3,683,770 to Land, et al., U.S. Patent No. 3,447,437 to Tiffany, and U.S. Patent No. 3,545,357 to Erlichman, et al.
[37] The '619, '991, '770, '437 and '357 patents.
[38] Even the Land '619 patent with its curved passage designed "to prevent rays of light from directly traveling in [the] path of the film assembly ..." certainly does not teach bending for control of spread shape, nor even of lightpiping in integral film units.
[39] Kodak argues in this connection that Polaroid is estopped from claiming spread control as the invention, having abandoned claims addressed thereto. Polaroid did abandon claims directed expressly to spreading. The claims ultimately approved claim deflection as the invention, and the patent describes spread control as one of the benefits derived from the invention. Contrary to Kodak's contention Polaroid alleges infringement by a literal reading of the claims' construction thereof. Its position is entirely in accord with Schriber-Schroth Co. v. Cleveland Trust Co., 311 U.S. 211 , 61 S. Ct. 235, 85 L. Ed. 132 (1940).
[40] It is for this reason as well that Kodak's argument concerning the Murphy '911 patent fails. The EK-4 and EK-6 cameras do not read on Murphy '991 because their exit is not as required by Murphy '991.
[41] Rolleicord Camera with interchangeable Rolleiken Back, Bertram Camera, Honeywell Elmo Cine Camera, Crislin Insta Camera, and Polaroid Colorpack II, Big Swinger and Little Swinger Cameras.
[42] In view of this finding, based on the prior art cameras, it is unnecessary to consider the prior art patents on which Kodak relies, U.S. Patent No. 3,643,565 to Bellows, U.S. Patent No. 3,283,682 to Rice, and U.S. Patent No. 3,650,188 to Whall.
Some case metadata and case summaries were written with the help of AI, which can produce inaccuracies. You should read the full case before relying on it for legal research purposes.
Get free summaries of new District of Massachusetts U.S. Federal District Court opinions delivered to your inbox!
- Bankruptcy Lawyers
- Business Lawyers
- Criminal Lawyers
- Employment Lawyers
- Estate Planning Lawyers
- Family Lawyers
- Personal Injury Lawyers
- Estate Planning
- Personal Injury
- Business Formation
- Business Operations
- Intellectual Property
- International Trade
- Real Estate
- Financial Aid
- Course Outlines
- Law Journals
- US Constitution
- Regulations
- Supreme Court
- Circuit Courts
- District Courts
- Dockets & Filings
- State Constitutions
- State Codes
- State Case Law
- Legal Blogs
- Business Forms
- Product Recalls
- Justia Connect Membership
- Justia Premium Placements
- Justia Elevate (SEO, Websites)
- Justia Amplify (PPC, GBP)
- Testimonials
Polaroid Wins $909 Million From Kodak : Photography: The firms have been involved in a patent-infringement suit for years. Analysts had expected the award to be much larger.
- Copy Link URL Copied!
In a huge award that nonetheless disappointed some observers, Polaroid Corp. won $909 million Friday in a long-running instant photography patent-infringement suit against rival Eastman Kodak Co.
U.S. District Judge A. David Mazzone in Boston, delivering a judgment topped only by the $10.3 billion awarded to Pennzoil Co. in a dispute against Texaco Inc. over an oil company takeover, ruled that Polaroid had lost profits of nearly $250 million because of Kodak’s illegal actions.
But the $909-million award, which also reflects interest and royalties, was far short of the $2.5 billion that some Wall Street analysts had expected, or the $5.7 billion in lost profit and interest that Polaroid had demanded in court papers it filed in February, 1988.
“Clearly this is a negative award for Polaroid,” said B. Alex Henderson, an analyst at Prudential Bache Securities in New York. “People were expecting a number much larger than that, and I would expect Polaroid (stock) to be off anything from $3 to $5 Monday morning.”
On Friday, Kodak shares were up sharply in after-hours trading following Judge Mazzone’s lower-than-expected award. In New York Stock Exchange trading, Kodak closed at $34.625, up 25 cents for the day, but rose to $38 in some off-market trading.
Polaroid shares were unchanged from the NYSE close at $29.25, down 25 cents for the day.
Polaroid declined to say whether it would appeal the ruling, announcing it “will review the decision and all relevant factors to determine what steps the company will take.”
Kodak’s chairman and chief executive officer, Kay R. Whitmore, said, “While we feel the court award is substantially more than the amount to which Polaroid is entitled, we view the court’s decision as a confirmation of our good faith in entering the instant photography business.”
The patent-infringement case began 14 years ago when Cambridge, Mass.-based Polaroid alleged that it had suffered losses of nearly $4 billion when Rochester-based Kodak infringed on Polaroid’s instant-photography patents.
Polaroid’s instant camera, which develops photographs on the spot in 60 seconds, was a technological marvel that captivated America when it first appeared on store shelves after Thanksgiving in 1948.
Polaroid alleged that Kodak illegally incorporated the technology in instant photography products it sold from 1976 until early 1986.
Polaroid sought trebled damages of $12 billion, claiming it suffered severely at Kodak’s hands through loss of market share and unfair price competition.
But Kodak said it had only cost Polaroid $343 million and termed Polaroid’s claim “excessive.”
Many experts believe that the dispute took a creative and financial toll on Polaroid, which was one of the earliest postwar high-tech pioneers in the U.S. and whose founder, Edwin H. Land, holds more patents than any inventor except Thomas Edison.
Land’s much-ballyhooed follow-up to the instant still camera--Polavision instant movies--was a flop in 1977. The $700 camera cost too much, could not record sound and only exposed 2 1/2 minutes of film per cartridge. Consumers opted for a competing invention: the videotape recorder.
Polaroid suffered another blow a few years later when the Japanese began marketing automated, fuss-free 35-m.m. cameras in the United States. That development, together with the advent of one-hour photo shops, rendered instant still cameras virtually obsolete.
The company’s instant camera sales--and profit--plunged.
More to Read
Column: OpenAI just scored a huge victory in a copyright case ... or did it?
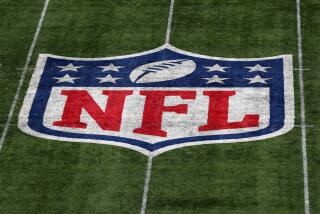

Federal judge overturns $4.7-billion verdict in ‘NFL Sunday Ticket’ lawsuit
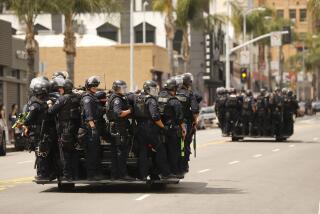
Jury awards $3.75 million to protester hit by hard-foam police projectiles
Inside the business of entertainment
The Wide Shot brings you news, analysis and insights on everything from streaming wars to production — and what it all means for the future.
You may occasionally receive promotional content from the Los Angeles Times.
More From the Los Angeles Times
Workers at a Las Vegas casino are on strike. Here’s what to know
World & Nation
He’ll be the last meatpacker in NYC’s Meatpacking District
Losses for Big Tech pull U.S. stock indexes lower
Bond trader at Pasadena firm shunted $600 million to favored portfolios, U.S. claims
Most read in business.
Glendale’s blue-collar tech unicorn ServiceTitan files for IPO
Toys, car parts and avocados: How Trump’s proposed tariffs could impact your wallet
- Case Studies
Strategy & Execution
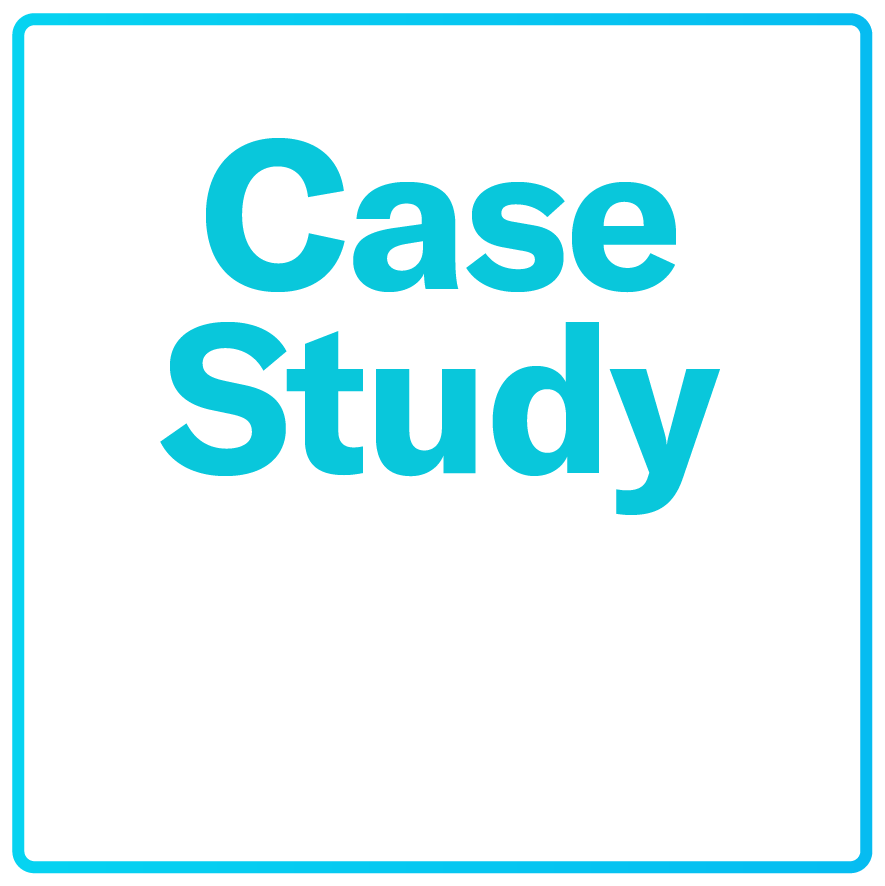
Polaroid-Kodak
Write a review, are you an educator.
Register as a Premium Educator at hbsp.harvard.edu , plan a course, and save your students up to 50% with your academic discount.
Product Description
Publication Date: June 01, 1976
Industry: Retail and consumer goods
Source: Harvard Business School
Describes Kodak's long-awaited challenge to Polaroid in the field of instant photography. Provides technological and company background of both Polaroid and Eastman-Kodak and their respective product lines. Discusses Polaroid's claim that Kodak infringed on 10 Polaroid patents.

This Product Also Appears In
Related products.
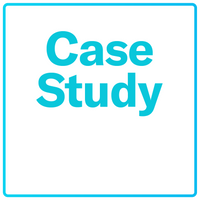
Polaroid-Kodak (B6)
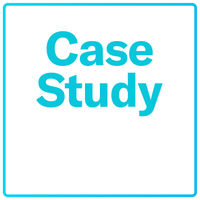
Polaroid-Kodak, (B11)
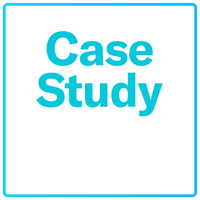
Polaroid-Kodak, (B10)
Copyright permissions.
To obtain copyright permission to share this PDF with your team, purchase one copy per user.
Order for your team and save!

IMAGES
VIDEO
COMMENTS
Although Kodak’s design differed from Polaroid’s in numerous ways, Polaroid filed suit against Kodak mere months after the release of the new products for the infringement of 12 Polaroid patents, accusing Kodak of illegally incorporating instant photography technology into their products.
Describes Kodak's long-awaited challenge to Polaroid in the field of instant photography. Provides technological and company background of both Polaroid and Eastman-Kodak and their respective product lines. Discusses Polaroid's claim that Kodak infringed on 10 Polaroid patents.
A US District Court judge in Boston ruled that Eastman Kodak Co. infringed on seven Polaroid patents that are key to instant photography, Polaroid's core business. The decision closes at least one chapter in a nine-year legal battle between the two photography giants.
Describes additional events in battle between Polaroid and Kodak outlined in Polaroid-Kodak. Includes the competitive actions taken by the companies such as the introduction of customer rebates and bonus plans with dealers.
Polaroid Corporation, the assignee of numerous patents in the field of instant photography, brought this action against Eastman Kodak Company for infringement of twelve of its patents relating to the art/technology of both film and camera. Kodak denied infringement and alleged that all of the patents are invalid or unenforceable or both.
Polaroid sought trebled damages of $12 billion, claiming it suffered severely at Kodak’s hands through loss of market share and unfair price competition. But Kodak said it had only cost...
Fourteen and a half years in court ensued, and Polaroid won. Kodak had to write a check for the largest settlement ever paid out in a patent trial—$925 million—and Judge Rya Sobel, in a serious rebuke, barred the company from the instant-photo business altogether.
This case is a study in how NOT to enter a competitive market against an incumbent with competitive advantages like Polaroid. Detail Polaroid’s competitive advantages in the instant photography market
This document provides a case study comparison of how Kodak and Polaroid responded to the rise of digital photography technologies. It describes the technological, market, and organizational capabilities of each company prior to digital photography.
Describes Kodak's long-awaited challenge to Polaroid in the field of instant photography. Provides technological and company background of both Polaroid and Eastman-Kodak and their respective...