Schneider Electric Blog
Home > Industry > Machine and Process Management > An Introduction to SCADA Systems

An Introduction to SCADA Systems
December 11, 2018
2 min read | Atin Chhabra
JavaScript is required to use the TTS Player.
This audio was created using Microsoft Azure Speech Services
What is SCADA System?
SCADA System refers to Supervisory Control and Data Acquisition System. Primarily, it is a network of all the machinery and equipment in the system connected through a centralised hub. The hub acquires all the data from the site. It includes information like machine status, process status, health of the machine, its throughput etc.
Functions of SCADA
All the equipment connected through machine control are operated through instruction sent over the web. The processing unit analyses the data and supervises the healthy functioning of the signals transmitted in the entire unit. The data is stored for valuation in a distributed database. The acquired data also has reference metadata stored for in the different database such as a programmable logic controller ( PLC ).
How does it work?
The complete SCADA systems has four significant units namely – data communication, data acquisition, information or data presentation and monitoring and control system. With complete symphony in the above four mentioned units, the entire operation of the automation system can be monitored. The data acquisition system fetches real-time data from all the connected machine units. The data reports about the status of all the components and sensors, where data communication network comes into play. The system ensures accuracy in data being transferred through the internet protocol. Once the data is collected, the processing unit analyses the data and presents it to the operator through Human-Machine Interface ( HMI ).
The comprehensive system works in close connection with predictive maintenance also. The data relayed by communication system after processing is also analysed by this system to detect any shortcomings that may occur in the system. This reduces the susceptibility of system breakdown or expected downtime due to a faulty line.
Application of the System
Although this is a new technology, businesses have already leveraged the technology in both the public and private sector. It has brought about immense satisfaction in the operation managers because the system makes the production line foolproof. This also streamlines packaging and delivery lines following the processes. The overall automation and process control has helped to save a significant amount of money and time. This is the reason why many more enterprises are looking for automating their industrial processes. With the Industrial Internet of Things taking the front seat, it is essential to look for companies helping businesses step towards automation. Schneider Electric India is one of the significant names in the research and development of the automation industry. It has not only brought these systems to common units but also helps the employees to upskill their knowledge by training them how to operate the machinery.
I hope this article equipped you with all the knowledge you were seeking about SCADA System! Comment below if you feel that we’ve missed on anything or if there is something more you want to know.
#SchneiderElectric #LifeIsOn

SCADA vs IoT: the Role of SCADA Systems in Manufacturing’s Industry 4.0
What is SCADA Systems?

Water Security: The Role of SCADA Systems

3 facts You Need to know about SCADA Systems
Are you sure you want to log out of Unmudl?
Understanding scada systems: an in-depth guide.
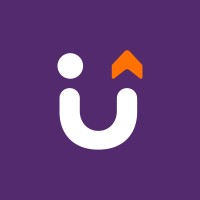
Key Takeaways
Many often consider Supervisory Control and Data Acquisition (SCADA) systems the backbone of modern industrial operations. They are the silent architects behind the scenes, orchestrating complex processes with precision and finesse. This article aims to elevate your understanding of the nuanced aspects of SCADA systems, which drive efficiency, safety, and reliability in industrial settings.
What are SCADA Systems?
SCADA systems are a type of industrial control system (ICS) used for monitoring and controlling infrastructure and facility-based processes. These systems gather real-time data from sensors and equipment, allowing operators to control and manage industrial operations remotely. SCADA systems have revolutionized industrial operations in energy, oil and gas, water management, and manufacturing sectors.
The versatility of SCADA is evident in its ability to adapt to various industrial environments. This adaptability ensures the smooth running of complex processes across different sectors. SCADA systems have seen continual development, with newer technologies enhancing their capabilities and integration with other industrial systems.
.webp)
History and Evolution of SCADA
SCADA systems have evolved significantly since their inception in the 1960s. Initially, these systems were simple, isolated, and with limited functionality. Over the years, however, SCADA has transformed into a sophisticated, interconnected system, employing advanced technologies like the Internet of Things (IoT) and cloud computing.
The 1980s and 1990s saw a significant shift with the integration of computer technology, making SCADA more powerful and versatile. This period marked the beginning of using real time data for better industry decision-making. Today's SCADA systems are far from their predecessors in terms of enhanced security, scalability, and interoperability features.
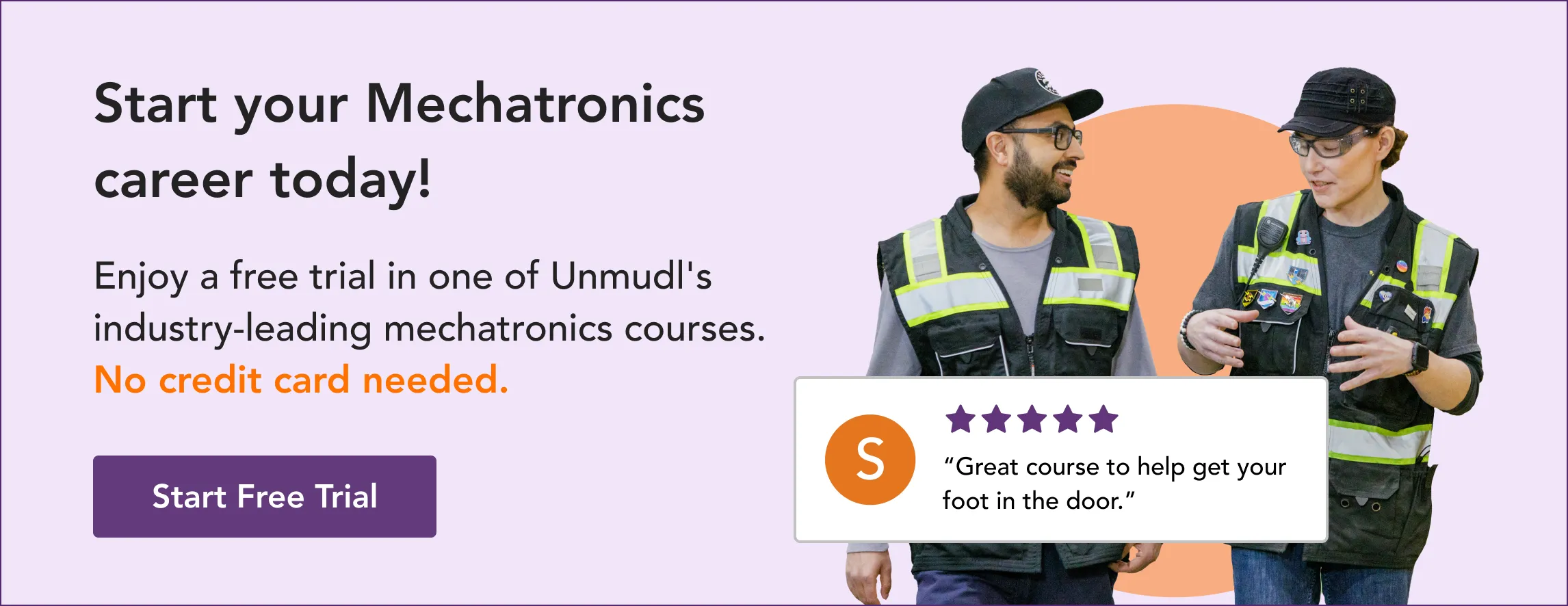
Interested in switching to a different trade?
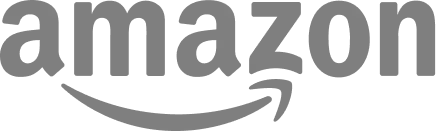
Not happy with your apprenticeship?
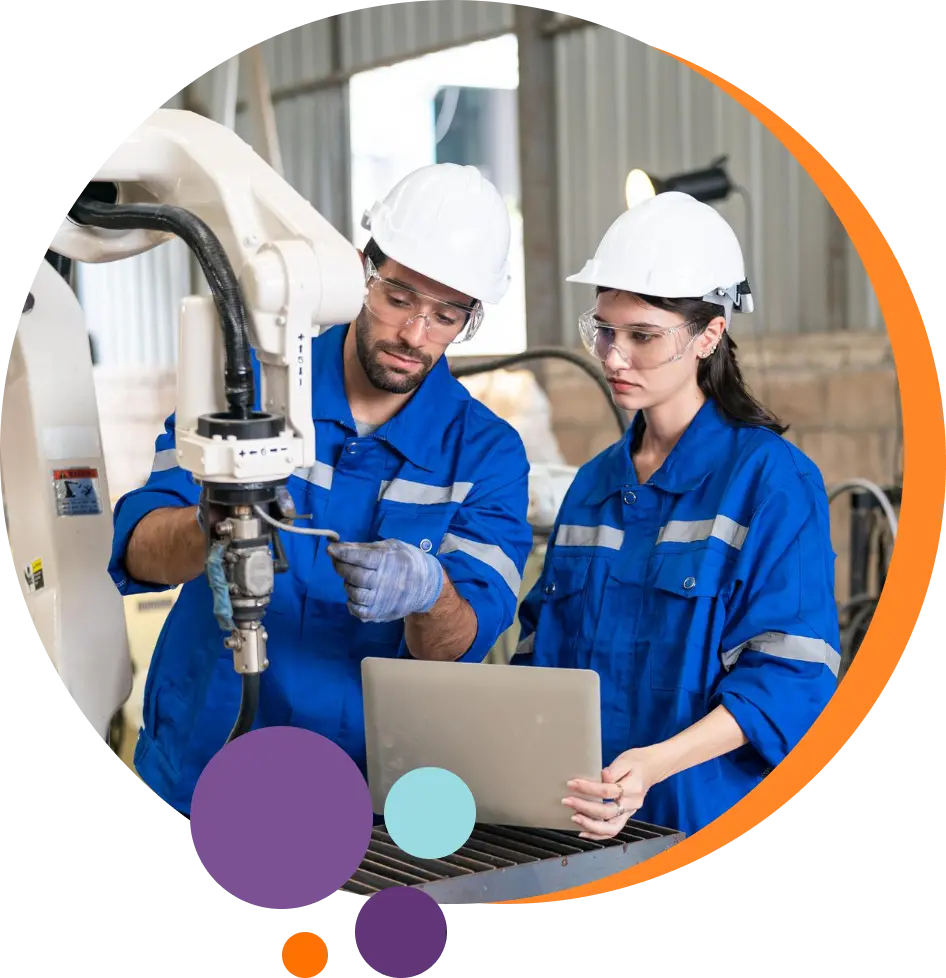
Want to get started in Mechatronics?
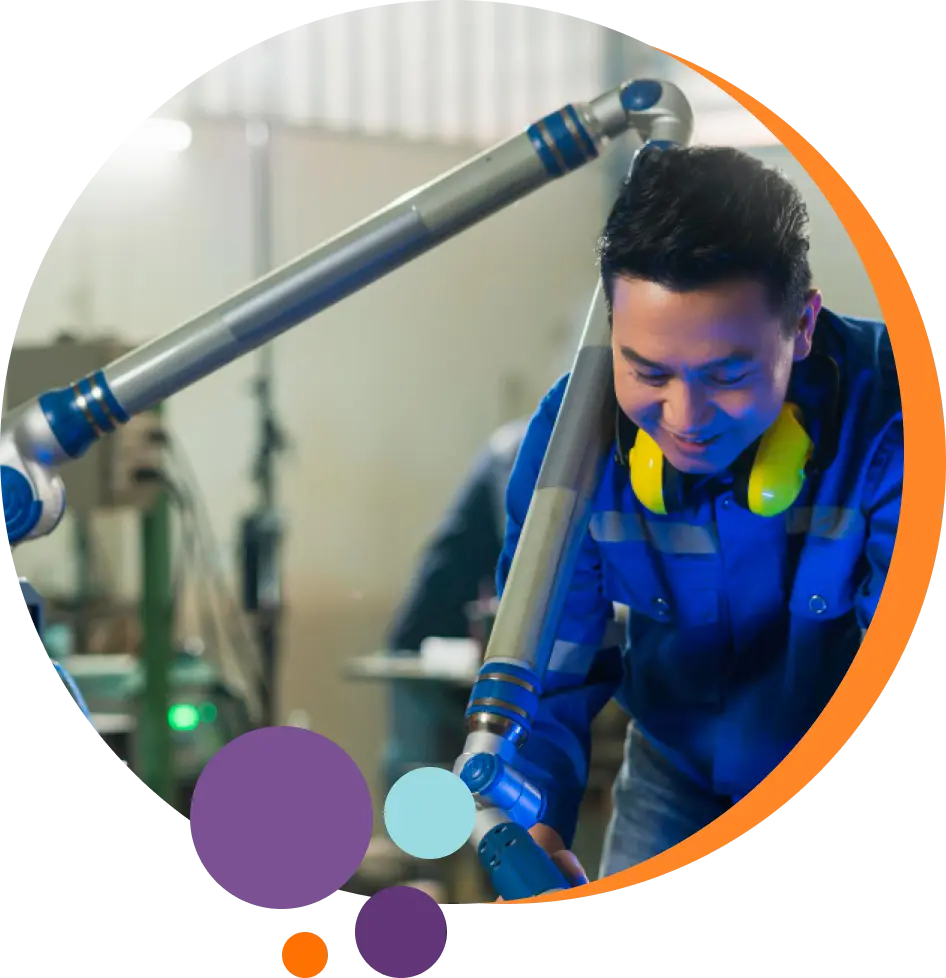
Don’t want your job to be replaced by AI?
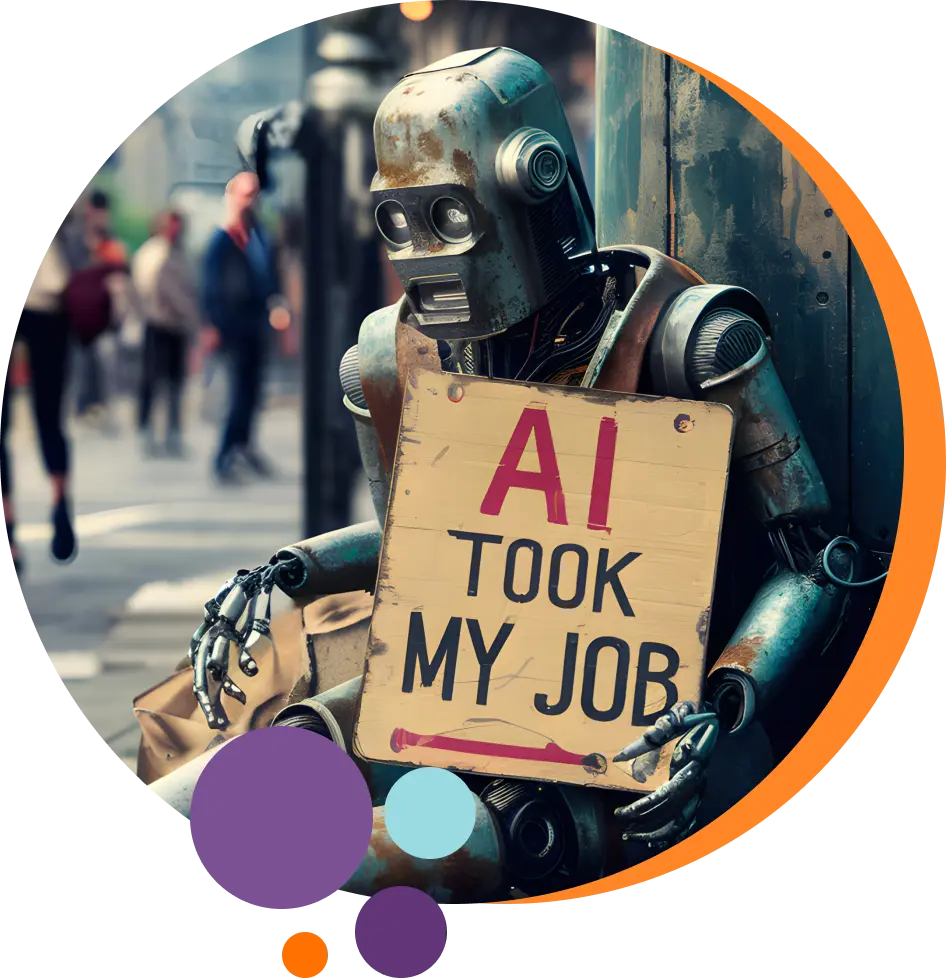
Want to get started as a technician?
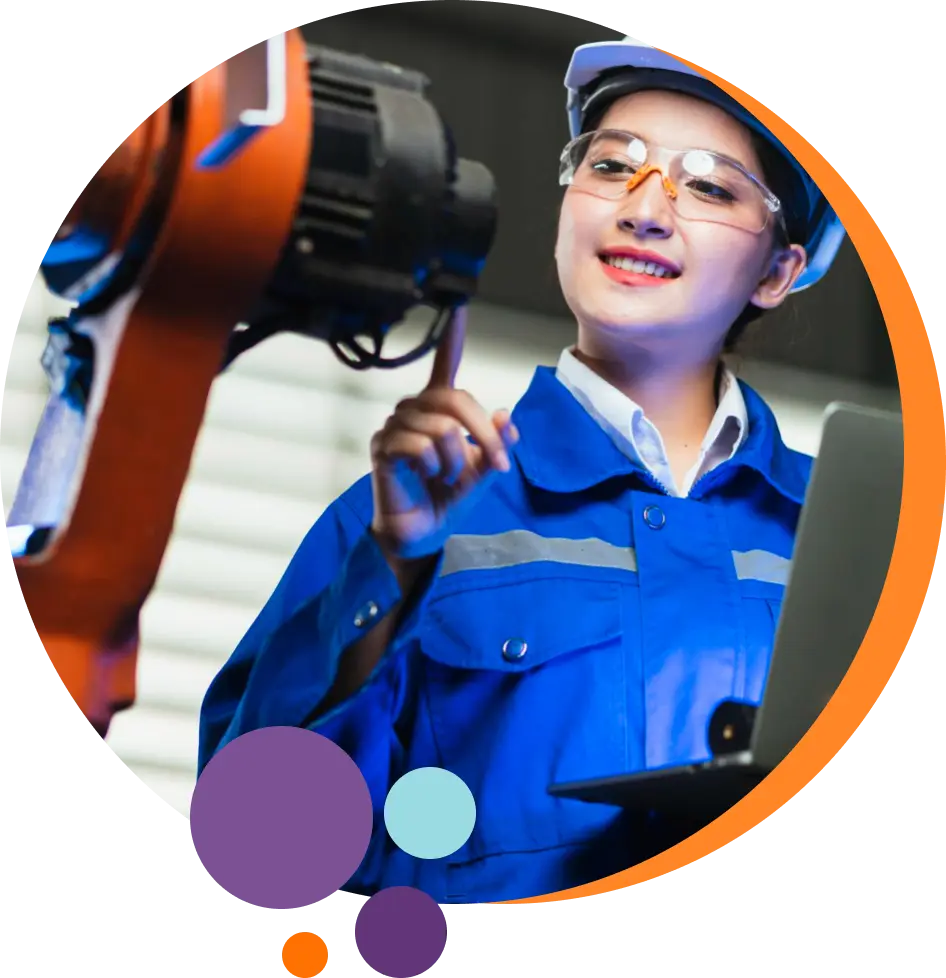
Want to get started as a Maintenance Technician?
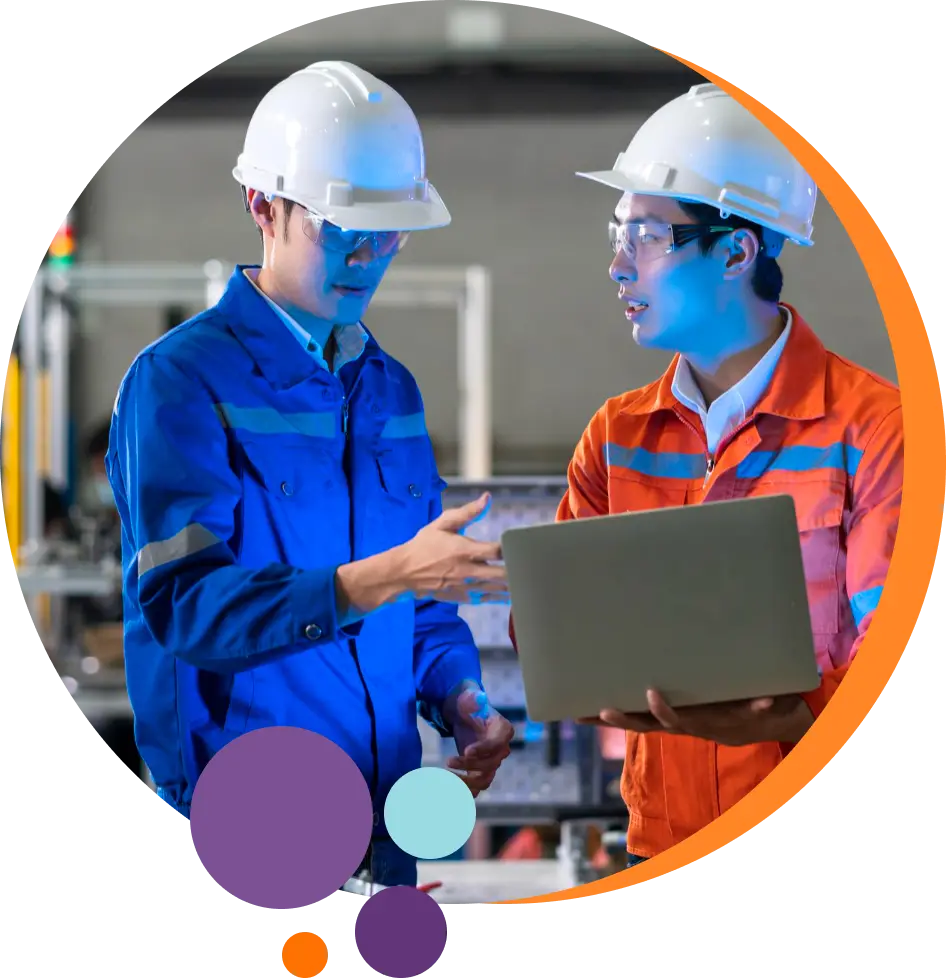
Want to get started as a Controls Technician?
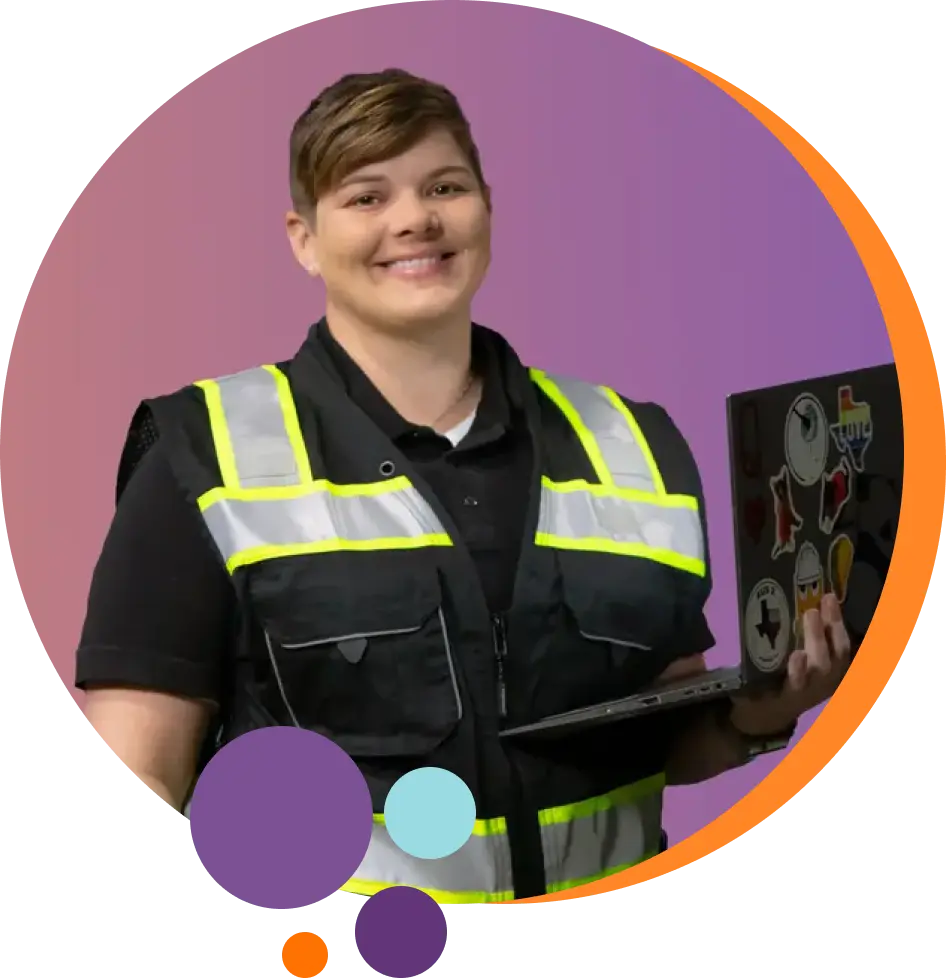
Want to get started as a Robotics Technician?
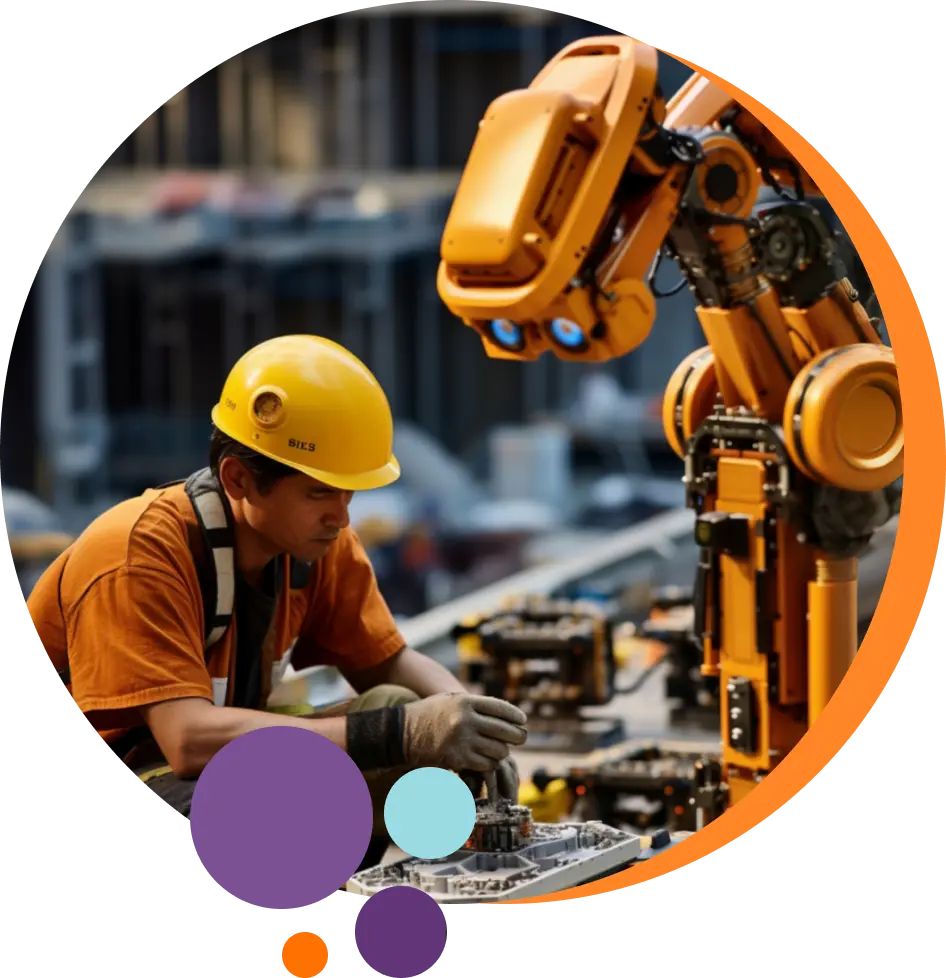
Interested in a high paying trade job?
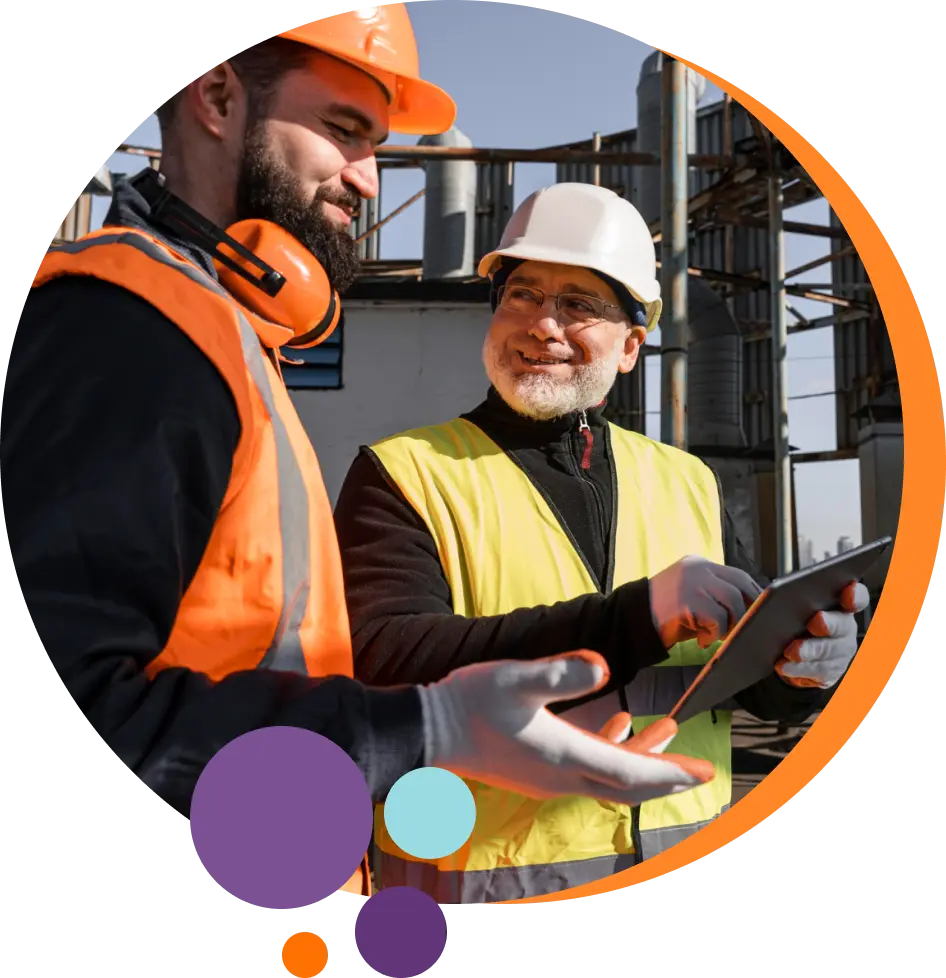
Core Components and In-Depth Understanding of SCADA Systems
A typical SCADA system comprises several key components, each integral to its operation. These include sensors and actuators, Remote Terminal Units (RTUs), Human-Machine Interface (HMI), and a central control system. The synergy of these components is what makes a SCADA system efficient and reliable.
Sensors and actuators are the primary elements in gathering and acting on field data. Sensors monitor environmental conditions such as temperature, pressure, and flow rates, converting these physical parameters into digital data for the SCADA system.
Actuators are the doers in the system, executing control actions based on commands from the supervisory computers. They represent the action arm of the system, responding to the analyzed data to effect changes in the field.
The role of supervisory computers in a SCADA system is akin to that of a central processing unit in a computer. They are the core of the SCADA system, where critical data processing and decision-making occur. They gather data from the field sensors, analyze it to make operational decisions, and send back commands to actuators and field controllers. This data collection, analysis, and response loop forms the backbone of SCADA's functionality, ensuring the smooth operation of complex industrial processes.
RTUs are another crucial component that works as intermediaries between field devices and the central system. They ensure seamless data communication by linking sensory inputs from the field to the analytical prowess of the central control system. The HMI, meanwhile, provides a user-friendly platform for operators to interact with the SCADA system. It displays data in an accessible format, allowing for efficient monitoring and control of the industrial processes.
Types of SCADA Systems
SCADA systems have evolved remarkably, transitioning through various stages, each signifying a leap in technology and functionality. Let us explore the different types of SCADA systems by tracing their historical development and the advancements each type brought to the field.
Monolithic SCADA Systems
The earliest SCADA systems were monolithic in design. These first-generation systems were centralized to operate on mainframe computers. Their functionality was limited to monitoring and controlling processes within a single facility.
Due to their architecture, these systems lacked the flexibility and scalability of later generations. They were confined to specific locations and had limited connectivity options.
Distributed SCADA Systems
The second generation of SCADA systems saw the advent of distributed architecture. These systems introduced decentralized control and data collection, allowing for a more flexible and scalable approach.
Distributed SCADA systems could manage more complex operations and handle larger amounts of data more efficiently. This generation marked a significant step toward modern SCADA, with improved data handling and control capabilities across various locations.
Networked SCADA Systems
The third generation introduced networked SCADA systems. These systems integrated various IT and control systems by utilizing modern communication technologies Networked SCADA systems are characterized by their use of Ethernet and other advanced communication protocols that enhance their flexibility, security, and efficiency. They brought improved interconnectivity, allowing different systems to communicate and exchange data seamlessly and overcome the limitations of the previous generations.
IoT-Integrated SCADA Systems
The latest evolution in SCADA systems incorporates IoT technologies. These fourth-generation systems leverage cloud computing and big data analytics to offer unprecedented flexibility, efficiency, and scalability. IoT SCADA systems represent a paradigm shift in industrial control, where a network of interconnected intelligent devices performs control and monitoring functions. This integration enables more sophisticated data analysis, predictive maintenance, and a higher degree of automation and operational insight.
.webp)
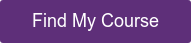
We help people like you find new careers they love!
The critical role of scada in various industries.
SCADA systems play a pivotal role in many industries, demonstrating their adaptability and efficiency in various settings.
SCADA Applications Across Industries
SCADA systems are integral to the functionality and efficiency of multiple industries. They are essential in managing complex energy grids, automating intricate manufacturing processes, and ensuring the smooth operation of water management systems. In the transportation sector, SCADA systems contribute to the reliability and safety of operations.
Their versatility makes them indispensable for sectors that require precise control and monitoring, such as power generation, utility management, and industrial manufacturing. SCADA's ability to process and analyze vast amounts of data in real-time is crucial in these environments and leads to more informed decision-making and enhanced operational efficiency.
Real-world Impact and Case Studies
Numerous case studies demonstrate the substantial benefits of implementing SCADA systems in various industries. In the energy sector, for instance, SCADA systems have been instrumental in optimizing grid management, leading to improved energy distribution and reduced outages. In manufacturing, integrating SCADA systems has resulted in enhanced safety protocols by minimizing worker risks and hazards.
Water treatment plants have seen significant improvements in efficiency and compliance with environmental standards, thanks to the precise monitoring and control capabilities of SCADA systems. These real-world applications underscore the system's ability to bring about significant cost savings and operational improvements, underlining its value as a critical tool in modern industrial operations.
Functions and Applications of SCADA
SCADA systems provide vital functions like data acquisition, networked data communication, and data presentation. These systems are designed to gather critical information, facilitate real-time data exchange, and present the data in an accessible format for decision-making.
In terms of applications, SCADA is used in diverse fields. From managing energy distribution networks to controlling water treatment plants and from overseeing manufacturing processes to monitoring transportation systems, SCADA applications are widespread.
Technological Advances in SCADA
The integration of cutting-edge technologies has dramatically enhanced SCADA systems. IoT, for instance, has expanded the capabilities of SCADA to enable more comprehensive data collection and analysis. Cloud computing has also played a role in offering scalable and flexible data storage and processing solutions.
With the advent of Artificial Intelligence (AI) and machine learning, SCADA systems are now more intelligent and capable of predictive maintenance and anomaly detection. This evolution increases efficiency and significantly reduces downtime and operational costs.
SCADA in the Context of Cybersecurity
Cybersecurity is a major concern for SCADA systems, especially given their critical role in infrastructure. SCADA systems now have advanced security features to prevent unauthorized access and cyber-attacks. Regular updates, patches, and rigorous security protocols are essential to safeguard these systems.
The Stuxnet incident in 2010, where a malicious worm targeted SCADA systems, highlights the need for robust cybersecurity measures. Since then, there has been a heightened focus on securing SCADA systems against cyber threats.
.webp)
SCADA's Role in Environmental Monitoring
SCADA systems are also instrumental in environmental monitoring. They help track environmental parameters and ensure compliance with environmental regulations. In water treatment plants, for instance, SCADA systems monitor and control the levels of various chemicals to ensure the safety and quality of the water.
In the energy sector, likewise, SCADA systems are used for monitoring emissions and ensuring plants adhere to environmental standards. This helps protect the environment and aid sustainable operations.

The Future Outlook and Potential of SCADA Systems
SCADA systems stand on the brink of a new technological integration and innovation era.
Integration of Advanced Technologies in SCADA
Integrating AI and big data analytics represents a significant future trend for SCADA systems. These technological advancements are set to enhance the predictive capabilities of SCADA, allowing for more proactive and efficient management of industrial processes. The ability to predict and preemptively address potential issues before they escalate will revolutionize how industries manage and maintain their operations.
The Role of SCADA in Smart Cities and Renewable Energy
SCADA systems are also becoming pivotal in developing and managing smart cities . With the trend toward urbanization, SCADA's potential to contribute to more efficient city management is significant. From optimizing traffic control to streamlining public utilities management, SCADA will be at the heart of smart urban infrastructure.
Emerging Technologies Enhancing SCADA Systems
Emerging technologies like augmented and virtual reality are also expected to be integrated into SCADA systems. These technologies could provide enhanced operational visibility and offer advanced training tools, making complex processes more accessible and understandable for operators. This integration will likely improve the efficiency and safety of operations, particularly in complex and hazardous environments.
SCADA in the Integration of Renewable Energy Sources
As renewable energy sources become increasingly prevalent, SCADA systems will play a crucial role in integrating these sources into existing energy grids. This integration is vital for ensuring a stable and reliable energy supply as the world transitions to more sustainable energy solutions. SCADA's ability to monitor and manage diverse energy sources will be critical in achieving this balance.
How SCADA Systems Transform Industrial Operations
This section explores the dynamic role of SCADA systems in revolutionizing industrial operations.
SCADA System Functionality
SCADA systems transform raw data into actionable insights for efficient operation management. They collect data from various sensors, process it, and present it on HMIs for operators to make informed decisions. This functionality extends to controlling various industrial parameters such as temperature, pressure, and flow rates.
Flexibility and Configurability of SCADA Systems
The configurable nature of SCADA systems allows for tailored solutions across different industries. Whether managing a water treatment facility or monitoring a manufacturing process, SCADA systems can be adapted to meet specific operational needs, enhancing their utility across various sectors.
.webp)
Embracing SCADA in Modern Industries
SCADA systems are a foundational element of the modern industrial landscape. Their role in enhancing efficiency, reducing costs, and improving safety cannot be overstated. For individuals and industries alike, understanding and utilizing SCADA systems is vital to keeping pace with the rapidly evolving world of industrial automation .
These systems streamline operations and open new avenues for innovation and development in various sectors. Embracing SCADA is about moving forward with the future of the industry.
Elevate Your Career in Industrial Automation
If you're intrigued by the possibilities of SCADA systems and the advancements in industrial automation, now is the time to enhance your skills and knowledge in this field. Exploring courses in Reliability Maintenance Engineering and Mechatronics can be your gateway to exciting opportunities in this dynamic sector. These fields offer the right blend of theoretical knowledge and practical skills, preparing you for a rewarding career in industries that rely heavily on SCADA systems.
Equip yourself with the tools and knowledge necessary to excel in a world increasingly driven by advanced industrial automation. Embrace this chance to be a part of the future. Sign up at Unmudl today and start shaping your future in the dynamic world of industrial automation.
Frequently Asked Questions
Contributor(s).
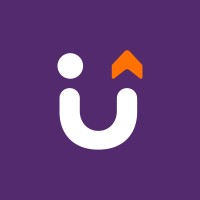
The Unmudl Skills Team is a team of experts with decades of experience in helping learners acquire the skills needed to secure meaningful employment in the workforce.
More Articles
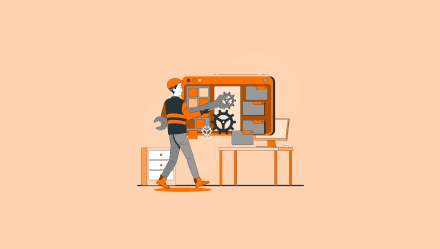
Navigating the Roadmap to an Engineering Career in Mechatronics
.webp)
Is Mechatronics a Good Career?
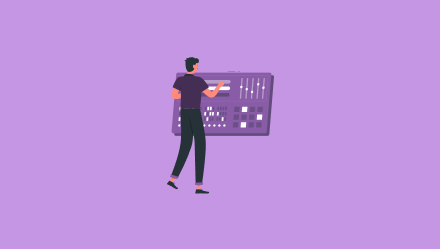
Becoming a Control Systems Lead: Unlocking a Promising Career Path
PLCGurus.NET
Fastest growing community of automation professionals.

What is SCADA? Data Acquisition Systems Explained
What does SCADA stand for? SCADA stands for S upervisory C ontrol A nd D ata A cquisition.
What Is SCADA and How Does It Work?
The definition of SCADA is pretty self-explanatory:
The function of a SCADA system is to Supervise, Control, and manage Data Acquisition.
A SCADA system may include:
- At least one computer or server. The computers are connected to each other over a network to perform supervisory functions, while also implementing human-machine interfaces (HMIs).
- A series of peripheral devices including but not limited to RTUs (remote terminal units), Input and Output Modules, and others intelligent devices that interface the machinery, plant, and processes via actuators and sensors.
- A communication network that includes a variety of communication protocols and transmission media. This network functions to ensure the correct transmission of information between peripheral devices and computers.
And the following subsystems are usually present in a SCADA system:
- Programmable Logic Controllers (PLCs) that are deployed as field devices
- Interface (i.e. display) used by an operator. The data acquired from the process is displayed in this interface
- A supervisory system that collects all the data from and about the process
- Remote Terminal Units (RTUs) connected to sensors. They help to convert the signals gathered by the sensors to digital data to be processed by the supervisory system.
- A communication network (i.e. LAN), connecting RTUs to the supervisory system
SCADA software is an integrated development environment that provides all the required tools to develop SCADA applications and software.
These applications and software are designed to run on supervisory computers that perform the core Supervision, Control, and Data Acquisition functions of a SCADA system, which we will discuss below.
Supervision
The function that allows operators to have an immediate view of the process at hand so they can control the progress of the processes over time by monitoring and analyzing the sequence of states.
The main objective of Supervision is to provide an HMI (human-machine interface) or multiple HMIs.
To be effective, the HMI must provide the operator with a complete and accurate visualization of the whole process, allowing the operator to monitor the status, the evolution of states, and unexpected deviations (potential issues and bottlenecks).
For an effective HMI, graphic visualization of the process is very important. Translating the relevant information of the process to an easy-to-understand visual language is paramount.
For instance, the software can display the status of manufacturing equipment through an easy-to-use graphic symbol complete with color codes.
When an unexpected deviation occurs, the interface will display an alarm notification via a pop-up window.
The Control function in a SCADA system refers to the ability of the system to interact with a controlled process so it can modify the evolution of states according to pre-established policies or manual decisions taken by the operator.
It’s important to note that ‘control’ in a SCADA system doesn’t refer to real-time process control typical to PLCs, but rather emphasizes the ability to modify the evolution of states in a process.
To better understand the difference, let’s use an example of air pressure in a process.
In PLC real-time control, the objective is to keep this pressure unchanged throughout the whole process, for example by controlling the appropriate actuators.
On the other hand, the objective of SCADA control is to modify the pressure in which the process should work by sending an appropriate command through the SCADA software.
- Data Acquisition
Data Acquisition in a SCADA system is arguably the main function, and arguably outweighs the other two functions just discussed.
Data Acquisition refers to the two-way transfer of information from field devices and the supervisory computer. This allows the supervisory computer to control the processes as discussed above in the Control section.
By putting the Data Acquisition system in constant communication with the Supervision system, the supervisory system can collect all the necessary information to allow monitoring and observation of the process as a whole.
The objective of Data Acquisition is to ensure the error-free transmission of data and information between processes to allow for complete supervision.
How a SCADA System Works
To really understand how a SCADA system work, we have to understand how the system’s hardware and software aspects work.
SCADA Hardware Architecture
When discussing the hardware aspect of the SCADA system, generally we can divide it into two different layers: the client layer and the data server layer.
The client layer, as the name suggests, handles the human-machine interactions of the SCADA system, while the data server layer handless data acquisition and data processing.
The SCADA station (a single PC) connects directly to a database server. This database server communicates with devices in the field through PLCs, RTUs, or other controllers. These controllers will then connect to the field devices like sensors.
In a SCADA system, we can connect PLCs to the data servers directly (i.e. via ethernet connection) or via networks. The RTUs convert the sensor signals to digital data so it can be read and processed by the supervisory system.
According to the feedback received by the RTU or PLCs, it will then apply electrical signals to control the process.
SCADA Software Architecture
The software aspect of the SCADA system is responsible for monitoring changes in the process and perform analysis to find trends and patterns. The software will then manage information such as logistics data, scheduled processes, and troubleshooting. The software system allows the operator to properly monitor a visual representation of the data provided by the process.
SCADA Operation Workflow
In a SCADA system; sensors, PLCs (or other controllers), RTUs, and a communication network (i.e. LAN or WAN) are working together to perform the following functions:
- Data Communication
- Data Presentation
- Monitoring of Data
To be more precise, the sensors collect data/information and RTUs will then send this data to the PLC controller so the interface can display the status of the system.
According to the information displayed in the interface, the operator can give a command to other system components. All of these are made possible by the communication network.
Different Types of SCADA System
In its history, there have been four different types, or generations:
- Early or Monolithic SCADA systems (first-gen)
- Distributed SCADA systems (second-gen)
- Networked SCADA systems (third-gen)
- IoT SCADA systems (fourth-gen)
Early SCADA Systems
In the first generation of SCADA systems, minicomputers are used to connect directly to RTUs.
During this time network services are not yet available, so the early SCADA systems are mostly independent without much connectivity to other systems.
All RTUs in an early SCADA system would connect to a back-up mainframe system, which is very important to achieve redundancy.
The early SCADA systems are mainly limited to monitoring sensors and sending flags to operators in cases when a certain threshold has been detected by the sensors.
Distributed SCADA Systems
In a second-generation, distributed SCADA system, LAN (Local Area Network) is used to share the control functions across multiple systems.
Individual SCADA stations were used to share real-time information and command processing for controlling processes.
With this model, the cost and overall size of the system were reduced compared to the first-generation systems.
However, network protocols were not standardized in this period, so the security of the SCADA system was mainly ignored.
Networked SCADA Systems
Most SCADA systems at the moment communicate via WAN (Wide Area Network) via Ethernet, Fiber Optic, or WiFi. Third-generation SCADA systems also utilize PLCs for monitoring and controlling purposes.
While the first and second-generation of SCADA systems are mainly limited to a single-site network as a closed system, we can now have several parallel-working SCADA systems under a single operator in the network architecture.
IoT SCADA Systems
The latest generation of SCADA system now makes use of the concept of the Internet of Things (IoT).
IoT provided a mechanism to scale SCADA systems to be much larger than the previous generations. At the same time, it reduced the overall cost of implementing a SCADA system by utilizing cloud computing.
Maintenance, implementation, and integration are also much easier in an IoT SCADA system compared to earlier generations.
By utilizing IoT concepts, the SCADA system can now report the evolution of process states in real-time by using cloud computing, which also allows more complex control algorithms to be implemented on the PLCs.
Security-wise, we can also use open network protocols (like TLS) to replace proprietary network protocols in previous generations, which will also allow more manageable security functions.
Popular Software Used for SCADA
Ignition scada.
Ignition SCADA by Inductive Automation offers an industry-leading toolset for SCADA functionalities on a scalable universal platform.
The software comes with an excellent set of data acquisition tools like OPC UA that can connect to virtually any PLC, and can seamlessly connect to any SQL database.
With Ignition SCADA, you can also seamlessly connect to IoT devices via MQTT open messaging.
CloudView NMS
CloudView is a standards-based NMS (network management and monitoring system), which also allows SCADA monitoring besides other useful monitoring functions like server monitoring, IoT monitoring, website monitoring, and so much more.
CloudView NMS allows a consistent logical and geographical view of your network, reliable monitoring, and real-time troubleshooting.
Open Automation Software
Open Automation Software, or OAS, is a very versatile platform where you can connect directly to your PLCs, databases, OPC servers, and IoT platforms to create virtually any SCADA systems you can think of and any industrial automation.
Offers unparalleled connectivity between PLCs, databases, and custom apps with data transport support from any data source to any destination while enabling data acquisition and real-time alarm/notification.
VTScada by Trihedral offers a very intuitive platform where you can create custom-tailored SCADA applications that end users can easily and reliably use, anytime.
VTScada is an HMI software that can communicate via a network to distributed RTUs and PLCs to control remote hardware and retrieve process data.
As you can imagine, this was a very introductory article on what SCADA is and what makes up a Supervisory Control and Data Acquisition system.
If you enjoyed reading this article, consider some of these great reads as well:
- NEMA Enclosure Ratings Explained
- 10 Best Multimeters for Electricians
- What is a Servo Motor? Motion Control Basics
- What is an Actuator? Actuator Types Explained

IMAGES
COMMENTS
SCADA stands for “Supervisory Control and Data Acquisition.” It is a control system that uses computers, networked data communications, and graphical Human Machine Interfaces (HMIs) to manage and control industrial processes.
The complete SCADA systems has four significant units namely – data communication, data acquisition, information or data presentation and monitoring and control system. With complete symphony in the above four mentioned units, the entire operation of the automation system can be monitored.
Data presentation is achieved through HMIs, which represent current and historical data to the operators running the SCADA system. Real-time and historical data are both important parts of the SCADA system, as they enable users to track current performance against historical trends.
A SCADA system performs four functions: 1. Data acquisition 2. Networked data communication 3. Data presentation 4. Control SCADA Subsystems A Human-Machine Interface or HMI is the apparatus which presents process data to a human operator, and through this, the human operator monitors and controls the process.
SCADA systems are a type of industrial control system (ICS) used for monitoring and controlling infrastructure and facility-based processes. These systems gather real-time data from sensors and equipment, allowing operators to control and manage industrial operations remotely.
Data Acquisition in a SCADA system is arguably the main function, and arguably outweighs the other two functions just discussed. Data Acquisition refers to the two-way transfer of information from field devices and the supervisory computer. This allows the supervisory computer to control the processes as discussed above in the Control section.